กระบวนการอะโนไดซ์และการชุบเป็นวิธีการรักษาพื้นผิวที่ใช้กันอย่างแพร่หลายในการผลิตอุตสาหกรรมโดยมีวัตถุประสงค์เพื่อปรับปรุงประสิทธิภาพความทนทานและความสวยงามของส่วนประกอบโลหะและพลาสติก อโนไดซ์เป็นกระบวนการทางเคมีไฟฟ้าที่สร้างชั้นออกไซด์ที่มีความหนาและป้องกันบนพื้นผิวของพื้นผิวโลหะผ่านการออกซิเดชั่นควบคุมของวัสดุ ชั้นออกไซด์นี้ไม่เพียง แต่ช่วยเพิ่มความต้านทานของโลหะต่อการกัดกร่อนการสึกหรอและการฉีกขาด แต่ยังสามารถใช้เป็นฐานสำหรับการระบายสีหรือการพิมพ์
ในทางกลับกัน การชุบเป็นกระบวนการที่เกี่ยวข้องกับการเคลือบชั้นโลหะบาง ๆ บนพื้นผิวของวัสดุพิมพ์โดยใช้วิธีการชุบด้วยไฟฟ้าหรือการชุบแบบไม่ใช้ไฟฟ้า การชุบมักใช้เพื่อปรับปรุงความแข็งของพื้นผิว ความต้านทานต่อการขัดถู และการนำไฟฟ้าของพื้นผิว แต่ยังสามารถใช้เพื่อการตกแต่งได้อีกด้วย ทั้งกระบวนการอโนไดซ์และการชุบจำเป็นต้องมีการควบคุมอย่างเข้มงวดของพารามิเตอร์ต่างๆ เพื่อให้แน่ใจว่ามีคุณภาพสูงและได้ผลลัพธ์ที่สม่ำเสมอ ทำให้เป็นส่วนสำคัญของอุตสาหกรรมต่างๆ รวมถึงยานยนต์ การบินและอวกาศ อิเล็กทรอนิกส์ และการก่อสร้าง
แม้ว่าทั้งสองกระบวนการมีเป้าหมายเพื่อเพิ่มคุณสมบัติพื้นผิวของวัสดุพิมพ์ แต่กลไกและการใช้งานต่างกัน ในหัวข้อต่อไปนี้ เราจะอธิบายหลักการ กระบวนการ และการใช้งานของกระบวนการชุบและกระบวนการอโนไดซ์ รวมถึงการชุบและการอโนไดซ์ประเภทต่างๆ ข้อดีและข้อเสียที่เกี่ยวข้อง ตลอดจนความท้าทายและนวัตกรรมในแต่ละกระบวนการ นอกจากนี้ เราจะหารือเกี่ยวกับความสำคัญของน้ำหล่อเย็นและบทบาทของเครื่องทำความเย็นในการประกันคุณภาพและประสิทธิภาพของกระบวนการชุบและอโนไดซ์
กระบวนการอโนไดซ์
กระบวนการอโนไดซ์จะสร้างชั้นออกไซด์ที่หนาและป้องกันบนพื้นผิวของพื้นผิวโลหะ กระบวนการนี้เกี่ยวข้องกับการจุ่มพื้นผิวโลหะลงในสารละลายอิเล็กโทรไลต์ ซึ่งโดยทั่วไปคือกรด และส่งกระแสไฟฟ้าผ่านสารละลายนั้น เป็นผลให้ไอออนออกซิเจนในสารละลายอิเล็กโทรไลต์ถูกดึงดูดไปยังพื้นผิวของพื้นผิวโลหะและรวมตัวกับอะตอมของโลหะเพื่อสร้างชั้นอะลูมิเนียมออกไซด์ที่เสถียรและหนาแน่น ชั้นออกไซด์นี้ช่วยป้องกันการกัดกร่อน การสึกหรอ และปัจจัยด้านสิ่งแวดล้อมได้อย่างดีเยี่ยม กระบวนการอโนไดซ์สามารถทำได้หลายประเภท ได้แก่ การอโนไดซ์ด้วยกรดซัลฟิวริก การอโนไดซ์ด้วยกรดโครมิก และการอโนไดซ์แบบแข็ง ขึ้นอยู่กับคุณสมบัติที่ต้องการของชั้นออกไซด์ กระบวนการอโนไดซ์เป็นกระบวนการที่ปลอดภัยและเป็นมิตรกับสิ่งแวดล้อมซึ่งไม่ทำให้องค์ประกอบของโลหะเปลี่ยนแปลง ทำให้เหมาะสำหรับการใช้งานที่หลากหลาย รวมถึงอุตสาหกรรมการบินและอวกาศ ยานยนต์ และการก่อสร้าง
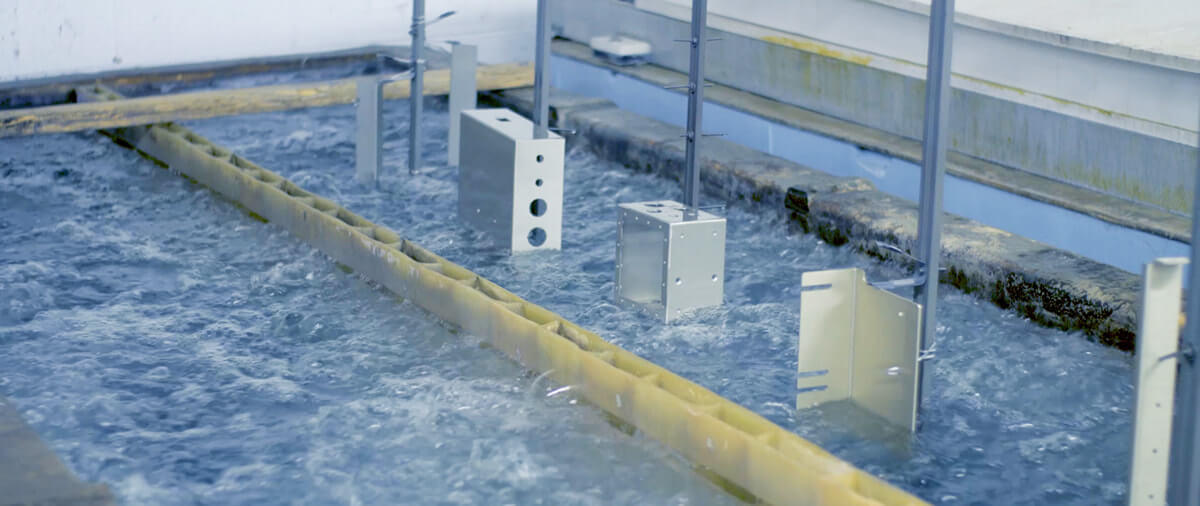
ประเภทของกระบวนการอโนไดซ์
กระบวนการอโนไดซ์เป็นวิธีการชุบผิวอเนกประสงค์ที่สามารถจำแนกเป็นประเภทต่างๆ ตามสารละลายอิเล็กโทรไลต์ที่ใช้และคุณสมบัติที่ต้องการของชั้นออกไซด์
- อโนไดซ์กรดซัลฟิวริก เป็นกระบวนการอโนไดซ์ประเภทที่พบมากที่สุดและส่งผลให้ชั้นออกไซด์มีความหนาแน่นและแข็งซึ่งมีความทนทานสูงต่อการกัดกร่อน การสึกหรอ และปัจจัยด้านสิ่งแวดล้อม อโนไดซ์ประเภทนี้สามารถนำไปย้อมหรือทาสีเพิ่มเติมเพื่อให้ได้สีและความสวยงามที่แตกต่างกัน
- กรดโครมิกอโนไดซ์ในทางกลับกัน ส่งผลให้ชั้นออกไซด์บางลงและมีความยืดหยุ่นมากขึ้น ซึ่งมีการยึดเกาะที่ดีกับพื้นผิว และเหมาะสำหรับการใช้งานด้านการบินและอวกาศและไฟฟ้า
- ฮาร์ดอโนไดซ์ เป็นอโนไดซ์กรดกำมะถันประเภทหนึ่งที่ใช้แรงดันและอุณหภูมิที่สูงขึ้น ส่งผลให้ชั้นออกไซด์หนาและทนทานต่อการสึกหรอ ซึ่งเหมาะสำหรับการใช้งานที่มีความเครียดสูง เช่น ก้านลูกสูบและกระบอกไฮดรอลิก
กระบวนการอโนไดซ์มีการใช้งานที่หลากหลายในอุตสาหกรรมต่างๆ รวมถึงการบินและอวกาศ ยานยนต์ อิเล็กทรอนิกส์ และการก่อสร้าง ชิ้นส่วนอะโนไดซ์มักใช้ในโครงสร้างเครื่องบิน ตัวถังรถยนต์ ตัวเรือนอิเล็กทรอนิกส์ และพื้นผิวด้านสถาปัตยกรรม ประโยชน์ของกระบวนการอโนไดซ์ ได้แก่ ความต้านทานการกัดกร่อนที่เพิ่มขึ้น ความทนทานต่อการสึกหรอ และความสวยงาม ทำให้เป็นวิธีการรักษาพื้นผิวที่ได้รับความนิยมและคุ้มค่าสำหรับพื้นผิวต่างๆ
ข้อดีและข้อเสียของกระบวนการอโนไดซ์
กระบวนการอโนไดซ์เป็นวิธีการชุบผิวที่ใช้กันอย่างแพร่หลายซึ่งให้ประโยชน์หลายประการ แต่ก็มีข้อจำกัดบางประการเช่นกัน
