Anodizing&Plating Processes are two widely used surface treatment methods in industrial production, aimed at improving the performance, durability, and aesthetic appeal of metal and plastic components. Anodizing is an electrochemical process that creates a thick, protective oxide layer on the surface of a metal substrate, through the controlled oxidation of the material. This oxide layer not only enhances the metal’s resistance to corrosion, wear and tear, and temperature but can also serve as a base for coloring or printing.
一方、メッキは、電気メッキまたは無電解メッキ法のいずれかを使用して、基板の表面に金属の薄層を堆積させるプロセスです。めっきは、通常、基材の表面硬度、耐摩耗性、電気伝導性を向上させるために使用されますが、装飾目的で使用することもできます。陽極酸化処理とメッキ処理の両方で、高品質で一貫した結果を保証するためにさまざまなパラメーターを厳密に制御する必要があり、自動車、航空宇宙、電子機器、建設などのさまざまな業界で重要な役割を果たしています。
どちらのプロセスも基板の表面特性を向上させることを目的としていますが、メカニズムと用途が異なります。次のセクションでは、めっきプロセスと陽極酸化プロセスの原理、プロセス、およびアプリケーションについて説明します。これには、さまざまな種類のめっきと陽極酸化、それぞれの長所と短所、および各プロセスの課題と革新が含まれます。また、冷却水の重要性と、めっきおよび陽極酸化プロセスの品質と効率を確保するためのチラーの役割についても説明します。
陽極酸化プロセス
陽極酸化プロセスは、金属基板の表面に厚い保護酸化層を作成します。このプロセスでは、通常は酸である電解質溶液に金属基板を浸し、そこに電流を流します。その結果、電解質溶液中の酸素イオンが金属基板の表面に引き付けられ、金属原子と結合して、酸化アルミニウムの安定した緻密な層を形成します。この酸化物層は、腐食、磨耗、および環境要因に対する優れたバリアを提供します。アルマイト処理は、硫酸アルマイト、クロム酸アルマイト、硬質アルマイトなど、目的とする酸化皮膜の性質に応じてさまざまな種類があります。陽極酸化プロセスは、金属の組成を変えない安全で環境に優しいプロセスであり、航空宇宙、自動車、建設産業などの幅広い用途に適しています。
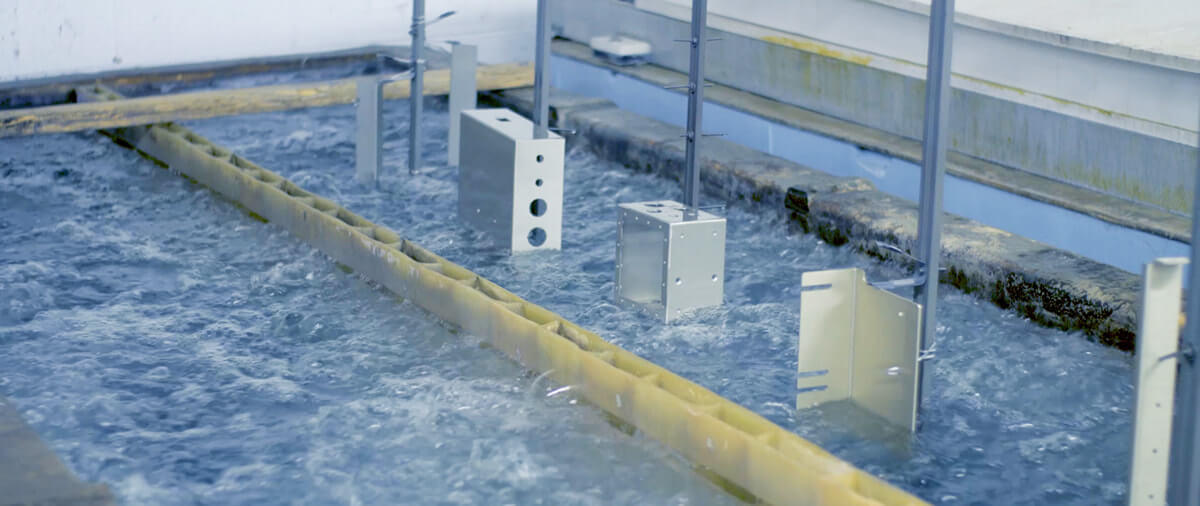
陽極酸化処理の種類
陽極酸化処理は、使用する電解液と酸化物層の望ましい特性に基づいてさまざまなタイプに分類できる汎用性の高い表面処理方法です。
- 硫酸アルマイト 陽極酸化プロセスの最も一般的なタイプであり、腐食、摩耗、および環境要因に対して非常に耐性のある緻密で硬い酸化物層が得られます。このタイプの陽極酸化は、さまざまな色や美的効果を得るために、さらに染色または塗装することができます。
- クロム酸アルマイト一方、基板への密着性が高く、航空宇宙および電気用途に最適な、より薄く柔軟な酸化物層が得られます。
- ハードアルマイト は、より高い電圧と温度を伴う硫酸陽極酸化の一種であり、ピストンロッドや油圧シリンダーなどの高応力用途に適した、厚くて耐摩耗性の酸化層が得られます。
陽極酸化プロセスは、航空宇宙、自動車、電子機器、建設など、さまざまな業界で幅広い用途があります。アルマイト処理された部品は、航空機の構造、自動車の車体、電子機器のハウジング、および建築仕上げに一般的に使用されています。陽極酸化プロセスの利点には、耐腐食性、耐摩耗性、および美的魅力の向上が含まれ、さまざまな基材に対して一般的で費用対効果の高い表面処理方法となっています。
