In the demanding environments of various industries, the significance of a well-functioning cooling system cannot be overstated. An industrial water chiller operates as a vital piece in this puzzle, safeguarding both the productivity and integrity of many industrial operations.
What is A Water Chiller?
A chiller is a machine that cools down spaces or materials. It uses a special fluid called a refrigerant, which flows through several parts like a compressor and a condenser. All these parts work together to pull heat away from a specific area or process, helping to keep temperatures steady and within a set range.
The Working Mechanism of Water Chillers
Core Principles of Operation
Industrial chillers operate using one of two central principles: heat absorption or vapor compression.
To appreciate their crucial role in various industries, let’s delve into how these principles harmonize with the main components of a chiller.
Heat Absorption Method
Heat absorption chillers use heat exchangers to effectively pull heat away from different processes, releasing it into the surrounding environment. These exchangers mainly consist of a series of pipes filled with cooling fluids – a mixture of air, water, or a combination of water and other liquids. The ultimate goal is to lessen the heat and create a suitable setting for various industrial operations.
Vapor Compression Method
Conversely, vapor compression chillers cool down processes by moving a coolant through pipes that are part of systems needing cooling. This movement absorbs heat from the processes, transferring it into the coolant, which then moves to a refrigeration system. In this system, the coolant is cooled down, readying it for another cycle of process cooling.
The Refrigeration Cycle
At the heart of a chiller system are four main components: the evaporator, compressor, condenser, and expansion valve, all housing a refrigerant crucial to its functioning.
The process begins with the low-pressure refrigerant entering the evaporator where it absorbs heat, transitioning into a gaseous state. This gas then moves to the compressor, where its pressure significantly rises.
Next, the high-pressure refrigerant flows to the condenser. During this stage, the condenser releases the absorbed heat, utilizing either water from a cooling tower or air from the surroundings, and transforms it into a high-pressure liquid. This liquid then advances to the expansion valve, a specific component that regulates the refrigerant flow, kickstarting a new cooling cycle. This continuous loop is the backbone of the refrigeration cycle, fundamental to an industrial chiller’s operations.
4 Key Components
- Compressor: The central role of the compressor is to convert the refrigerant from a low-pressure, low-temperature state to a high-temperature, high-pressure gas state. Common types of compressors include centrifugal, turbocor (scroll), and screw types.
- Condenser: In the condenser phase, the hot high-pressure gas flows through coils, where it encounters a flow of water or air over the coils. This interaction helps to extract heat from the refrigerant, causing it to lose heat and condense into a liquid form.
- Evaporator: During the evaporator stage, the refrigerant transitions back into a gaseous state, becoming significantly colder and acting as a heat absorber. This phase is crucial as it involves the direct heat transfer from the fluid to the refrigerant. The common types of evaporators include copper coil, shell and tube, and plate types.
- Expansion Valve: Also known as a thermostatic or electronic expansion valve, this component controls the amount of refrigerant flowing between the condenser and the evaporator. It dynamically adjusts the refrigerant flow to meet the current cooling needs.
Other External Components Needed
- Cooling Towers: Essential in water-cooled chiller systems, cooling towers assist in releasing the heat absorbed by the refrigerant into the surrounding atmosphere.
Water Cooling Tower - Pumps: Incorporating pumps like chilled water pumps and condenser water pumps are necessary for the continuous circulation of the cooling fluid and refrigerant throughout the chiller system.
- Piping System: A well-designed piping system is crucial to interlink different components, ensuring seamless flow of refrigerant and cooling fluids across the system.
- Electrical Control Panels: These panels are vital to the efficient operation of the chiller system, hosting controls and switches for safe, monitored, and automated functionality.
- Heat Exchangers: Depending on the system configuration, additional heat exchangers might be incorporated to enhance the efficiency of heat transfer or recovery processes.
- Storage Tanks(buffer tanks): These tanks serve as reservoirs for chilled water or other fluids, aiding in managing fluctuating cooling loads and guaranteeing a constant supply of chilled water.
- Chemical Treatment System: To uphold the water quality within the system, a chemical treatment setup is often necessary to prevent issues such as scaling, corrosion, and microbial growth.
