Anodizing&Plating Processes are two widely used surface treatment methods in industrial production, aimed at improving the performance, durability, and aesthetic appeal of metal and plastic components. Anodizing is an electrochemical process that creates a thick, protective oxide layer on the surface of a metal substrate, through the controlled oxidation of the material. This oxide layer not only enhances the metal’s resistance to corrosion, wear and tear, and temperature but can also serve as a base for coloring or printing.
On the other hand, Plating is a process that involves depositing a thin layer of metal on the surface of a substrate using either electroplating or electroless plating methods. Plating is usually used to improve surface hardness, resistance to abrasion, and electrical conductivity of a substrate, but can also be used for decorative purposes. Both Anodizing and Plating Processes require strict control of various parameters to ensure high-quality, consistent results, making them an important part of various industries, including automotive, aerospace, electronics, and construction.
While both processes are aimed at enhancing the surface properties of a substrate, they differ in their mechanisms and applications. In the following sections, we will describe the principles, processes, and applications of Plating Process and Anodizing Process, including the different types of plating and anodizing, their respective advantages and disadvantages, and the challenges and innovations in each process. We will also discuss the importance of cooling water and the role of chillers in ensuring the quality and efficiency of Plating and Anodizing Processes.
Anodizing Process
Anodizing Process creates a thick, protective oxide layer on the surface of a metal substrate. The process involves immersing the metal substrate into an electrolyte solution, which is typically an acid, and passing an electrical current through it. As a result, oxygen ions in the electrolyte solution are attracted to the surface of the metal substrate and combine with the metal atoms to form a stable, dense layer of aluminum oxide. This oxide layer provides an excellent barrier against corrosion, wear and tear, and environmental factors. Anodizing Process can be performed in different types, including sulfuric acid anodizing, chromic acid anodizing, and hard anodizing, depending on the desired properties of the oxide layer. Anodizing Process is a safe and eco-friendly process that does not alter the composition of the metal, making it suitable for a wide range of applications, including aerospace, automotive, and construction industries.
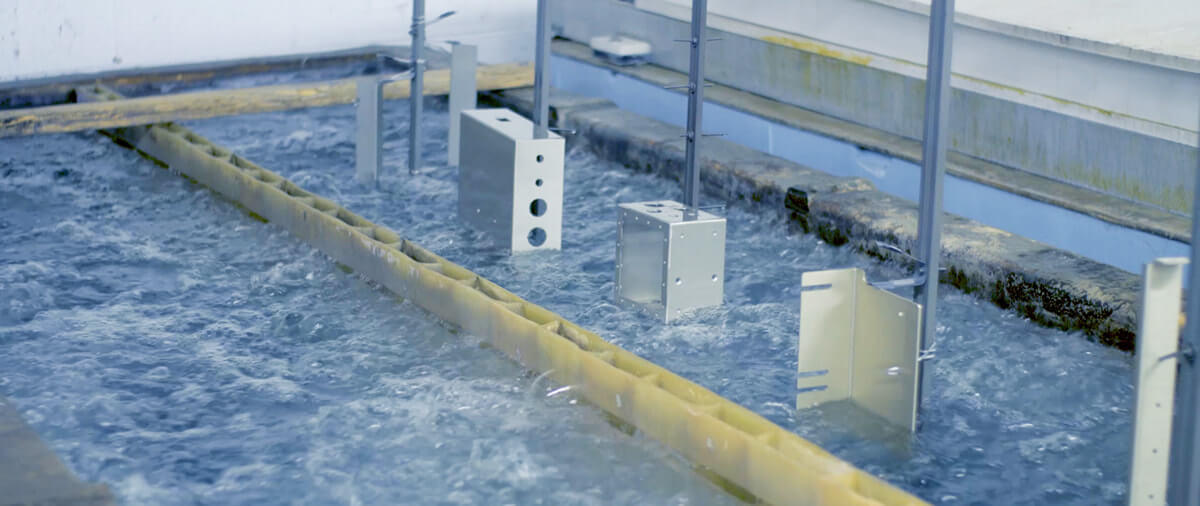
Anodizing Process Types
Anodizing Process is a versatile surface treatment method that can be classified into different types based on the electrolyte solution used and the desired properties of the oxide layer.
