Water chillers, pivotal components in many industrial and commercial cooling systems, can be classified in numerous ways – based on the condenser type, cooling capacity, and the refrigeration cycle. This comprehensive guide provides detailed insights into each category, assisting you in making the optimal choice based on your specific needs.
Classification By Type of Condenser
Condensers play a critical role in the chiller system, effectively removing heat from the system. Two primary types of condensers are prevalent in the industry – air-cooled and water-cooled.
Air-Cooled Chillers
Air-cooled chillers use the ambient air surrounding the system to cool and condense the refrigerant. Ideally suited for small to medium cooling loads, these chillers typically sit outdoors, where fans drive the ambient air over a finned tube or plate heat exchanger, facilitating efficient heat dissipation.
Air-cooled chillers offer simpler and more cost-effective installation, eliminating the need for a separate cooling tower or condenser water pump. Their maintenance demands are relatively low, but they tend to have a higher power consumption and potentially a shorter lifespan than their water-cooled counterparts.
Water-Cooled Chillers
Contrary to air-cooled chillers, water-cooled chillers leverage cooling towers to enhance thermodynamic efficacy. Commonly found in large commercial buildings or industrial facilities, these chillers effectively manage large-scale cooling applications.
In these systems, waste heat generated by the chiller is dissipated into the atmosphere via the cooling tower. This process involves water evaporation at low pressure, facilitating efficient heat absorption.
Water-cooled chillers, while offering superior energy efficiency and quieter operation than air-cooled chillers, necessitate regular maintenance. This includes treating the condenser water to prevent microbial growth and minimize mineral deposit accumulation. However, they can be an excellent choice for applications where heat recovery systems can utilize the discharged heat.
Air-Cooled Chillers | Water-Cooled Chillers | |
---|---|---|
Cost | Lower initial cost, higher operating cost due to lower efficiency | Higher initial cost (due to the need for cooling tower and additional equipment), lower operating cost due to higher efficiency |
Characteristics | – Requires air flow for heat dispersal – Noisy due to the use of fans – Shorter lifespan than water-cooled chillers | – Uses water from a cooling tower for heat dispersal – Quieter operation – Longer lifespan than air-cooled chillers |
Suitable Application | – Small to medium cooling loads – When there’s a lack of water or restrictions on water use – Outdoor, standalone installations | – Medium to large cooling loads – When a water source is readily available – Indoor, industrial, and large-scale commercial applications |
Installation Difficulty | Easier and less expensive to install as they do not require a separate cooling tower or condenser water pump | More complex and costly to install as they require a cooling tower, condenser water pump, and additional piping |
Maintenance | – Generally easier and less costly to maintain – Does not require water treatment or cooling tower maintenance | – More complex and costly to maintain – Requires regular water treatment to prevent microbial growth and mineral deposits – Cooling tower needs regular maintenance and cleaning |
Classification By Cooling Capacity
The cooling capacity of a chiller is a critical parameter determining its applicability. Measured in tons or British Thermal Units (BTUs) per hour, the cooling capacity indicates the volume of heat the chiller can eliminate from a process within a specific timeframe. Chillers generally fall into one of the following categories:
Small Capacity Chillers
Small-capacity chillers, with a cooling capacity ranging from 0.2 tons to 25 tons, are compact and often portable. These chillers are ideal for smaller applications such as laboratory cooling, small-scale manufacturing processes, medical applications, food and beverage industry cooling requirements, and more.
Medium Capacity Chillers
Ranging in cooling capacity from 30 tons to 200 tons, medium-capacity chillers cater to larger commercial applications. These include building HVAC systems, industrial cooling processes, data center cooling applications, and more.
Large Capacity Chillers
Large-capacity chillers, providing a cooling capacity exceeding 210 tons, are usually designed to address large industrial applications and district cooling systems. Given their scale, these chillers are often custom-built based on the specific requirements of the application.
Classification By Refrigeration Cycle
The refrigeration cycle forms the foundation of a chiller’s functionality, dictating how the system removes heat. Depending on the compressor type, chillers can be classified as reciprocating, scroll, screw, or centrifugal.