Different Types of Industrial Chillers
Selecting the appropriate chiller is critical and comes with a wide array of options, each tailored to the unique requirements and specifics of different industries. Gaining insights into the distinct types of industrial chillers on the market is, thus, vital. Here, we explore the classifications of these chillers based on cooling mediums, compressor types, vapor categories, and specialized applications:
Cooling Media
- Air-Cooled Chillers: Best suited for areas with scarce water resources, these chillers use ambient air to discharge heat, mainly finding use in medium-sized industries due to their relatively easy maintenance.
- Water-Cooled Chillers: Perfectly suited for facilities with abundant water resources, these chillers utilize water as a medium to effectively absorb and dispel heat in the condenser, making them a favored choice in expansive industrial setups.
Compressor Type
- Scroll Chiller: Known for their quiet functioning and high efficiency, scroll compressors are a common choice for smaller facilities, offering dependability with less maintenance concerns.
- Screw Chiller: A fixture in medium to large operations, screw compressors offer a fine balance between efficiency and reliability, expertly managing substantial cooling loads.
- Centrifugal Chiller: Primarily found in large-scale industrial setups, centrifugal compressors excel in delivering massive cooling capacity while maintaining energy efficiency.
- Reciprocating Chiller: Showcasing adaptability, reciprocating compressors are utilized in a broad spectrum of applications, delivering robust performance even in stringent conditions.
Vapor Type
- Absorption Chillers: Operating on the fundamental principle of heat absorption, these types of chillers are particularly favored for their capacity to efficiently harness waste heat, thereby promoting a more environmentally friendly method of operation. They stand as a viable option in scenarios where electrical power is limited or expensive, channeling waste heat as a primary energy source and thus fostering a sustainable operational framework.
- Vapor Compression Chillers: Anchoring many industries with their high efficiency and reliability, these chillers are imperative where meticulous temperature control is a prerequisite.
Specialized Applications
- Explosion-Proof Chillers: Designed for environments harboring volatile substances, these chillers come equipped with features to prevent sparks and explosions, thereby ensuring safety in hazardous industrial settings.
- Low-Temperature Chillers: Tailored for industries necessitating ultra-low temperatures, these chillers facilitate the maintenance of critically low temperatures, aiding in processes that demand stringent cooling requirements.
Applications of Water Chillers
Over the years, industries have relentlessly sought methods to enhance cooling systems for manufacturing processes. The early 20th century saw the birth of the basic air conditioner, but it was quickly outpaced by the growing demands of large structures and machinery involved in assembly operations. This spurred technological advancements from the 1950s onwards, paving the way for modern cooling equipment capable of supporting intricate processes like laser cutting and die casting, transforming rudimentary water baths into an indispensable component in today’s manufacturing landscape.
Food Processing
In the world of food manufacturing, water chillers are hard at work every day. They play a pivotal role in wineries, where they control the temperature during the fermentation and storage of wine. Similarly, bakeries rely on them for cooling mixers, managing potable water temperature, and cooling yeast tanks, which are vital components in bakery operations.
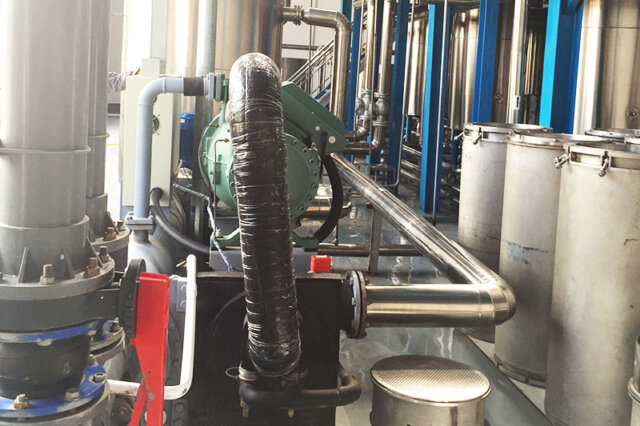
Metal Finishing
Metal finishing processes, such as electroplating, demand precise temperature control to manage the intense heat generated during metal bonding procedures. Water chillers are there to step in, cooling anodizing liquids or utilizing glycol/water mixtures to lower temperatures inside tanks, thereby ensuring a quality finish.
Injection Molding
When it comes to mass-producing plastic parts, injection molding is the way to go. Here, water chillers are integral, providing a continuous flow of supercooled fluid to maintain the mold at the ideal temperature, thus preventing issues like cracks and internal stresses in the final products.