- Sulfuric acid anodizing is the most common type of Anodizing Process and results in a dense and hard oxide layer that is highly resistant to corrosion, wear, and environmental factors. This type of anodizing can be further dyed or painted to achieve different colors and aesthetic effects.
- Chromic acid anodizing, on the other hand, results in a thinner and more flexible oxide layer that has good adhesion to the substrate and is ideal for aerospace and electrical applications.
- Hard anodizing is a type of sulfuric acid anodizing that involves higher voltages and temperatures, resulting in a thick and wear-resistant oxide layer that is suitable for high-stress applications such as piston rods and hydraulic cylinders.
Anodizing Process has a wide range of applications in various industries, including aerospace, automotive, electronics, and construction. Anodized parts are commonly used in aircraft structures, automobile bodies, electronic housings, and architectural finishes. The benefits of Anodizing Process include enhanced corrosion resistance, wear resistance, and aesthetic appeal, making it a popular and cost-effective surface treatment method for various substrates.
Pros and Cons of Anodizing Process
Anodizing Process is a widely used surface treatment method that provides several benefits but also has some limitations.
The advantages of Anodizing Process include the creation of a hard, durable, and corrosion-resistant surface layer that enhances the functional and aesthetic properties of a substrate. Anodizing is also a safe and eco-friendly process that does not alter the composition of the metal. Additionally, Anodizing Process can be performed in different types, providing flexibility in achieving various colors, finishes, and properties.
However, there are also some limitations to Anodizing Process. For example, the thickness of the oxide layer is limited and can affect the mechanical properties of the substrate. Anodizing Process also requires strict control of various process parameters, which can increase the cost and time required for production. Moreover, some types of anodizing, such as chromic acid anodizing, can be hazardous to health and the environment. Despite these limitations, Anodizing Process remains a popular and cost-effective surface treatment method for various applications.
Pros | Cons |
Hard, durable, and corrosion-resistant surface layer | Limited thickness of the oxide layer can affect mechanical properties |
Safe and eco-friendly process | Requires strict control of various process parameters, increasing cost and time |
Provides flexibility in achieving various colors, finishes, and properties | Some types of anodizing can be hazardous to health and the environment |
Anodizing Quality Inspection Methods
To ensure high-quality and consistent results in Anodizing Process, various quality inspection and control methods are used. One of the most common methods is to measure the thickness and porosity of the oxide layer using non-destructive testing techniques such as eddy current testing, X-ray fluorescence, or magnetic induction. The surface appearance, color, and gloss of the anodized parts can be inspected visually or using colorimeters and gloss meters. Other quality control methods include testing the corrosion resistance, wear resistance, and adhesion strength of the anodized layer using salt spray testing, scratch testing, and peel testing. To maintain the quality and consistency of Anodizing Process, it is crucial to control various process parameters, including the concentration and pH value of the electrolyte solution, the temperature and current density, and the agitation rate. Real-time monitoring and feedback systems can help identify and correct process deviations, ensuring that the final products meet the desired specifications and performance requirements.