陽極酸化処理の長所と短所
陽極酸化処理は広く使用されている表面処理方法で、いくつかの利点がありますが、いくつかの制限もあります。
陽極酸化プロセスの利点には、基材の機能的および美的特性を向上させる、硬く、耐久性があり、耐腐食性の表面層の作成が含まれます。陽極酸化は、金属の組成を変えない安全で環境に優しいプロセスでもあります。さらに、陽極酸化プロセスはさまざまなタイプで実行できるため、さまざまな色、仕上げ、および特性を柔軟に実現できます。
ただし、陽極酸化処理にはいくつかの制限もあります。例えば、酸化物層の厚さは制限されており、基板の機械的特性に影響を与える可能性があります。陽極酸化プロセスでは、さまざまなプロセスパラメーターを厳密に制御する必要があるため、生産に必要なコストと時間が増加する可能性があります。さらに、クロム酸陽極酸化などの一部のタイプの陽極酸化は、健康や環境に有害な場合があります。これらの制限にもかかわらず、陽極酸化プロセスは、さまざまな用途で人気があり、費用対効果の高い表面処理方法であり続けています。
長所 | 短所 |
硬く、耐久性があり、耐腐食性の表層 | 酸化物層の厚さが限られているため、機械的特性に影響を与える可能性があります |
安全で環境に優しいプロセス | さまざまなプロセス パラメータを厳密に制御する必要があり、コストと時間が増加する |
さまざまな色、仕上げ、特性を柔軟に実現 | 陽極酸化の種類によっては、健康や環境に有害な場合があります |
アルマイトの品質検査方法
陽極酸化プロセスで高品質で一貫した結果を保証するために、さまざまな品質検査と管理方法が使用されます。最も一般的な方法の 1 つは、渦電流試験、蛍光 X 線、磁気誘導などの非破壊検査技術を使用して、酸化物層の厚さと多孔性を測定することです。アルマイト処理された部品の表面の外観、色、および光沢は、目視または比色計と光沢計を使用して検査できます。他の品質管理方法には、塩水噴霧試験、スクラッチ試験、および剥離試験を使用した陽極酸化層の耐食性、耐摩耗性、および接着強度の試験が含まれます。陽極酸化プロセスの品質と一貫性を維持するには、電解液の濃度と pH 値、温度と電流密度、攪拌速度など、さまざまなプロセス パラメータを制御することが重要です。リアルタイムの監視およびフィードバック システムは、プロセスの逸脱を特定して修正するのに役立ち、最終製品が望ましい仕様と性能要件を満たしていることを保証します。
方法 | 目的 |
非破壊検査技術 | 渦電流、XRF、または MI を使用して、酸化物層の厚さと空隙率を測定します |
目視検査と器具 | 目視検査または機器を使用して、表面の外観、色、および光沢を検査します |
耐食性試験 | 塩水噴霧試験を使用して、陽極酸化層の耐食性を試験します |
耐摩耗試験 | スクラッチテストを使用して、陽極酸化層の耐摩耗性をテストします |
接着強度試験 | 剥離試験を使用して、陽極酸化層の接着強度をテストします |
プロセス制御パラメータ | 電解液濃度、温度などのプロセスパラメータを制御します。 |
リアルタイム監視システム | プロセスの逸脱をリアルタイムで特定して修正し、一貫した結果を保証 |
メッキ工程
メッキプロセスは、電気メッキまたは無電解メッキプロセスを使用して、基板表面に金属の薄層を堆積させることを含む表面処理方法です。電気めっきは、金属イオンを含む電解液に電流を流し、金属イオンを基板に引き付けて表面に堆積させるプロセスです。一方、無電解メッキは、外部電流を必要とせずに金属イオンを基板表面に堆積させる化学還元反応を伴います。めっき処理は、金属、プラスチック、セラミックスなどのさまざまな基材に実行して、耐摩耗性、耐食性、電気伝導性などの表面特性を向上させることができます。めっき層の厚さ、密着性、および特性は、めっき液の組成と pH 値、温度と攪拌速度、および電流密度などのさまざまなプロセス パラメータを調整することによって制御できます。次のセクションでは、さまざまな種類のめっきプロセス、その長所と短所、およびさまざまな業界での用途について説明します。また、冷却水の重要性とめっきプロセスにおけるチラーの役割についても説明します。
