A brine chiller is a cooling system that uses brine (a solution of water and salt) as a refrigerant to transfer heat from a process or application to a cooling source. The brine solution is typically circulated through a heat exchanger to absorb heat from the process or application and then pumped to a cooling source, such as a refrigeration system, where it releases the heat and cools back down to its original temperature.
Why Brine Is Used for Cooling?
Brine is used for cooling because it has a lower freezing point than water, making it suitable for use in low-temperature applications. Additionally, the addition of salt to water lowers the freezing temperature of the solution, and the heat transport efficiency of brine can be greatly enhanced for the comparatively low cost of the material.
A variety of salts can be used to make a brine solution for use in a brine chiller, but sodium chloride (NaCl) is the most commonly used salt. Sodium chloride is readily available, cost-effective, and has a relatively low freezing point, making it an ideal choice for use in refrigeration systems.
Other salts that can be used in a brine chiller include calcium chloride (CaCl2) and potassium chloride (KCl). These salts have lower freezing points than sodium chloride and can be used in applications that require lower temperatures.
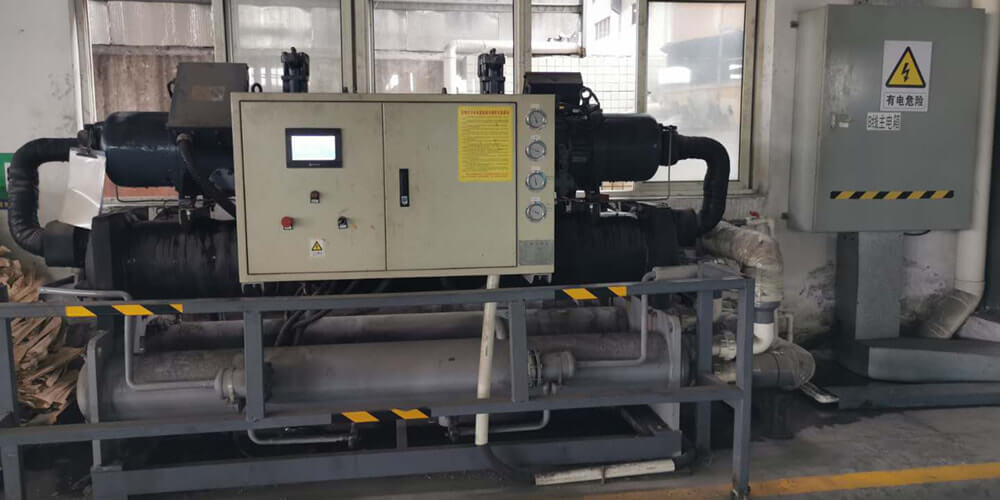
Proper Ratio of Water to Salt for Brine Chiller
Generally, the ratio ranges from 1 part salt to 10 parts water (by weight) for a low-concentration brine, up to 23 parts salt to 77 parts water for a high-concentration brine. The concentration of the brine also affects its freezing point and its heat transport efficiency.
For example, a brine solution with a concentration of 23% NaCl (by weight) has a freezing point of approximately -21°C (-6°F), while a solution with a concentration of 15% NaCl has a freezing point of approximately -10°C (14°F).
It’s important to carefully consider the concentration of the brine when selecting the ratio of water to salt, as higher concentrations of salt can lower the freezing point of the brine and increase its efficiency as a cooling agent, but can also increase the risk of corrosion and other problems. It’s also important to ensure that the salt is fully dissolved in the water before using the brine in the chiller system, as undissolved salt can lead to blockages in the system and other issues that can affect its efficiency and effectiveness.