Method | Purpose |
Non-destructive testing techniques | Measure the thickness and porosity of the oxide layer using eddy current, XRF, or MI |
Visual inspection and instruments | Inspect the surface appearance, color, and gloss using visual inspection or instruments |
Corrosion resistance testing | Test the corrosion resistance of the anodized layer using salt spray testing |
Wear resistance testing | Test the wear resistance of the anodized layer using scratch testing |
Adhesion strength testing | Test the adhesion strength of the anodized layer using peel testing |
Process control parameters | Control process parameters such as electrolyte solution concentration, temperature, etc. |
Real-time monitoring systems | Identify and correct process deviations in real-time to ensure consistent results |
Plating Process
Plating Process is a surface treatment method that involves depositing a thin layer of metal on a substrate surface using an electroplating or electroless plating process. Electroplating is a process that involves passing an electrical current through an electrolyte solution containing metal ions, which are then attracted to the substrate and deposited on its surface. Electroless plating, on the other hand, involves a chemical reduction reaction that deposits metal ions onto the substrate surface without the need for an external electrical current. Plating Process can be performed on a variety of substrates, including metals, plastics, and ceramics, to improve their surface properties, such as wear resistance, corrosion resistance, and electrical conductivity. The thickness, adhesion, and properties of the plated layer can be controlled by adjusting various process parameters, such as the composition and pH value of the plating solution, the temperature and agitation rate, and the current density. In the following sections, we will discuss the different types of Plating Processes, their advantages and disadvantages, and their applications in various industries. We will also discuss the importance of cooling water and the role of chillers in Plating Process.
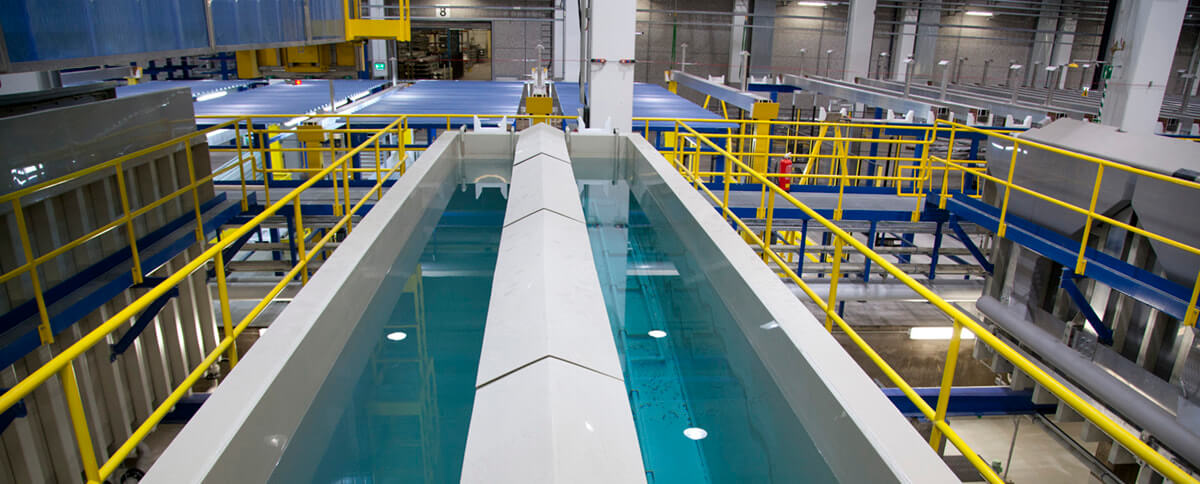
Plating Process Types
Plating Process can be classified into various types based on the type of metal used in the plating solution, the substrate material, and the properties of the plated layer. Some of the most common types of Plating Process include electroless nickel plating, gold plating, silver plating, and copper plating.
- Electroless nickel plating is a widely used type of Plating Process that provides excellent wear resistance, corrosion resistance, and hardness properties.
- Gold plating is known for its excellent conductivity, corrosion resistance, and aesthetic appeal, making it suitable for electronic and jewelry applications.
- Silver plating is another popular type of Plating Process that provides excellent conductivity and is commonly used in electrical contacts and connectors.
- Copper plating is often used as an underlayer for other types of plating to enhance the adhesion and corrosion resistance properties of the plated layer.
Plating Process has a wide range of applications in various industries, including aerospace, automotive, electronics, and medical. It can be used to enhance the performance, appearance, and durability of a substrate and is often used in the manufacturing of parts, components, and finished products. The benefits of Plating Process include improved properties, lower cost, and environmental friendliness, making it a popular and cost-effective surface treatment method for various applications.