ข้อดีของกระบวนการอโนไดซ์ ได้แก่ การสร้างชั้นพื้นผิวที่แข็ง ทนทาน และป้องกันการกัดกร่อน ซึ่งช่วยเพิ่มคุณสมบัติการทำงานและความสวยงามของพื้นผิว การชุบอโนไดซ์ยังเป็นกระบวนการที่ปลอดภัยและเป็นมิตรกับสิ่งแวดล้อม โดยไม่ทำให้ส่วนประกอบของโลหะเปลี่ยนแปลง นอกจากนี้ กระบวนการอโนไดซ์ยังสามารถทำได้หลายประเภท ทำให้มีความยืดหยุ่นในการได้สี พื้นผิว และคุณสมบัติต่างๆ
อย่างไรก็ตาม ยังมีข้อจำกัดบางประการสำหรับกระบวนการอโนไดซ์ ตัวอย่างเช่น ความหนาของชั้นออกไซด์มีจำกัดและอาจส่งผลต่อคุณสมบัติเชิงกลของวัสดุพิมพ์ กระบวนการอโนไดซ์ยังต้องการการควบคุมพารามิเตอร์กระบวนการต่างๆ อย่างเข้มงวด ซึ่งสามารถเพิ่มต้นทุนและเวลาในการผลิตได้ นอกจากนี้ การชุบอโนไดซ์บางประเภท เช่น การชุบด้วยกรดโครมิก อาจเป็นอันตรายต่อสุขภาพและสิ่งแวดล้อม แม้จะมีข้อจำกัดเหล่านี้ กระบวนการอโนไดซ์ยังคงเป็นวิธีการชุบผิวที่ได้รับความนิยมและคุ้มค่าสำหรับการใช้งานที่หลากหลาย
ข้อดี | ข้อเสีย |
ชั้นผิวแข็ง ทนทาน และทนต่อการกัดกร่อน | ความหนาของชั้นออกไซด์ที่จำกัดอาจส่งผลต่อคุณสมบัติทางกล |
กระบวนการที่ปลอดภัยและเป็นมิตรกับสิ่งแวดล้อม | ต้องมีการควบคุมพารามิเตอร์ต่างๆ ของกระบวนการอย่างเข้มงวด ทำให้ต้นทุนและเวลาเพิ่มขึ้น |
ให้ความยืดหยุ่นเพื่อให้ได้สี พื้นผิว และคุณสมบัติที่หลากหลาย | อโนไดซ์บางประเภทอาจเป็นอันตรายต่อสุขภาพและสิ่งแวดล้อม |
วิธีการตรวจสอบคุณภาพอโนไดซ์
เพื่อให้แน่ใจว่ามีคุณภาพสูงและผลลัพธ์ที่สม่ำเสมอในกระบวนการอโนไดซ์ จึงใช้วิธีการตรวจสอบและควบคุมคุณภาพที่หลากหลาย วิธีการหนึ่งที่พบมากที่สุดคือการวัดความหนาและความพรุนของชั้นออกไซด์โดยใช้เทคนิคการทดสอบแบบไม่ทำลาย เช่น การทดสอบกระแสไหลวน การเรืองแสงด้วยรังสีเอกซ์ หรือการเหนี่ยวนำแม่เหล็ก สามารถตรวจสอบลักษณะพื้นผิว สี และความเงาของชิ้นส่วนอะโนไดซ์ได้ด้วยสายตาหรือใช้เครื่องวัดสีและเครื่องวัดความเงา วิธีการควบคุมคุณภาพอื่นๆ ได้แก่ การทดสอบความทนทานต่อการกัดกร่อน ความทนทานต่อการสึกหรอ และความแข็งแรงในการยึดเกาะของชั้นอะโนไดซ์โดยใช้การทดสอบการพ่นเกลือ การทดสอบการขีดข่วน และการทดสอบการลอก เพื่อรักษาคุณภาพและความสม่ำเสมอของกระบวนการอโนไดซ์ สิ่งสำคัญคือต้องควบคุมพารามิเตอร์ต่างๆ ของกระบวนการ รวมถึงความเข้มข้นและค่า pH ของสารละลายอิเล็กโทรไลต์ อุณหภูมิและความหนาแน่นกระแส และอัตราการกวน ระบบการตรวจสอบและข้อเสนอแนะตามเวลาจริงสามารถช่วยระบุและแก้ไขความเบี่ยงเบนของกระบวนการ ทำให้มั่นใจได้ว่าผลิตภัณฑ์ขั้นสุดท้ายตรงตามข้อกำหนดและข้อกำหนดด้านประสิทธิภาพที่ต้องการ
วิธี | วัตถุประสงค์ |
เทคนิคการทดสอบแบบไม่ทำลาย | วัดความหนาและความพรุนของชั้นออกไซด์โดยใช้กระแสไหลวน, XRF หรือ MI |
การตรวจสอบด้วยสายตาและเครื่องมือ | ตรวจสอบลักษณะพื้นผิว สี และความเงาโดยใช้การตรวจสอบด้วยสายตาหรือเครื่องมือ |
การทดสอบความทนทานต่อการกัดกร่อน | ทดสอบความทนทานต่อการกัดกร่อนของชั้นอะโนไดซ์โดยใช้การทดสอบการพ่นเกลือ |
การทดสอบความต้านทานการสึกหรอ | ทดสอบความทนทานต่อการสึกหรอของชั้นอะโนไดซ์โดยใช้การทดสอบการขีดข่วน |
การทดสอบแรงยึดเกาะ | ทดสอบแรงยึดเกาะของชั้นอะโนไดซ์โดยใช้การทดสอบการลอก |
พารามิเตอร์การควบคุมกระบวนการ | ควบคุมพารามิเตอร์ของกระบวนการ เช่น ความเข้มข้นของสารละลายอิเล็กโทรไลต์ อุณหภูมิ ฯลฯ |
ระบบตรวจสอบตามเวลาจริง | ระบุและแก้ไขความเบี่ยงเบนของกระบวนการแบบเรียลไทม์เพื่อให้ได้ผลลัพธ์ที่สอดคล้องกัน |
กระบวนการชุบ
กระบวนการชุบเป็นวิธีการรักษาพื้นผิวที่เกี่ยวข้องกับการเคลือบโลหะบาง ๆ บนพื้นผิวพื้นผิวโดยใช้กระบวนการชุบด้วยไฟฟ้าหรือการชุบแบบไม่ใช้ไฟฟ้า การชุบด้วยไฟฟ้าเป็นกระบวนการที่เกี่ยวข้องกับการส่งผ่านกระแสไฟฟ้าผ่านสารละลายอิเล็กโทรไลต์ที่มีไอออนของโลหะ ซึ่งจะถูกดึงดูดไปยังพื้นผิวและสะสมบนพื้นผิว ในทางกลับกัน การชุบแบบไม่ใช้ไฟฟ้าเกี่ยวข้องกับปฏิกิริยารีดิวซ์ทางเคมีที่สะสมไอออนของโลหะไว้บนพื้นผิวของวัสดุพิมพ์โดยไม่จำเป็นต้องใช้กระแสไฟฟ้าจากภายนอก กระบวนการชุบสามารถทำได้กับพื้นผิวหลายประเภท รวมถึงโลหะ พลาสติก และเซรามิก เพื่อปรับปรุงคุณสมบัติพื้นผิว เช่น ความต้านทานการสึกหรอ ความต้านทานการกัดกร่อน และการนำไฟฟ้า ความหนา การยึดเกาะ และคุณสมบัติของชั้นชุบสามารถควบคุมได้โดยการปรับพารามิเตอร์กระบวนการต่างๆ เช่น องค์ประกอบและค่า pH ของน้ำยาชุบ อุณหภูมิและอัตราการกวน และความหนาแน่นกระแส ในหัวข้อต่อไปนี้ เราจะพูดถึงกระบวนการชุบประเภทต่างๆ ข้อดีและข้อเสีย และการใช้งานในอุตสาหกรรมต่างๆ เราจะหารือเกี่ยวกับความสำคัญของน้ำหล่อเย็นและบทบาทของเครื่องทำความเย็นในกระบวนการชุบ
