Chillers are vital for cooling in industries, commercial buildings, and data centers, and the compressor is their powerhouse, driving the refrigeration cycle. Choosing the right compressor type can make or break a chiller’s efficiency, reliability, and cost-effectiveness. This guide explores the main types of chiller compressors—reciprocating, rotary vane, scroll, screw, and centrifugal—detailing how they work, their strengths, weaknesses, and where they shine, helping you pick the best fit for your cooling needs.
What Is a Chiller Compressor?
A chiller compressor pumps refrigerant through the system, compressing low-pressure gas into a high-pressure, high-temperature state to kickstart the cooling process. It’s the heart of the vapor compression cycle, where refrigerant absorbs heat from a fluid (like water) in the evaporator, gets compressed, releases heat in the condenser, and expands to cool again. Compressors vary in design, each suited to specific cooling loads, from small offices to massive factories.
How Compressors Work
All chiller compressors follow the same basic principle:
- Intake: Low-pressure refrigerant gas enters from the evaporator.
- Compression: The compressor squeezes the gas, raising its pressure and temperature (e.g., to 150°F or 66°C).
- Discharge: Hot, high-pressure gas flows to the condenser, where it releases heat.
- Cycle: The refrigerant continues to the expansion valve and evaporator, repeating the process.
The compressor’s design—whether pistons, screws, or impellers—determines how it compresses the gas, affecting efficiency, noise, and maintenance.
Types of Chiller Compressors
Reciprocating Compressors
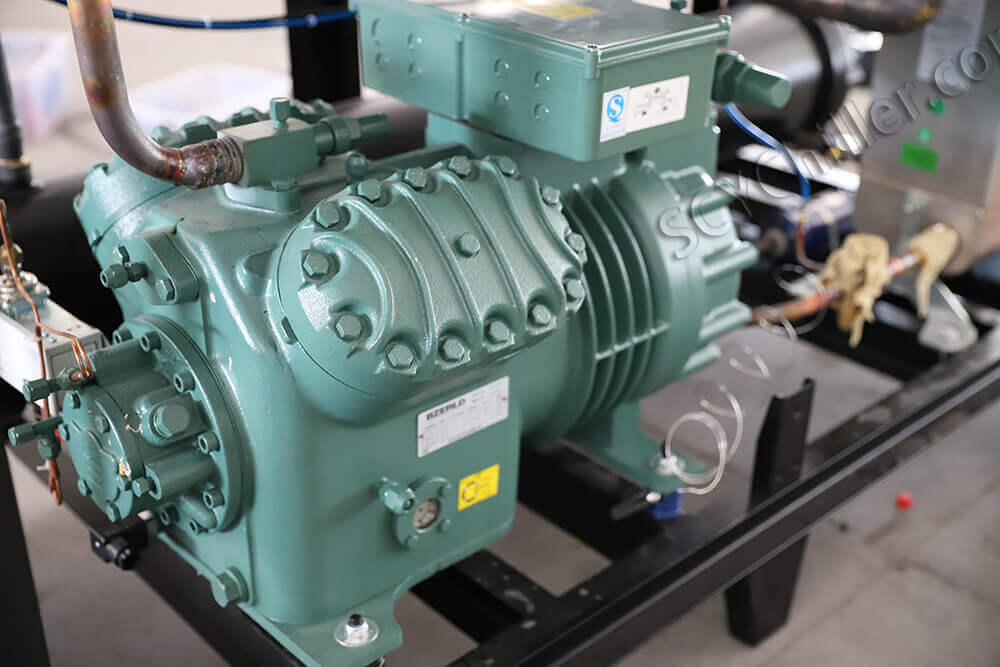
- How They Work: Pistons driven by a crankshaft compress refrigerant in cylinders, like a car engine. Gas enters, gets squeezed, and exits at high pressure.
- Applications: Small to medium chillers (5–150 tons), used in commercial buildings, retail, or older industrial setups.
- Advantages:
- Cost-effective, with lower upfront costs.
- Handles variable loads well, ideal for fluctuating demands.
- Simple design, easy to repair with widely available parts.
- Disadvantages:
- Noisy due to piston movement, often 80–90 dBA.
- Higher maintenance from many moving parts (valves, pistons).
- Less efficient, with COPs around 2.5–3.0.
- Example: A 50-ton reciprocating chiller cooling a small office, handling 600,000 BTU/h with affordable reliability.
Rotary Vane Compressors
- How They Work: A rotor with sliding vanes spins in a cylindrical chamber, trapping and compressing refrigerant as vanes extend and retract.
- Applications: Smaller chillers (1–30 tons), often in portable units or light commercial settings like restaurants.
- Advantages:
- Compact and lightweight, fitting tight spaces.
- Quieter than reciprocating, around 60–70 dBA.
- Smooth operation with fewer vibrations.
- Disadvantages:
- Limited capacity, not suited for large loads.
- Vanes wear out faster, needing replacement every 3–5 years.
- Moderate efficiency, with COPs of 2.8–3.2.
- Example: A 10-ton rotary vane chiller cooling a café, maintaining 72°F (22°C) with minimal noise.
Scroll Compressors
- How They Work: Two spiral-shaped scrolls interlock—one fixed, one orbiting—to compress refrigerant in shrinking pockets, pushing it to the center.
- Applications: Small to medium chillers (10–100 tons), popular in offices, schools, and light industrial use.
- Advantages:
- Quiet, around 50–60 dBA, ideal for noise-sensitive areas.
- High efficiency, with COPs of 3.0–3.5, saving energy.