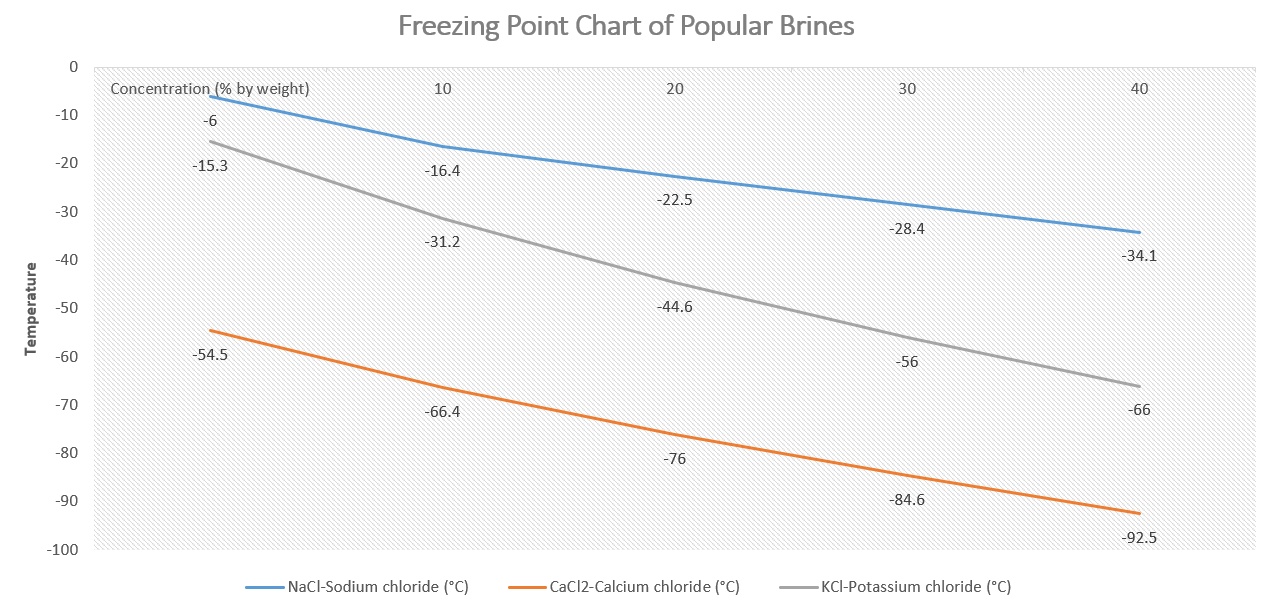
Additionally, it’s important to ensure that the salt is fully dissolved in the water before using the brine in the chiller system. Undissolved salt can lead to blockages in the system and other issues that can affect its efficiency and effectiveness. Regular monitoring and maintenance of the chiller system can also help to ensure that the brine is properly maintained and operating at peak efficiency.
What’s the Difference Between Brine and Glycol?
Brine and glycol are both commonly used as refrigerants in cooling systems, but there are some key differences between the two.
One of the main differences is their composition. Brine is a solution of water and salt, while glycol is a type of alcohol that is chemically similar to ethylene glycol or propylene glycol. This means that brine is a salt-based solution, while glycol is a liquid that does not contain any salt.
Another difference is their toxicity. Glycol can be toxic if ingested or inhaled in large quantities, while brine is non-toxic and safe to handle. This makes brine a safer choice for applications where there is a risk of exposure to the refrigerant.
Property | Ethylene Glycol | NaCl/CaCl2/KCl Brine |
Freeze Point Depression | More effective | Varies with concentration |
Heat Transfer Efficiency/Capacity | Better | Lower than glycols but can be enhanced by increasing the concentration |
Viscosity | Lower | Higher |
Flammability | Low | Non-flammable |
Chemical Oxygen Demand | Low | None |
Biodegrading | Degrades in 10-30 days | Non-biodegradable |
Carcinogenic | No | Non-carcinogenic |
Toxic | High level of acute when taken orally, targets the kidneys | Non-toxic |
Skin Irritant | Low | Low |
Note: The information in this table is based on the general properties and characteristics of these chemicals and may vary depending on the specific concentration and use in a brine chiller system.
The freezing point of brine can be lowered by adding salt to the solution, while the freezing point of glycol can be lowered by adding water. As a result, brine is often preferred for lower-temperature applications, such as in the chemical industry or ice rinks, where temperatures need to be maintained below freezing.
Another difference between brine and glycol is their heat transfer properties. Glycol has a higher heat transfer coefficient than brine, meaning it can transfer heat more efficiently. However, brine is often preferred for applications where precise temperature control is important, as it has a higher specific heat capacity than glycol and can absorb more heat per unit of volume.