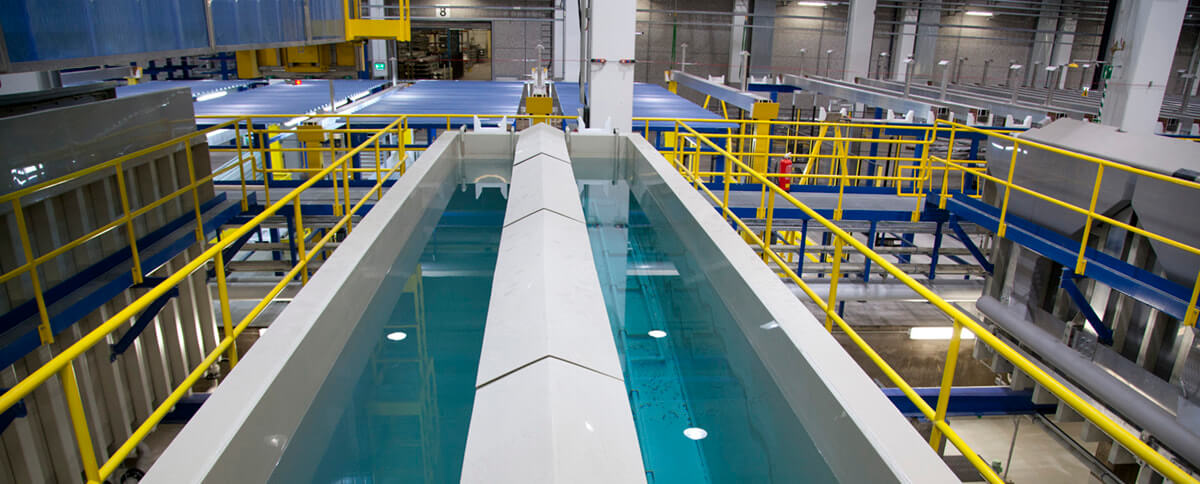
めっき工程の種類
めっき工程は、めっき液に使用する金属の種類、下地の材質、めっき層の性質などにより、さまざまな種類に分類できます。メッキ処理の最も一般的なタイプには、無電解ニッケルメッキ、金メッキ、銀メッキ、銅メッキなどがあります。
- 無電解ニッケルめっきは、優れた耐摩耗性、耐食性、および硬度特性を提供する、広く使用されているタイプのめっきプロセスです。
- 金メッキは、その優れた導電性、耐食性、美的魅力で知られており、電子機器や宝飾品の用途に適しています。
- 銀メッキは、優れた導電性を提供するもう 1 つの一般的なメッキ プロセスであり、電気接点やコネクタで一般的に使用されています。
- 銅めっきは、めっき層の密着性と耐食性を高めるために、他の種類のめっきの下層としてよく使用されます。
めっきプロセスは、航空宇宙、自動車、エレクトロニクス、医療など、さまざまな業界で幅広い用途があります。基材の性能、外観、および耐久性を向上させるために使用でき、部品、コンポーネント、および完成品の製造によく使用されます。めっきプロセスの利点には、特性の改善、低コスト、環境への配慮が含まれ、さまざまな用途で人気があり費用対効果の高い表面処理方法となっています。
メッキプロセスの長所と短所
めっきプロセスの利点には、基板表面に金属の薄層を堆積させる機能が含まれます。これにより、耐摩耗性、耐食性、導電性などの基板の表面特性が向上します。メッキ処理も様々な基材に対応できるため、汎用性の高い表面処理方法です。さらに、めっきプロセスはさまざまなタイプで実行できるため、さまざまな特性と仕上げを柔軟に実現できます。
メッキ加工の限界。たとえば、このプロセスではさまざまなプロセス パラメータを厳密に制御する必要があり、生産に必要なコストと時間が増加する可能性があります。さらに、電気めっきなどの一部のめっきプロセスでは、大量の電力が必要となり、環境に有害な廃水が発生します。これらの制限にもかかわらず、めっきプロセスは、さまざまな用途で人気があり、費用対効果の高い表面処理方法であり続けています。
長所 | 短所 |
基板表面への金属薄層の堆積 | さまざまなパラメーターを厳密に制御する必要があり、生産コストと時間が増加します |
基材の表面特性を向上 | 特定の種類のメッキ プロセスでは、廃水が発生し、大量の電力が消費され、環境に有害な場合があります。 |
汎用性があり、さまざまな基板で実行できます | |
さまざまなタイプが利用可能で、さまざまな特性と仕上げが可能 |
めっき品質検査方法
品質の検査と管理は、高品質で一貫した結果を保証するために、めっきプロセスで非常に重要です。最も一般的な品質管理方法には、めっき層の厚さと密着強度の測定、表面の欠陥の目視検査、めっき層の耐食性、耐摩耗性、電気伝導性の試験などがあります。これらのテストは通常、蛍光 X 線や磁気誘導などの非破壊技術を使用して実行されます。テストに加えて、めっき液の組成と pH 値、温度と攪拌速度、電流密度などのさまざまなプロセス パラメータを制御することは、めっき層の品質と一貫性を維持するために重要です。リアルタイムの監視およびフィードバック システムは、プロセスの逸脱を特定して修正するのに役立ち、最終製品が望ましい仕様と性能要件を満たしていることを保証します。厳格な品質管理システムを実装することにより、Plating Process は、さまざまな用途向けの高品質で信頼性が高く、費用対効果の高い製品を生産できます。
方法 | 目的 |
非破壊検査技術 | XRFまたは磁気誘導を使用してメッキ層の厚さと密着強度を測定します |
外観検査 | 表面に欠陥がないか視覚的に検査する |
耐食性試験 | 塩水噴霧試験によるめっき層の耐食性試験 |
耐摩耗試験 | スクラッチテストを使用してメッキ層の耐摩耗性をテストします |