Space Cooling
Manufacturing plants with heavy machinery generate substantial heat. Water chillers are essential in these environments, helping to prevent extreme temperatures in working spaces and offices, thereby saving costs on separate HVAC systems.
Industrial Applications
In industrial settings, machinery and high-powered equipment generate significant heat. Water chillers work tirelessly, circulating cool liquids through equipment to maintain efficiency and enhance the lifespan of these units.
Work Environment
On busy manufacturing floors, temperatures can soar quickly. Water chillers are essential here, helping to keep working conditions at the proper temperature and ensuring employee safety. They work hand in hand with air handling units to cool areas effectively, offering an environment similar to that provided by an air conditioner.
Plastic Manufacturing
In the plastic manufacturing sector, temperature control is crucial to prevent damage to temperature-sensitive materials. Water chillers play a critical role, offering cooling baths that preserve the quality of plastic products, especially during the extrusion process, where they help in maintaining the correct separation of water and cooling mediums.
Power Generation
In power plants, generating electrical power results in a high amount of heat. Chillers are vital, absorbing the generated heat and helping to cool components and processes efficiently.
Medical Industry
Critical medical equipment like MRI and CT scanners generate a considerable amount of heat that needs to be controlled effectively. Water chillers are at the forefront, providing a consistent source of cool temperatures to guarantee the seamless operation of these machines.
Laser Industry
Laser industries rely heavily on chillers to maintain optimal wavelengths in various laser equipment. They ensure peak efficiency by offering a steady source of cool temperatures, vital for precise and accurate laser processes.
How to Choose the Right Chiller Size
Making an informed decision on the right chiller size is paramount in the industry. The process involves considering a few critical parameters to estimate the ideal chiller size suited for your application. Here, we break down the steps to guide you in selecting the appropriate chiller size:
Step 1: Determine Key Parameters
Before you venture into choosing a chiller, it’s essential to gather certain data points, including:
- The flow rate of your process
- The incoming water temperature
- The desired chilled water temperature
Step 2: Utilize the Chiller Tonnage Calculation Formula
Armed with the necessary parameters, employ the following formula to calculate the chiller tonnage you’ll require:
- Calculate the temperature differential: Incoming Water Temperature (°c) – Required Chilled Water Temperature (°c)
- Determine the hourly water flow rate (in m³ or GPM)
- Find the cooling capacity in tons using the formula:Cooling Capacity (tons) = Water Flow Rate x Temp. Differential ÷ 0.86 ÷ 3.517
- To ensure optimal performance, oversize the chiller by 20%, thus:Ideal Size in Tons =
Example:
To bring this into perspective, let’s consider an example where we need to cool 5m³ of water from 25°c to 15°c within an hour. The steps would be as follows:
- Temperature Differential: 25°c – 15°c = 10°c
- Water Flow Rate: 5 m³/hour
- Cooling Capacity: 5×100.86×3.517=16.53 tons
- Ideal Chiller Size: 16.53 tons x 1.2 = 19.84 tons
Therefore, a chiller with a capacity of 19.84 tons would be required to meet your needs.
Efficiency of Chilled Water Chillers
In contemporary industries, optimizing the performance of chilled water chillers is more vital than ever. Recognizing the efficiency of your system and employing strategies to enhance it can lead to a more streamlined operation. Here’s a guide to help you grasp the intricacies of chiller efficiency and how to augment it:
Gauging Efficiency
To truly ascertain the efficiency of a chiller system, it’s essential to consider a few fundamental aspects:
1. Co-efficient of Performance (COP)
A prime indicator of a chiller’s efficiency, this metric compares the amount of cooling provided by the chiller to the amount of energy it consumes. A higher COP indicates better efficiency.
When comparing the COP between air-cooled and water-cooled chillers, there is a marked difference to be noted. Generally, water-cooled chillers exhibit a higher COP, ranging between 3.1 and 4.7, making them significantly more efficient than their air-cooled counterparts, which usually display a COP range between 2.5 and 3.5. This discrepancy arises from the different cooling methods employed by each system; water-cooled chillers utilize a condenser water loop to expel heat to the environment, which is more efficient, while air-cooled chillers rely on fans to discharge the heat, which consumes more energy.