Reciprocating Chillers
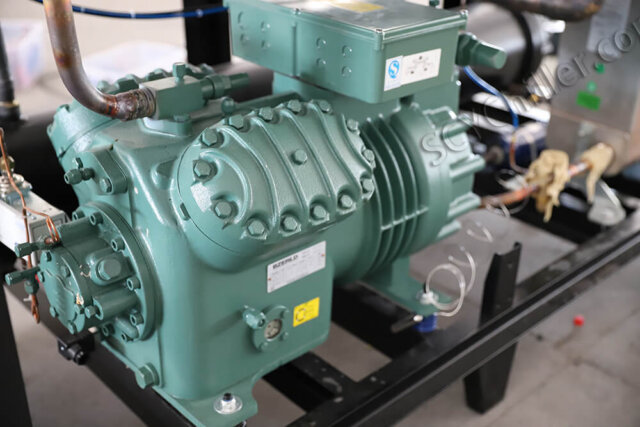
Reciprocating chillers use reciprocating compressors, operating similarly to a car engine. Here, the refrigerant is compressed using the piston’s back-and-forth motion within a cylinder. These chillers are commonly employed for small to medium cooling applications.
Scroll Chillers
Scroll chillers employ scroll compressors that feature two interlocking, spiral-shaped pieces rotating together to compress the refrigerant. With one scroll remaining stationary and the other executing an orbital movement, the refrigerant is forced toward the center, resulting in compression. Scroll chillers offer quiet operation, superior efficiency, and excellent reliability, making them a popular choice for medium-sized cooling needs.
Screw Chillers
Screw chillers incorporate screw compressors, characterized by two intertwined helical rotors enclosed within a casing. As these rotors rotate, the space for the refrigerant decreases, leading to compression. Due to their high efficiency and reliability, screw chillers are often chosen for large-scale commercial and industrial applications.
Centrifugal Chillers
Centrifugal chillers utilize centrifugal compressors that work by spinning a high-speed impeller to compress the refrigerant. These chillers are well-suited for large cooling loads as they can achieve substantial cooling capacities while maintaining high efficiency.
Chiller Type | Advantages | Disadvantages | Cost | Suitable Applications | Maintenance Difficulty |
---|---|---|---|---|---|
Reciprocating Chillers | – Compact and efficient at small scale – Widely available | – Noise and vibration – Requires frequent maintenance | Low to Medium | Small to medium applications, small buildings, process cooling | Moderate |
Scroll Chillers | – High efficiency – Quiet operation – Reliable | – Limited capacity range -Not as efficient at part-load conditions | Medium | Medium-sized cooling needs, mid-sized buildings, process cooling | Low |
Screw Chillers | – High efficiency – Reliable – Suitable for large-scale operations | – Higher initial cost – Requires skilled maintenance | High | Large-scale commercial and industrial applications | High |
Centrifugal Chillers | – High cooling capacity – Highly efficient | – High initial cost – Complex maintenance | High | Large cooling loads, big commercial buildings, district cooling systems | High |
Conclusion
In conclusion, the diverse range of chillers available, each with unique features and advantages, offers myriad options to meet a wide variety of cooling requirements. Whether your need is for a compact, portable chiller for a small application or a custom-built large-capacity chiller for an industrial process, understanding these classifications can guide you to the best choice for your specific needs.
FAQs
- Q: What factors should I consider when choosing a chiller for my application?
A: You should consider factors such as cooling capacity, the type of refrigerant used, energy efficiency, noise levels, space requirements, and maintenance needs. It’s also essential to consider the specific needs of your application. - Q: What is the difference between a water-cooled chiller and an air-cooled chiller?
A: The primary difference lies in the way they dissipate heat. Air-cooled chillers use air to remove heat from the system, while water-cooled chillers use water. Each type has its pros and cons, and the best choice depends on your specific application and environment. - Q: What is the cooling capacity of a chiller?
A: Cooling capacity refers to the amount of heat a chiller can remove from a process in a certain period. It is typically measured in tons or BTUs per hour. The right capacity for you depends on the heat load in your application. - Q: What is the meaning of ‘reciprocating’, ‘scroll’, ‘screw’, and ‘centrifugal’ in the context of chillers?
A: These terms refer to the type of compressor the chiller uses in its refrigeration cycle. Each type operates differently and has its advantages and disadvantages. - Q: How do I maintain a chiller for optimal performance?
A: Regular maintenance activities include cleaning the condenser and evaporator, checking and refilling refrigerant levels, inspecting and tightening electrical connections, and lubricating moving parts. It’s advisable to follow the manufacturer’s guidelines for specific maintenance tasks and intervals. - Q: Can I use my chiller for heat recovery?
A: Yes, certain types of chillers, especially water-cooled ones, are suitable for heat recovery. The waste heat they produce can be used for other processes, such as space heating or preheating water, improving overall energy efficiency.
Good Information for mechanical engineer
thanks