When Choose Brine Over Glycol and Vice Versa?
Brine is often chosen over glycol as a refrigerant in several situations:
- Low-temperature applications: Brine has a lower freezing point than glycol and can be used in low-temperature applications where temperatures need to be maintained below freezing, such as in refrigeration systems, ice rinks, and cold storage facilities.
- Non-toxicity: Brine is non-toxic and safe to handle, making it a preferred choice for applications where there is a risk of exposure to the refrigerant.
- Cost: Brine is often less expensive than glycol and can be more cost-effective as a refrigerant for some applications.
- Specific heat capacity: Brine has a higher specific heat capacity than glycol, which means it can absorb more heat per unit of volume. This makes it a more efficient cooling agent than glycol, particularly in applications where precise temperature control is important.
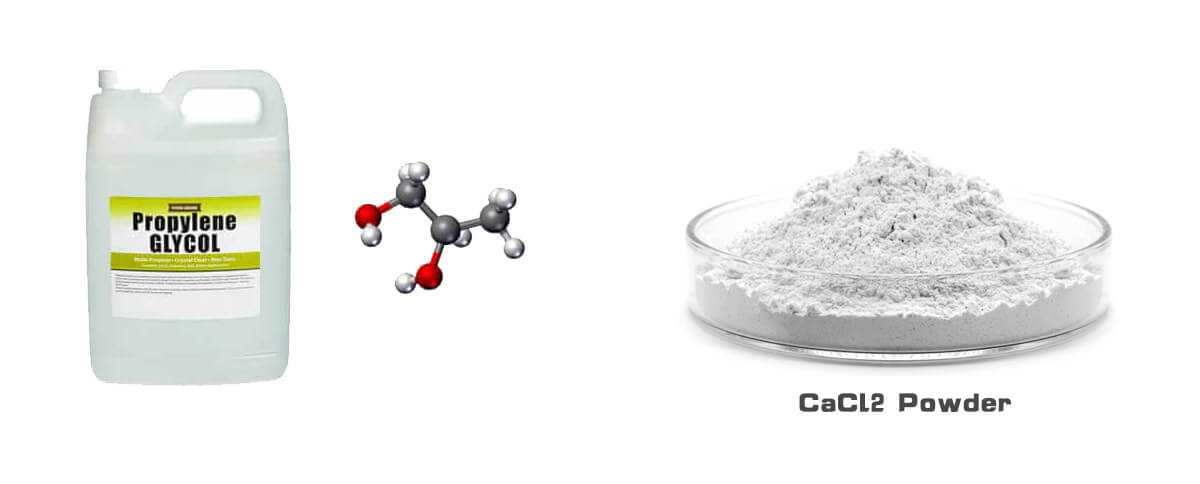
Glycol may be chosen over brine as a refrigerant in several situations:
- Freeze protection: Glycol has a higher freezing point than brine and can be used in applications where freeze protection is necessary, such as in heating and cooling systems that may be exposed to low temperatures.
- Heat transfer efficiency: Glycol has a higher heat transfer coefficient than brine, which means it can transfer heat more efficiently. This makes it a preferred choice for applications where heat transfer efficiency is important, such as in heat exchangers, and air conditioning systems.
- Corrosion resistance: Glycol has a higher resistance to corrosion than brine and can be used in systems that are more prone to corrosion, such as in cooling towers, boilers, and other heating and cooling equipment.
- Availability: Glycol is widely available and can be easily purchased, making it a convenient choice for many applications.
Brine is often preferred over glycol as a refrigerant in super low-temperature applications where precise temperature control is important, due to its lower freezing point, non-toxicity, cost-effectiveness, and higher specific heat capacity. However, glycol may be preferred in applications where freeze protection, heat transfer efficiency, corrosion resistance, and availability are more important factors. Ultimately, the choice between brine and glycol as a refrigerant depends on the specific requirements of the application.
What’s the Biggest Disadvantage of Using Brine in A Chiller?
One of the biggest disadvantages of using brine in a chiller is its potential for corrosion. Salt-based solutions like brine can be highly corrosive to metal surfaces, which can lead to damage and reduced efficiency of the chiller system over time. The corrosive nature of brine can also lead to leaks, contamination, and other problems that can be costly to repair.