However, it’s crucial to note that the initial investment and maintenance requirements for water-cooled chillers can be higher compared to air-cooled ones. Thus, while considering the COP as a determining factor for chiller efficiency, it’s equally vital to weigh the overall operational costs and the specific requirements of your facility to make an informed decision.
2. Integrated Part Load Value (IPLV)
This variable gives an insight into the chiller’s performance during partial load conditions, offering a more holistic view of its efficiency throughout varying operational states.
3. Seasonal Efficiency
Taking a broader perspective, evaluate the chiller’s efficiency across different seasons to understand how environmental factors might influence its performance.
Tips to Enhance Performance
To boost the efficiency of your chiller system, here are some expert suggestions:
- Regular Maintenance: Like any high-functioning machinery, routine maintenance is key. Ensure the system is clean and free of leaks to maintain optimal efficiency.
- Optimized Water Flow: Adjusting the water flow rate in accordance with the manufacturer’s guidelines can significantly improve the chiller’s efficiency.
- Utilizing Variable Speed Drives: Incorporating variable speed drives can allow the chiller to adapt to different load conditions, enhancing its efficiency considerably.
- Energy Recovery: Explore opportunities to recover and reuse waste heat, thereby promoting a more environmentally friendly and efficient operation.
- System Monitoring: Employ modern monitoring tools to keep a close eye on system performance, enabling timely interventions and adjustments to maintain peak efficiency.
By understanding how to accurately gauge the efficiency and implementing strategies to bolster performance, you can ensure that your chilled water chiller system operates at its peak potential, providing substantial benefits in the long run.
How Long Do Water Chillers Last? (Maintenance of Chiller)
Chillers, both air-cooled and water-cooled types, require a well-maintained pressure balance to operate efficiently.
High-Pressure Troubleshooting in Chillers
Discrepancies in this balance, particularly high pressure, can lead to operational challenges and diminished efficiency. Here’s a brief guide to identifying and addressing common high-pressure problems in both types of chillers:
Air-cooled Chillers
- Inefficient Condenser Function or High Ambient Temperature: Regularly check and clean the fan area to enhance cooling efficiency.
- Condenser Blockage: Maintain a clean condenser to prevent gas buildup; consult the manufacturer for proper cleaning techniques.
- Air Entrapment: After installation or maintenance, vent any trapped air from the system to avoid high-pressure alarms.
- Excess Refrigerant: Avoid overcharging the system with refrigerant and maintain the optimal pressure by venting when necessary.
- Expansion Valve Issues: Monitor the expansion valve regularly and adjust or replace it to maintain the proper pressure balance.
Water-cooled Chillers
- Closed Cooling Water Valve: Ensure the valve is always open for steady water circulation.
- Insufficient Cooling Water Flow or High Water Temperature: Inspect the piping size and ensure that the pump and water valve are working optimally.
- Cooling Water Tower Malfunction: Regularly check the cooling tower for any operational glitches and address them promptly.
- Water Scale Build-up: Arrange for professional cleaning periodically to prevent scale accumulation and ensure efficient operation.
- Refrigerant Overfill: Maintain the correct amount of refrigerant to prevent pressure imbalances and enhance condenser efficiency.
- Expansion Valve Malfunction: Regularly check the valve and adjust or replace as needed to avoid high pressure at the condenser front.
Low-Pressure Troubleshooting in Chillers
Low-pressure troubles in chillers can manifest as a surge in energy usage and diminished cooling efficiency. It’s essential to pinpoint the underlying causes to prevent inefficiencies and potential shutdowns. Here we delve into the common issues and solutions concerning low pressure in chillers:
Potential Issues from Low-pressure Failures:
- Surge in Energy Usage: A chiller experiencing low pressure often consumes more energy due to decreased motor load, resulting in wasted energy under the same cooling conditions.
- Diminished Cooling Efficiency: The chiller struggles to attain its target cooling capacity as reduced suction pressure affects return air volume, which ultimately hampers efficiency and performance.
Causes and Solutions for Low Pressure in Chillers:
- Insufficient Refrigerant or Leakage: This can cause reduced suction pressure, activating a low-pressure alarm, and possibly leading to unit shutdown.
- Solution: Identify and fix any leaks in component junctures and replenish the refrigerant to the correct level.
- Low Ambient Temperature: If the external temperature is low, it might lower the cooling water and compressor oil temperature, potentially triggering a low-pressure fault alarm.