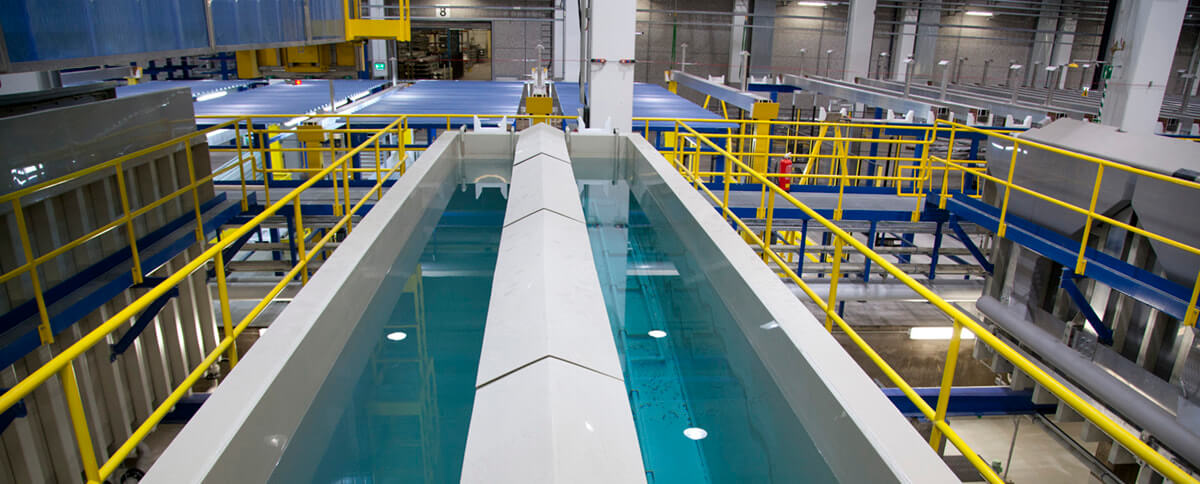
ประเภทของกระบวนการชุบ
กระบวนการชุบแบ่งออกได้เป็นประเภทต่างๆ ตามประเภทของโลหะที่ใช้ในน้ำยาชุบ วัสดุพื้นผิว และคุณสมบัติของชั้นชุบ กระบวนการชุบบางประเภทที่พบมากที่สุด ได้แก่ การชุบนิกเกิลแบบไม่ใช้ไฟฟ้า การชุบทอง การชุบเงิน และการชุบทองแดง
- การชุบนิเกิลแบบไม่ใช้ไฟฟ้าเป็นกระบวนการชุบชนิดหนึ่งที่ใช้กันอย่างแพร่หลายซึ่งให้คุณสมบัติต้านทานการสึกหรอ ต้านทานการกัดกร่อน และความแข็งที่ดีเยี่ยม
- การชุบทองเป็นที่รู้จักกันดีในด้านการนำไฟฟ้าที่ดีเยี่ยม ความต้านทานการกัดกร่อน และความสวยงาม ทำให้เหมาะสำหรับการใช้งานด้านอิเล็กทรอนิกส์และเครื่องประดับ
- การชุบเงินเป็นกระบวนการชุบที่ได้รับความนิยมอีกประเภทหนึ่งซึ่งให้ค่าการนำไฟฟ้าที่ดีเยี่ยมและมักใช้ในหน้าสัมผัสทางไฟฟ้าและคอนเนคเตอร์
- การชุบทองแดงมักใช้เป็นชั้นรองสำหรับการชุบประเภทอื่น ๆ เพื่อเพิ่มคุณสมบัติการยึดเกาะและต้านทานการกัดกร่อนของชั้นชุบ
กระบวนการชุบมีการใช้งานที่หลากหลายในอุตสาหกรรมต่างๆ รวมถึงการบินและอวกาศ ยานยนต์ อิเล็กทรอนิกส์ และการแพทย์ สามารถใช้เพื่อเพิ่มประสิทธิภาพ ลักษณะ และความทนทานของวัสดุพิมพ์ และมักใช้ในการผลิตชิ้นส่วน ส่วนประกอบ และผลิตภัณฑ์สำเร็จรูป ประโยชน์ของกระบวนการชุบผิวรวมถึงคุณสมบัติที่ดีขึ้น ต้นทุนที่ต่ำลง และเป็นมิตรต่อสิ่งแวดล้อม ทำให้เป็นวิธีการชุบผิวที่ได้รับความนิยมและคุ้มค่าสำหรับการใช้งานต่างๆ
ข้อดีและข้อเสียของกระบวนการชุบ
ข้อดีของกระบวนการชุบผิว ได้แก่ ความสามารถในการเคลือบชั้นโลหะบาง ๆ บนพื้นผิวของวัสดุพิมพ์ ซึ่งช่วยเพิ่มคุณสมบัติพื้นผิวของวัสดุพิมพ์ เช่น ความต้านทานการสึกหรอ ความต้านทานการกัดกร่อน และการนำไฟฟ้า กระบวนการชุบผิวสามารถทำได้บนวัสดุหลายประเภท ทำให้เป็นวิธีการรักษาพื้นผิวที่หลากหลาย นอกจากนี้ กระบวนการชุบโลหะสามารถทำได้หลายประเภท ทำให้มีความยืดหยุ่นในการบรรลุคุณสมบัติและพื้นผิวที่หลากหลาย