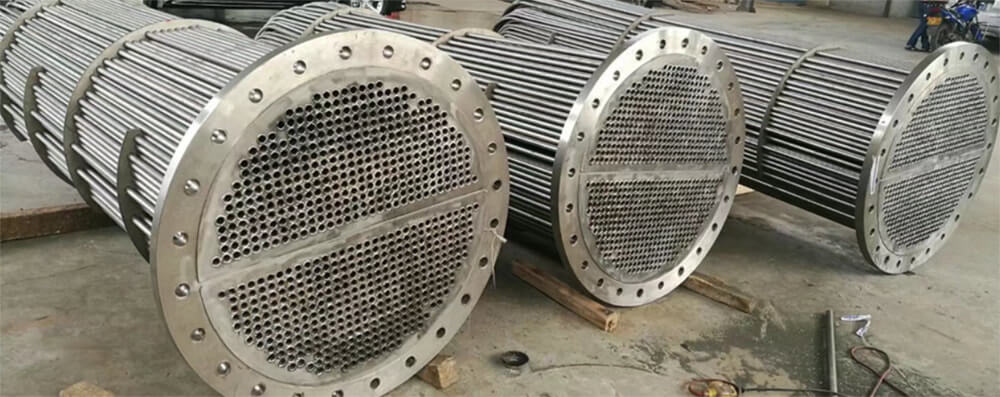
To minimize the risk of corrosion in a brine chiller, it’s important to carefully select the materials used in the construction of the chiller system. Materials that are resistant to corrosion, such as stainless steel or titanium, may be preferred for use in the heat exchanger, piping, and other components of the system. Additionally, regular maintenance and inspection of the chiller system can help to identify and address corrosion issues before they become more serious.
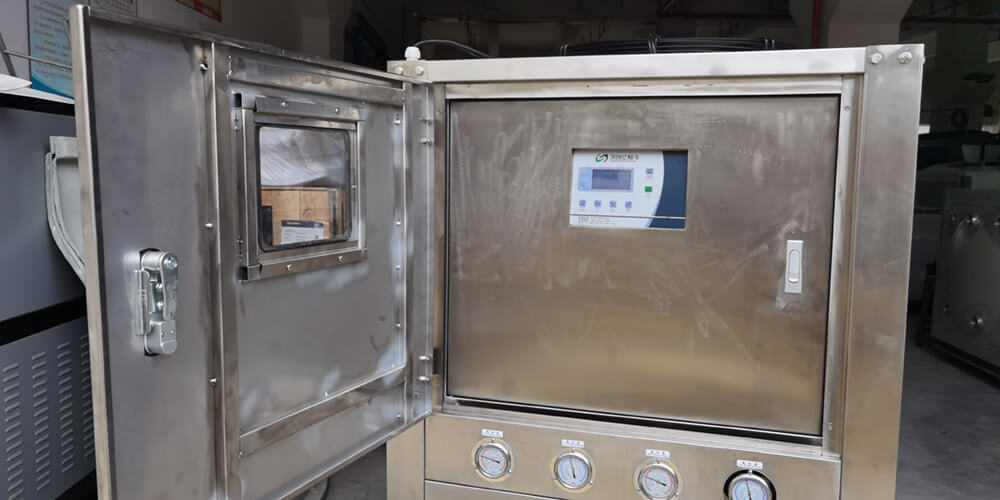
Another potential disadvantage of using brine in a chiller is the risk of contamination. Because brine is typically made from water and salt, there is a risk of bacterial growth and other types of contamination if the brine is not properly maintained and monitored. This can lead to reduced efficiency of the chiller system and may also pose a risk to the safety of the product or process being chilled.
How Does A Brine System Work?
A brine system works in a similar way to a glycol system, but instead of using glycol as the cooling medium, it uses brine. Brine is circulated through the chiller system, absorbing thermal energy from the process and carrying it away to be cooled.
The brine chiller consists of a compressor, an evaporator, a condenser, a throttling element, and an electric control system, similar to the glycol chiller. The refrigerant in the chiller absorbs heat from the brine, causing it to turn into a gas. The gaseous refrigerant is then circulated to a condenser where the heat is expelled through evaporative condensation, causing the refrigerant to condense back into a liquid.
