Adiabatic cooling represents a mechanism that capitalizes on the principles of thermodynamics, particularly the interplay between pressure and temperature. This process instigates a decrease in the system’s pressure, thus inciting volume expansion. This expansion translates into work exerted on the proximate environment, consequently engendering cooling.
What is An Adiabatic Cooling System
Adiabatic cooling systems function in a remarkably efficient and smart way. Initially, these systems pull air from the surrounding environment and decrease its temperature using the process of water evaporation, creating a refreshing cool breeze.
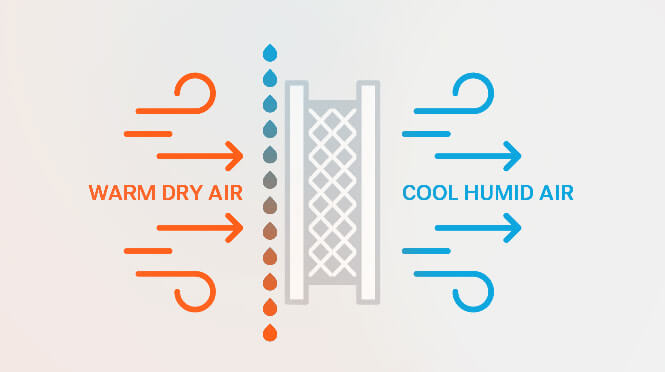
Next, this cooled air is directed towards a heat exchanger, where it takes on a crucial role. Acting like a sentinel, the exchanger extracts unwanted heat energy from the associated equipment or process and transfers it to the awaiting cool air.
Having accomplished its duty, the circulating air is now warmer. However, it doesn’t remain in this state for long. The system employs evaporation once again, cooling the air and readying it for another cooling cycle. Thus, the process continues in a ceaseless, efficient loop, showcasing the marvel of adiabatic cooling.
The process of adiabatic cooling is leveraged in various sectors. These systems take advantage of naturally occurring phenomena to control temperatures, which can significantly save water consumption—an essential consideration in cooling towers and similar installations.
Types of Adiabatic Cooling Systems
Two primary categories delineate adiabatic cooling systems:
- Direct Adiabatic Cooling: Commonly referred to as evaporative cooling, this type employs a direct interaction between water and air within the system. The cooling process is initiated by evaporating water into the air stream. As the air assimilates the heat energy during water evaporation, its temperature reduces. This cooled and humidified air is then recirculated, effectively lowering the temperature of the designated system or space.
- Indirect Adiabatic Cooling: Unlike the direct method, this system executes the cooling process within a heat exchanger. The warm air derived from the system assists in water evaporation. However, instead of recirculation, this cooled air is discharged externally. Concurrently, the heat exchanger exploits the ensuing cooling effect to attenuate the temperature of a secondary air stream that is circulated within the system or space. Consequently, the system or space’s humidity remains unaffected, a contrast to the direct adiabatic cooling method.
Each cooling system carries distinct advantages and disadvantages. Selection hinges on an array of considerations, including specific cooling needs, local climate conditions, and other influential factors. These variants of adiabatic cooling demonstrate the diversity and adaptability of this eco-friendly, efficient cooling methodology.
Direct Adiabatic Cooling | Indirect Adiabatic Cooling | |
---|---|---|
Pros | 1. More energy-efficient as it cools air directly using evaporation. 2. Simple and cost-effective to install and maintain. 3. Ideal for dry and hot climates where the added humidity can be beneficial. | 1. Maintains control over humidity, avoiding increased moisture levels within the system or space. 2. Provides more consistent cooling as the process isn’t heavily influenced by external humidity. 3. Suitable for humid climates or sensitive environments where added humidity could be detrimental. |
Cons | 1. Increases humidity levels, which can be a disadvantage in already humid climates or in environments sensitive to moisture. 2. Cooling effectiveness can decrease with higher external humidity. | 1. Requires more energy and is generally less efficient due to the two-stage cooling process. 2. Complex design can result in higher installation and maintenance costs. 3. In extremely dry climates, it may not cool as effectively as direct systems. |
Where Do Adiabatic Cooling Systems Excel?
Adiabatic cooling systems emerge as a competent and cost-effective alternative, notably in torrid, dry environments where water is scarce and bears significant expense. These systems also excel in regions where ambient air temperatures stay comfortably cool for the majority of the year, enabling air-cooled fluid coolers or refrigerant condensers to operate with optimal efficiency.
Greenhouse Temperature Regulation
Adiabatic cooling systems serve as an efficient solution to maintain optimal temperatures in greenhouses. By managing the evaporation and condensation processes, they help maintain the right temperature and humidity needed for plant growth, especially in hot climates.