Pros and Cons of Plating Process
The advantages of Plating Process include the ability to deposit a thin layer of metal on a substrate surface, which enhances the surface properties of the substrate, such as wear resistance, corrosion resistance, and electrical conductivity. Plating Process can also be performed on a variety of substrates, making it a versatile surface treatment method. Additionally, Plating Process can be performed in different types, providing flexibility in achieving various properties and finishes.
The limitations of Plating Process. For example, the process requires strict control of various process parameters, which can increase the cost and time required for production. Moreover, some types of Plating processes, such as electroplating, require a substantial amount of electricity and generate wastewater, which can be hazardous to the environment. Despite these limitations, Plating Process remains a popular and cost-effective surface treatment method for various applications.
Pros | Cons |
Deposition of a thin layer of metal onto a substrate surface | Requires strict control of various parameters, increasing production cost and time |
Enhances surface properties of substrate | Certain types of Plating Process generate wastewater and consume a significant amount of electricity, which can be harmful to the environment |
Versatile and can be performed on a variety of substrates | |
Different types available, allowing for various properties and finishes |
Plating Quality Inspection Methods
Quality inspection and control are crucial in Plating Process to ensure high-quality and consistent results. Some of the most common quality control methods include measuring the thickness and adhesion strength of the plated layer, visually inspecting the surface for defects, and testing the corrosion resistance, wear resistance, and electrical conductivity of the plated layer. These tests are typically performed using non-destructive techniques such as X-ray fluorescence and magnetic induction. In addition to testing, controlling various process parameters such as the composition and pH value of the plating solution, the temperature and agitation rate, and the current density is important for maintaining the quality and consistency of the plated layer. Real-time monitoring and feedback systems can help identify and correct process deviations, ensuring that the final products meet the desired specifications and performance requirements. By implementing a rigorous quality control system, Plating Process can produce high-quality, reliable, and cost-effective products for various applications.
Method | Purpose |
Non-destructive testing techniques | Measure the thickness and adhesion strength of the plated layer using XRF or magnetic induction |
Visual inspection | Inspect the surface for defects visually |
Corrosion resistance testing | Test the corrosion resistance of the plated layer using salt spray testing |
Wear resistance testing | Test the wear resistance of the plated layer using scratch testing |
Electrical conductivity testing | Test the electrical conductivity of the plated layer using resistance testing |
Process control parameters | Control process parameters such as plating solution composition, temperature, etc. |
Real-time monitoring systems | Identify and correct process deviations in real-time to ensure consistent results |
Cooling Water Requirements in Anodizing&Plating Process
Temperature control is a critical factor in both Anodizing and Plating Processes. The plating solution or electrolyte solution used in both processes has a temperature range that must be maintained within a specific tolerance. The temperature of the plating solution or electrolyte solution affects the plating rate, thickness, quality, and properties of the plated layer. For example, if the temperature is too high, the plated layer may become porous, brittle, or have poor adhesion strength. On the other hand, if the temperature is too low, the plating rate may be too slow, which can lead to uneven deposition or inconsistent properties. To maintain the proper temperature range, temperature control systems, such as chillers or heaters, are commonly used to regulate the temperature of the plating or electrolyte solution. The cooling water temperature used in the temperature control system is also important and must be carefully controlled to ensure that the plating or electrolyte solution temperature stays within the desired range. In the next sections, we will discuss the cooling water requirements and the role of chillers in Anodizing and Plating Processes.
Application of Chiller in Anodizing&Plating Process
Chillers play a critical role in maintaining the proper temperature range in Anodizing&Plating Process. Chillers are commonly used to cool the plating or electrolyte solution to maintain the proper temperature range for consistent plating results. Chillers remove the excess heat generated by the Anodizing&Plating Process and maintain the temperature within the desired range. The cooling capacity of the chiller must be matched to the specific requirements of the Anodizing&Plating Process to ensure proper temperature control. Different types of chillers, such as air-cooled or water-cooled chillers, may be used depending on the application and process requirements. The chiller can also provide additional benefits, such as increased energy efficiency, reduced water usage, and improved equipment lifespan. In addition to providing temperature control, chillers can also offer other features such as flow rate monitoring and automatic temperature control to help maintain optimal process conditions. The proper application of chillers can help to ensure consistent and high-quality results in Anodizing&Plating Process.