電気伝導度試験 | 抵抗試験を使用してメッキ層の電気伝導度をテストします |
プロセス制御パラメータ | めっき液の組成、温度などのプロセス パラメータを制御します。 |
リアルタイム監視システム | プロセスの逸脱をリアルタイムで特定して修正し、一貫した結果を保証 |
Cooling Water Requirements in Anodizing&Plating Process
温度制御は、陽極酸化プロセスとメッキプロセスの両方で重要な要素です。両方のプロセスで使用されるめっき液または電解液には、特定の許容範囲内に維持する必要がある温度範囲があります。めっき液または電解液の温度は、めっき速度、厚さ、品質、およびめっき層の特性に影響を与えます。例えば、温度が高すぎると、めっき層が多孔質になったり、もろくなったり、接着強度が低下したりすることがあります。一方、温度が低すぎると、めっき速度が遅すぎて、不均一な堆積や不均一な特性につながる可能性があります。適切な温度範囲を維持するために、チラーやヒーターなどの温度制御システムを使用して、メッキまたは電解液の温度を調節するのが一般的です。温度制御システムで使用される冷却水の温度も重要であり、メッキまたは電解液の温度が望ましい範囲内にとどまるように慎重に制御する必要があります。次のセクションでは、陽極酸化およびめっきプロセスにおける冷却水の要件とチラーの役割について説明します。
Application of Chiller in Anodizing&Plating Process
Chillers play a critical role in maintaining the proper temperature range in Anodizing&Plating Process. Chillers are commonly used to cool the plating or electrolyte solution to maintain the proper temperature range for consistent plating results. Chillers remove the excess heat generated by the Anodizing&Plating Process and maintain the temperature within the desired range. The cooling capacity of the chiller must be matched to the specific requirements of the Anodizing&Plating Process to ensure proper temperature control. Different types of chillers, such as air-cooled or water-cooled chillers, may be used depending on the application and process requirements. The chiller can also provide additional benefits, such as increased energy efficiency, reduced water usage, and improved equipment lifespan. In addition to providing temperature control, chillers can also offer other features such as flow rate monitoring and automatic temperature control to help maintain optimal process conditions. The proper application of chillers can help to ensure consistent and high-quality results in Anodizing&Plating Process.