Industrial Processes
Sectors such as manufacturing, chemical processing, and power generation frequently generate substantial heat and require steady, efficient cooling. Adiabatic systems proffer an energy-saving and eco-friendly solution.
Hot and Dry Climates
Direct adiabatic cooling systems prove particularly efficacious in dry, hot conditions. The evaporative process not only cools the air but also imparts much-needed humidity to the surroundings.
Buildings and Offices
For structures where conventional air conditioning would be excessively costly or energy-demanding, adiabatic cooling systems present an efficient and environmentally conscious alternative.
Humid Environments
Indirect adiabatic cooling systems perform admirably in humid conditions where an increase in moisture levels is not desirable. They cool the air without intensifying the humidity, ensuring comfort without excess dampness.
In choosing whether an adiabatic cooling system is a suitable fit, the specific needs and conditions of your project or space should be duly considered.
The Necessity of Water Treatment in Adiabatic Cooling Systems
In the realm of adiabatic cooling towers, one might find two distinct water systems: one dedicated to the humidification and cooling of the inlet airstream and another functioning as a closed recirculation loop.
The absence of the recirculating cooling tower from the cooling matrix greatly streamlines the water treatment process. For the closed loop component of an adiabatic system, it is advised to administer corrosion inhibitors befitting of the water quality and system metallurgy. Take note that in colder climates, the inclusion of glycol may be crucial for freeze protection.
To facilitate rapid and complete evaporation of the water in the airstream, adiabatic cooling systems typically employ wetted humidification pads or misting spray nozzles, thus creating a high surface area. If the makeup water that is supplied to the cooling pads or spray nozzles possesses significant hardness, it may be necessary to implement softening measures to prevent the accumulation of mineral deposits that could impair cooling efficiency. Cooling media pads should be preserved and replaced in accordance with the manufacturer’s guidelines. In cases where misting spray nozzles are utilized, deionized water may be prescribed if the adiabatic cooling will be deployed beyond a certain annual hour limit.
Adiabatic models incorporating a sump or basin for the recirculation of spray water may also necessitate bleed control apparatus, a scale/corrosion inhibitor, and the addition of biocides. Despite adiabatic cooling system designs potentially being less susceptible to Legionella proliferation and transmission compared to standard cooling tower systems, the spray water system could still generate aerosols, thereby posing a potential Legionella risk. All water treatment chemicals should be in line with manufacturer stipulations and regulatory mandates.
In a myriad of locations and applications, adiabatic cooling systems prove to be a competent solution. Despite the requirement for routine preventative maintenance on the cooling pads or spray system, the overall water treatment demands are significantly diminished.
FAQs
Q1: What are the different types of adiabatic cooling systems?
Adiabatic cooling systems mainly fall into three categories: Direct, Indirect, and Two-Stage adiabatic cooling. Direct adiabatic cooling involves the evaporation of water directly into the air, cooling it down. Indirect adiabatic cooling uses a heat exchanger to cool a secondary air stream, keeping the internal humidity unchanged. The Two-Stage adiabatic cooling system combines both methods, providing a more efficient and rapid cooling solution.
Q2: In what situations are adiabatic cooling systems most effective?
Adiabatic cooling systems are particularly beneficial in hot, dry climates where water resources are scarce, and also in environments where the outside air temperature is sufficiently cool for most of the year. They are also ideal for data centers, industrial processes, buildings, and offices. Moreover, they serve well in humid environments, and they can help regulate temperature in greenhouses.
Q3: What are the advantages and disadvantages of direct and indirect adiabatic cooling systems?
Direct adiabatic cooling systems are beneficial because they’re relatively simple and cost-effective, especially in dry climates. However, they can increase humidity levels, which may not be desirable in certain conditions. Indirect adiabatic cooling systems, on the other hand, avoid increasing humidity but may be more complex and costly. Also, their cooling capacity may be slightly lower than direct systems.
Q4: How do adiabatic cooling systems contribute to water and energy conservation?
Adiabatic cooling systems utilize the natural process of evaporation to cool air, which is inherently energy-efficient. Additionally, indirect and two-stage systems can control humidity without adding moisture to the air, making them ideal for dry environments. Moreover, their water treatment requirements are less complex and demanding, contributing to water conservation.
Q5: What are the water treatment requirements for adiabatic cooling systems?
In adiabatic cooling systems, it is crucial to treat the closed loop with appropriate corrosion inhibitors and possibly glycol for freeze protection. If the system uses humidification pads or misting spray nozzles, water softening might be required to prevent mineral deposit build-up. When a sump or basin is used to recirculate spray water, additional measures like bleed control equipment, scale/corrosion inhibitors, and biocides may be needed. Ensuring all treatment chemicals comply with manufacturer and regulatory guidelines is essential.