- Fewer moving parts, reducing maintenance needs.
- Disadvantages:
- Higher initial cost than reciprocating.
- Limited to smaller capacities, less effective above 100 tons.
- Sensitive to liquid refrigerant, requiring careful control.
- Example: A 30-ton scroll chiller in a school, cooling classrooms to 70°F (21°C) with low noise and energy use.
Screw Compressors
- How They Work: Two interlocking helical rotors (screws) rotate, trapping and compressing refrigerant from one end to the other.
- Applications: Medium to large chillers (70–600 tons), used in factories, hospitals, and data centers.
- Advantages:
- High efficiency, with COPs of 3.5–4.0, even at partial loads.
- Reliable for continuous operation, lasting 20–25 years.
- Handles large capacities well, up to 600 tons.
- Disadvantages:
- Expensive upfront, often 20–30% more than scroll.
- Complex maintenance, needing specialized technicians.
- Moderate noise, around 70–80 dBA.
- Example: A 200-ton screw chiller in a factory, cooling machinery at 50°F (10°C), running 24/7 with high efficiency.
Centrifugal Compressors
- How They Work: A spinning impeller accelerates refrigerant, using centrifugal force to compress it, often with multiple stages for high pressure.
- Applications: Large chillers (200–2,000 tons), ideal for district cooling, airports, or industrial plants.
- Advantages:
- Top efficiency, with COPs of 4.0–6.0, especially at full load.
- Low maintenance, with magnetic bearings reducing wear.
- High capacity, handling massive loads like 24 million BTU/h.
- Disadvantages:
- Very high initial cost, sometimes $500,000+.
- Poor efficiency at low loads, below 30% capacity.
- Large footprint, needing significant space.
- Example: A 1,000-ton centrifugal chiller in a data center, keeping servers at 68°F (20°C) with unmatched efficiency.
Compressor Type | Initial Cost | Energy Efficiency (Full Load) | Part-Load Performance | Maintenance Needs | Typical Capacity Range |
---|---|---|---|---|---|
Reciprocating | Low | Moderate | Good | High | Small to Medium (up to ~150 tons) |
Scroll | Moderate | Good | Good | Low | Medium (up to ~200 tons) |
Screw | High | Good | Excellent | Moderate | Medium to Large (up to 500 tons) |
Centrifugal | High | Excellent | Poor (improves with VSD) | Low | Large to Very Large (>200 tons) |
Choosing the Right Compressor
Selecting a compressor depends on:
- Cooling Load: Small (scroll, reciprocating), medium (screw, scroll), or large (centrifugal, screw).
- Efficiency Needs: High COP for energy savings (centrifugal, screw) or budget-friendly (reciprocating).
- Space: Compact (scroll, plate) or larger (shell and tube).
- Noise: Quiet (scroll) or tolerable (screw, centrifugal).
- Budget: Lower cost (reciprocating) vs. long-term savings (screw, centrifugal).
For example, a small office might pick a 20-ton scroll chiller for quiet efficiency, while a chemical plant could opt for a 500-ton screw chiller for reliability.
Maintenance Tips
Keep compressors running smoothly with:
- Oil Checks: Change synthetic oil (e.g., POE) every 1–2 years, checking levels monthly.
- Filter Cleaning: Replace air and oil filters every 6–12 months to avoid clogs.
- Vibration Monitoring: Inspect quarterly for unusual shakes, signaling wear.
- Refrigerant Levels: Verify quarterly; a 5% loss cuts efficiency by 8%.
- Professional Service: Annual tune-ups catch issues early, saving 10–20% on energy.
Conclusion
Chiller compressors—reciprocating, rotary vane, scroll, screw, and centrifugal—each bring unique strengths to cooling systems. From quiet scroll units in offices to powerful centrifugal chillers in factories, understanding their functions and applications helps you choose wisely. With proper maintenance and an eye on trends like low-GWP refrigerants, you can ensure efficiency, reliability, and cost savings for years to come.
FAQ
1. What is a chiller compressor?
A chiller compressor is the component that compresses refrigerant gas, driving the refrigeration cycle to remove heat and provide cooling.
2. What are the main types of chiller compressors?
The main types are reciprocating, rotary vane, scroll, screw, and centrifugal, each suited to different cooling capacities and applications.
3. Which compressor is best for small chillers?
Scroll compressors are ideal for small chillers (10–100 tons) due to their quiet operation and efficiency.
4. What’s the most efficient compressor type?
Centrifugal compressors are typically the most efficient, with COPs of 4.0–6.0, especially for large loads, followed by screw compressors.
5. How do I choose the right compressor for my chiller?
Consider cooling load, efficiency needs, space, noise, and budget. Consult an engineer to match your specific requirements.
6. What are the maintenance needs for chiller compressors?
Regular oil changes, filter replacements, vibration checks, and refrigerant monitoring, with annual professional servicing.
7. How do compressor types affect energy costs?
High-efficiency types like centrifugal and screw save energy (COP 3.5–6.0), while reciprocating may use more (COP 2.5–3.0).
8. Are there eco-friendly compressor options?
Yes, newer models use low-GWP refrigerants like R-32, and centrifugal units with magnetic bearings reduce environmental impact.
9. What’s the lifespan of a chiller compressor?
With maintenance: reciprocating (10–15 years), scroll (15–20 years), screw (20–25 years), centrifugal (25+ years).
10. How noisy are chiller compressors?
Reciprocating are loudest (80–90 dBA), scroll quietest (50–60 dBA), screw and centrifugal moderate (70–80 dBA).