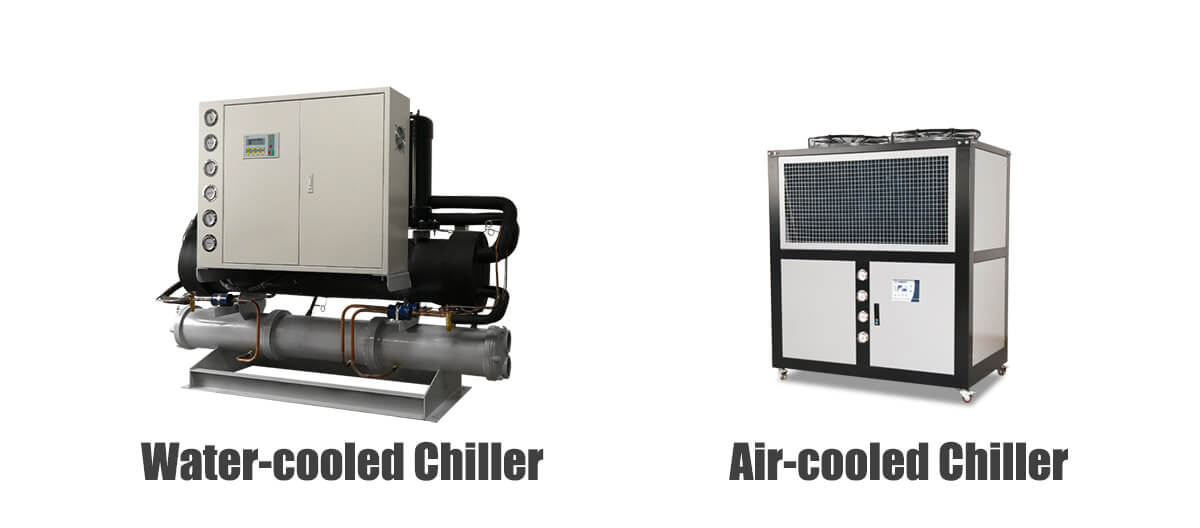
チラー選定・構成のポイント
- 冷却能力: The cooling capacity of the chiller should be matched to the specific requirements of the Anodizing&Plating Process to ensure proper temperature control. The cooling capacity of the chiller is typically measured in tons or kilowatts and should be selected based on the heat load of the process. If you have data like the temperature difference of in&out water, and the flow rate of the solution, please refer to our チラーサイズ計算機。
- チラーのタイプ: 空冷式や水冷式などのチラーのタイプは、特定の用途やプロセス要件に基づいて選択する必要があります。 水冷チラー 通常、より効率的で、より高い冷却能力を提供できますが、冷却塔へのアクセスが必要であり、より多くの水を消費します。 空冷チラー一方、 は設置と保守が簡単ですが、冷却能力が低く、廃熱を排出するためにより多くのスペースが必要です。
- 温度制御範囲: The chiller should be able to maintain the temperature of the plating or electrolyte solution within a specific range. The range is typically determined by the specific requirements of the Anodizing&Plating Process, and the chiller should be selected based on its ability to maintain the required temperature range.