As the brine circulates through the chiller system, it absorbs heat from the process and carries it away to be cooled. The cooled brine is then recirculated back to the process to begin the cycle again.
The specific details of how a brine system works will depend on the specific requirements of the application and the design of the chiller system. However, in general, a brine chiller works by using brine as the cooling medium to remove heat from the process and maintain a consistent temperature. The use of brine as a refrigerant can be cost-effective and efficient, particularly in low-temperature applications where precise temperature control is important.
What Can A Brine Chiller Be Used For?
A brine chiller can be used in various industries where precise temperature control is essential for product quality and safety. Some of the industries that are suitable for a brine chiller include:
Food and beverage industry
Brine chillers are commonly used in the food and beverage industry to cool process equipment such as reactors, condensers, and heat exchangers. They are also used for cooling food products during processing and storage.
Chemical processing industry
Brine chillers are used in the chemical processing industry to cool reactors, condensers, and other equipment that require precise temperature control.
Pharmaceutical industry
Brine chillers are used in the pharmaceutical industry to cool equipment used in the production of drugs and other medical products.
Ice rinks
Brine chillers are used to cool the ice surface in ice rinks and maintain a consistent temperature for the ice.
Refrigerated warehouses
Brine chillers are used in refrigerated warehouses to maintain a consistent temperature for the storage of perishable goods.
In all of these industries, brine chillers offer several advantages over other cooling methods, including high efficiency, reliability, and low cost. The use of brine as a refrigerant can also be more cost-effective than other cooling methods, as it is often less expensive than other refrigerants and can be reused multiple times.
How To Choose The Right Capacity for A Brine Chiller?
From the above information, we will know the important role played by brine chillers not only in industry but also in commercial applications. There are some useful tips for sizing your brine chillers:
Air-cooled Or Water-cooled
Air-cooled chillers use a condenser that is similar to the “radiators” in a car. They use a fan to force air through the refrigerant coil. Unless they are specifically designed for high ambient conditions, air-cooled condensers need to operate effectively at an ambient temperature of 35°C (95°F) or less.
Air-cooled chillers require less maintenance than water-cooled chiller units.
Advantages of air-cooled chiller:
- Air-cooled chillers do not require cooling towers.
- Easier to install compared with a water-cooled chiller.
Water-cooled chillers function in the same way as air-cooled chillers but require two steps to complete the transfer of heat. First, heat enters the condenser water from the refrigerant vapor. The warm condenser water is then pumped to the cooling tower, where the heat from the process is eventually vented to the atmosphere.
Advantages of water-cooled chiller:
- Higher COP(Coefficient Of Performance).
- Lower cost on power for the same cooling capacity.
- Have a longer lifespan.
- Relatively quieter than air-cooled chillers.
- Provide more consistent cooling performance.
Cooling capacity
How to calculate the cooling capacity I need? Let’s see the below formula.
- Calculate Temperature Differential = Incoming Water Temperature (°c) – Outlet Chilled Water Temperature(°c)
- Water flow rate that you need per hour(m³/hour)
- Get in tons of cooling capacity = Water Flow Rate x Temperature Differential ÷ 0.86 ÷ 3.517
- Oversize the chiller by 20% Ideal Size in Tons = Tons x 1.2
- You have the ideal size for your needs.
Fill out our quick sizing form and we will be able to provide you with the glycol chiller selection customized to your process.
If you are not sure how to choose the cooling capacity, please contact us.
Whether A Built-in Tank Is Necessary
In a chiller system, a tank is usually equipped to buffer the thermal load of the chiller. But should we choose a built-in type of tank or an external type of tank? A chiller with a built-in tank is easier to install and can be used simply by connecting a water pipe to your application. But it has a limited capacity and is not suitable for applications with larger chilled water demands. The external tank’s capacity can be customized according to specific needs. It can buffer a larger heat load, and store more chilled water, but the installation will be more troublesome.
Water Flow
The water flow of a glycol chiller is mainly controlled by the pump, so you can choose a pump with different flow rates according to your specific needs.