- Solution: Adjust the cooling water temperature or increase the preheating duration to allow the oil temperature to normalize.
- System Pipeline Blockage: Over time, impurities can accumulate in the system, clogging the filter and obstructing refrigerant passage and return air, leading to low pressure.
- Solution: Regular maintenance involving cleaning the filter, condenser, and evaporator should prevent blockages and ensure efficient operation.
- Expansion Valve Issue: A too-small opening or damage to the expansion valve can restrict the refrigerant flow, causing low compressor inlet pressure and a subsequent low-pressure fault.
- Solution: Enlarge the expansion valve opening or replace it if damaged to restore the appropriate chiller function.
- Relay Failure or Electrical System False Alarm: Occasionally, the relay might malfunction, potentially causing incorrect low-pressure alarms and halting the chiller’s operation.
- Solution: Inspect and repair or replace the low-pressure relay as needed. If unsure, consult with the manufacturer for assistance.
Conclusion
In conclusion, understanding and managing the different facets of water chillers, from selecting the right size to ensuring efficient performance and addressing pressure issues, is integral in sustaining their longevity and effectiveness. Implementing routine maintenance and adopting necessary measures can not only enhance the efficiency but also extend the lifespan of your chiller system. Keep these guidelines in mind to make informed decisions and optimize your chiller’s operation.
Furthermore, at SCY Chiller, we are committed to offering you state-of-the-art solutions to all your cooling needs. Our range of products is designed with the latest technology, ensuring energy efficiency and reliable performance. With our user-friendly designs and robust build, you can rely on SCY Chiller to keep your operations running smoothly, minimizing downtimes and maximizing productivity. Choose SCY Chiller for a cooler, more efficient future.
FAQs
Q1: How cold can a water chiller get?
A1: A water chiller can typically cool water to temperatures ranging between 7 to 20°C (45-68°F). The exact minimum temperature can vary depending on the specific make and model of the chiller.
Q2: Do you need a pump for a water chiller?
A2: Yes, a pump is generally required for a water chiller to circulate the chilled water through the system. The pump helps in transferring the water between the chiller and the process equipment that needs cooling.
Q3: How do HVAC water chillers work?
A3: HVAC water chillers work by using a refrigeration cycle to cool or heat water. This chilled or heated water is then circulated through coils in air handling units or other types of terminal devices to condition the space. The basic components of a chiller include a compressor, a condenser, an expansion valve, and an evaporator.
Q4: Are water chillers better than air chillers?
A4: Whether a water chiller is better than an air chiller depends on the specific application and environmental conditions. Water chillers are generally more efficient and quieter, but they require a steady water source and might have higher maintenance requirements. Air chillers, on the other hand, are usually easier to install and maintain.
Q5: How long do water chillers last?
A5: Water chillers can last for around 15-20 years, depending on the frequency of use and maintenance. Regular maintenance, including cleaning and inspecting components, can significantly extend the lifespan of a chiller.
Q6: Do water chillers use a lot of electricity?
A6: The electrical consumption of a water chiller depends on various factors including its size, efficiency, and the load it is handling. Modern chillers are designed to be energy-efficient, but they can be one of the larger consumers of electricity in a facility due to their role in cooling large spaces.
Q7: What is the best liquid for chillers?
A7: The best liquid to use in chillers is usually a mixture of water and a corrosion inhibitor/antifreeze agent. This mixture helps in preventing freezing and corrosion of the chiller components, allowing for efficient heat transfer.
Q8: What is the common problem of chiller?
A8: Some common problems with chillers include refrigerant leaks, reduced efficiency due to scaling, compressor issues, and sensor malfunctions. Regular maintenance can help in identifying and resolving these issues promptly.
Q9: Do water-cooled chillers have refrigerant?
A9: Yes, water-cooled chillers do contain refrigerant. The refrigerant is used in the chiller’s vapor compression or absorption cycle to facilitate the cooling process.
Q10: Where are chillers mostly used?
A10: Chillers are commonly used in various industrial and commercial settings such as manufacturing plants, office buildings, hospitals, schools, and data centers to provide conditioned air and to cool equipment.
Q11: How often do you change the water in a chiller?
A11: The frequency of changing water in a chiller depends on the water quality and system conditions. In general, the water should be checked regularly for impurities, and a complete water change should be done at least once a year or as advised by the manufacturer.