- 流量と圧力: 冷却水の流量と圧力は、チラーの要件に適合している必要があります。流量と圧力はチラーの性能と効率に影響を与える可能性があるため、冷却水システムが適切に設計および構成されていることを確認することが重要です。
- エネルギー効率: 運用コストを最小限に抑え、環境への影響を軽減するには、チラーのエネルギー効率を考慮する必要があります。エネルギー効率の高いチラーは、エネルギー コストを削減し、温室効果ガスの排出を削減するのに役立ちます。
- メンテナンスとサービス: チラーは、ダウンタイムを最小限に抑え、信頼性の高い動作を確保するために、メンテナンスとサービスが容易でなければなりません。熱交換器の清掃やフィルターの交換などの定期的なメンテナンスは、チラーの性能を維持し、寿命を延ばすのに役立ちます。
By considering these key points, it is possible to select and configure a chiller that meets the specific requirements of Anodizing&Plating Process and provides reliable, efficient, and cost-effective temperature control.
チラーのトラブルシューティング
Proper maintenance and operation of a chiller are crucial for reliable and consistent temperature control in Anodizing&Plating Process. However, if a problem does occur, it is important to be able to troubleshoot the issue and identify the root cause of the problem. Common issues with chillers can include low refrigerant levels, clogged filters, or failed components such as compressors or heat exchangers. In some cases, the problem may be related to the cooling water system rather than the chiller itself, such as issues with water flow or pressure. Troubleshooting can involve various methods such as visual inspection, measuring temperatures and pressures, or using diagnostic tools such as vibration analysis. By identifying and addressing the root cause of the problem, it is possible to minimize downtime and ensure that the Anodizing&Plating Process can continue to operate at optimal performance levels. Regular maintenance and monitoring can also help to prevent issues from occurring and ensure that the chiller and cooling water system are operating reliably and efficiently. For more detailed troubleshooting information, please refer to 冷凍システムの故障のトップ 10 チェックリスト。
Innovative Technologies in Anodizing&Plating Process
Advancements in technology have led to the development of new and innovative approaches for Anodizing&Plating Processes. These technologies can offer benefits such as improved efficiency, reduced environmental impact, and enhanced performance.
たとえば、パルスめっきは、断続的な電流を使用して金属イオンを基板上に堆積させる技術であり、その結果、接着性と均一性が向上します。
別の例は、外部電源を必要とせずに基板上に金属層を堆積させる無電解めっきの使用です。この技術により、耐食性や硬度などの特性が向上します。
In addition, various nanotechnology-based approaches, such as the use of nanostructured coatings or surface modifications, are being explored for Anodizing&Plating Process to enhance the performance and durability of plated surfaces. These innovative technologies have the potential to revolutionize the Anodizing&Plating Process industry and offer new possibilities for advanced surface treatments.
結論
Anodizing&Plating Process plays a crucial role in many industrial applications by providing enhanced surface properties, such as corrosion resistance, wear resistance, and improved aesthetics. The processes are widely used in various industries such as automotive, aerospace, electronics, and medical devices. The high demand for these processes has led to the development of new technologies and approaches for improving efficiency, performance, and sustainability. The use of chillers and temperature control systems is critical for maintaining the proper temperature range and ensuring consistent and reliable plating results. Advanced technologies such as pulse plating, electroless plating, and nanotechnology-based approaches offer exciting possibilities for the future of Anodizing&Plating Process. As industrial applications continue to grow and evolve, the demand for Anodizing&Plating Process is expected to increase, driving further advancements in technology and new approaches to surface treatments.
Status and Role of Chiller in Anodizing&Plating Process
Chillers play a critical role in the Anodizing&Plating Process industry by providing reliable and efficient temperature control for plating solutions and electrolyte solutions. The use of chillers is widespread and essential for ensuring consistent plating results and maintaining high product quality. In addition, chillers offer benefits such as improved energy efficiency, reduced water usage, and longer equipment lifespan. As new plating and surface treatment technologies continue to emerge, the role of chillers is expected to become even more important in ensuring optimal process conditions and performance. As a result, the Anodizing&Plating Process industry is likely to continue to rely on chillers and other temperature control systems for the foreseeable future.
Professional Anodizing&Plating Process Chiller Supplier
If you’re in need of a reliable and efficient chiller for your Anodizing&Plating Process, look no further than SCY Chiller. Our chillers are designed to provide precise temperature control for a wide range of industrial applications, including plating and surface treatment processes. We offer a variety of chiller types, such as air-cooled and water-cooled chillers, to meet your specific needs and requirements. Our chillers are energy-efficient, easy to operate, and require minimal maintenance, ensuring that your Anodizing&Plating Process runs smoothly and efficiently. お問い合わせ today to learn more about our chiller solutions and how we can help optimize your Anodizing&Plating Process.