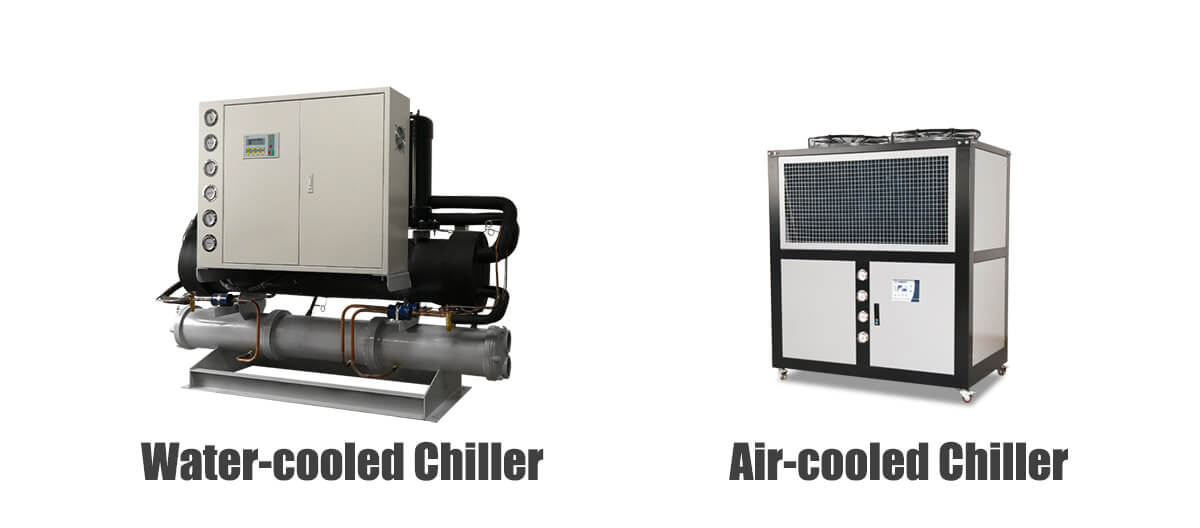
Key Points for Selection and Configuration of Chiller
- Cooling capacity: The cooling capacity of the chiller should be matched to the specific requirements of the Anodizing&Plating Process to ensure proper temperature control. The cooling capacity of the chiller is typically measured in tons or kilowatts and should be selected based on the heat load of the process. If you have data like the temperature difference of in&out water, and the flow rate of the solution, please refer to our chiller size calculator.
- Type of chiller: The type of chiller, such as air-cooled or water-cooled, should be selected based on the specific application and process requirements. Water-cooled chillers are typically more efficient and can provide higher cooling capacities, but require access to a cooling tower and consume more water. Air-cooled chillers, on the other hand, are easier to install and maintain, but have lower cooling capacities and require more space to vent the waste heat.
- Temperature control range: The chiller should be able to maintain the temperature of the plating or electrolyte solution within a specific range. The range is typically determined by the specific requirements of the Anodizing&Plating Process, and the chiller should be selected based on its ability to maintain the required temperature range.
- Flow rate and pressure: The flow rate and pressure of the cooling water should be compatible with the chiller’s requirements. The flow rate and pressure can affect the chiller’s performance and efficiency, so it is important to ensure that the cooling water system is properly designed and configured.
- Energy efficiency: The energy efficiency of the chiller should be considered to minimize operating costs and reduce environmental impact. Energy-efficient chillers can help to lower energy costs and reduce greenhouse gas emissions.
- Maintenance and service: The chiller should be easy to maintain and service to minimize downtime and ensure reliable operation. Regular maintenance, such as cleaning the heat exchanger and replacing filters, can help to maintain the chiller’s performance and prolong its lifespan.
By considering these key points, it is possible to select and configure a chiller that meets the specific requirements of Anodizing&Plating Process and provides reliable, efficient, and cost-effective temperature control.
Troubleshooting of Chiller
Proper maintenance and operation of a chiller are crucial for reliable and consistent temperature control in Anodizing&Plating Process. However, if a problem does occur, it is important to be able to troubleshoot the issue and identify the root cause of the problem. Common issues with chillers can include low refrigerant levels, clogged filters, or failed components such as compressors or heat exchangers. In some cases, the problem may be related to the cooling water system rather than the chiller itself, such as issues with water flow or pressure. Troubleshooting can involve various methods such as visual inspection, measuring temperatures and pressures, or using diagnostic tools such as vibration analysis. By identifying and addressing the root cause of the problem, it is possible to minimize downtime and ensure that the Anodizing&Plating Process can continue to operate at optimal performance levels. Regular maintenance and monitoring can also help to prevent issues from occurring and ensure that the chiller and cooling water system are operating reliably and efficiently. For more detailed troubleshooting information, please refer to Refrigeration System Top 10 Failures Check List.
Innovative Technologies in Anodizing&Plating Process
Advancements in technology have led to the development of new and innovative approaches for Anodizing&Plating Processes. These technologies can offer benefits such as improved efficiency, reduced environmental impact, and enhanced performance.
For example, pulse plating is a technique that uses intermittent current to deposit metal ions onto a substrate, resulting in improved adhesion and uniformity.
Another example is the use of electroless plating, which involves the deposition of a metal layer onto a substrate without the need for an external power source. This technique can result in improved properties such as corrosion resistance and hardness.
In addition, various nanotechnology-based approaches, such as the use of nanostructured coatings or surface modifications, are being explored for Anodizing&Plating Process to enhance the performance and durability of plated surfaces. These innovative technologies have the potential to revolutionize the Anodizing&Plating Process industry and offer new possibilities for advanced surface treatments.
Conclusion
Anodizing&Plating Process plays a crucial role in many industrial applications by providing enhanced surface properties, such as corrosion resistance, wear resistance, and improved aesthetics. The processes are widely used in various industries such as automotive, aerospace, electronics, and medical devices. The high demand for these processes has led to the development of new technologies and approaches for improving efficiency, performance, and sustainability. The use of chillers and temperature control systems is critical for maintaining the proper temperature range and ensuring consistent and reliable plating results. Advanced technologies such as pulse plating, electroless plating, and nanotechnology-based approaches offer exciting possibilities for the future of Anodizing&Plating Process. As industrial applications continue to grow and evolve, the demand for Anodizing&Plating Process is expected to increase, driving further advancements in technology and new approaches to surface treatments.
Status and Role of Chiller in Anodizing&Plating Process
Chillers play a critical role in the Anodizing&Plating Process industry by providing reliable and efficient temperature control for plating solutions and electrolyte solutions. The use of chillers is widespread and essential for ensuring consistent plating results and maintaining high product quality. In addition, chillers offer benefits such as improved energy efficiency, reduced water usage, and longer equipment lifespan. As new plating and surface treatment technologies continue to emerge, the role of chillers is expected to become even more important in ensuring optimal process conditions and performance. As a result, the Anodizing&Plating Process industry is likely to continue to rely on chillers and other temperature control systems for the foreseeable future.
Professional Anodizing&Plating Process Chiller Supplier
If you’re in need of a reliable and efficient chiller for your Anodizing&Plating Process, look no further than SCY Chiller. Our chillers are designed to provide precise temperature control for a wide range of industrial applications, including plating and surface treatment processes. We offer a variety of chiller types, such as air-cooled and water-cooled chillers, to meet your specific needs and requirements. Our chillers are energy-efficient, easy to operate, and require minimal maintenance, ensuring that your Anodizing&Plating Process runs smoothly and efficiently. Contact us today to learn more about our chiller solutions and how we can help optimize your Anodizing&Plating Process.