ข้อจำกัดของกระบวนการชุบ ตัวอย่างเช่น กระบวนการต้องมีการควบคุมอย่างเข้มงวดของพารามิเตอร์กระบวนการต่างๆ ซึ่งสามารถเพิ่มต้นทุนและเวลาที่จำเป็นสำหรับการผลิต นอกจากนี้ กระบวนการชุบบางประเภท เช่น การชุบด้วยไฟฟ้า ต้องใช้ไฟฟ้าจำนวนมากและทำให้เกิดน้ำเสีย ซึ่งอาจเป็นอันตรายต่อสิ่งแวดล้อม แม้จะมีข้อจำกัดเหล่านี้ กระบวนการชุบผิวยังคงเป็นวิธีการชุบผิวที่ได้รับความนิยมและคุ้มค่าสำหรับการใช้งานที่หลากหลาย
ข้อดี | ข้อเสีย |
การทับถมของชั้นโลหะบาง ๆ ลงบนพื้นผิววัสดุพิมพ์ | ต้องมีการควบคุมพารามิเตอร์ต่างๆ อย่างเข้มงวด ทำให้ต้นทุนและเวลาในการผลิตเพิ่มขึ้น |
ปรับปรุงคุณสมบัติพื้นผิวของพื้นผิว | กระบวนการชุบบางประเภทก่อให้เกิดน้ำเสียและใช้ไฟฟ้าจำนวนมาก ซึ่งอาจเป็นอันตรายต่อสิ่งแวดล้อม |
อเนกประสงค์และสามารถทำได้บนวัสดุพิมพ์ที่หลากหลาย | |
มีให้เลือกหลายประเภททำให้มีคุณสมบัติและพื้นผิวที่หลากหลาย |
วิธีการตรวจสอบคุณภาพการชุบ
การตรวจสอบและควบคุมคุณภาพมีความสำคัญอย่างยิ่งในกระบวนการชุบโลหะ เพื่อให้ได้ผลลัพธ์ที่มีคุณภาพสูงและสม่ำเสมอ วิธีการควบคุมคุณภาพทั่วไปบางส่วน ได้แก่ การวัดความหนาและแรงยึดเกาะของชั้นชุบ การตรวจสอบพื้นผิวเพื่อหาข้อบกพร่องด้วยสายตา และการทดสอบความต้านทานการกัดกร่อน ความต้านทานการสึกหรอ และการนำไฟฟ้าของชั้นชุบ การทดสอบเหล่านี้มักดำเนินการโดยใช้เทคนิคที่ไม่ทำลาย เช่น การเรืองแสงด้วยรังสีเอกซ์และการเหนี่ยวนำแม่เหล็ก นอกจากการทดสอบแล้ว การควบคุมพารามิเตอร์ต่างๆ ของกระบวนการ เช่น องค์ประกอบและค่า pH ของน้ำยาชุบ อุณหภูมิและอัตราการกวน และความหนาแน่นของกระแสก็มีความสำคัญต่อการรักษาคุณภาพและความสม่ำเสมอของชั้นชุบ ระบบการตรวจสอบและข้อเสนอแนะตามเวลาจริงสามารถช่วยระบุและแก้ไขความเบี่ยงเบนของกระบวนการ ทำให้มั่นใจได้ว่าผลิตภัณฑ์ขั้นสุดท้ายตรงตามข้อกำหนดและข้อกำหนดด้านประสิทธิภาพที่ต้องการ ด้วยการใช้ระบบควบคุมคุณภาพที่เข้มงวด กระบวนการชุบโลหะสามารถผลิตผลิตภัณฑ์คุณภาพสูง เชื่อถือได้ และคุ้มค่าสำหรับการใช้งานต่างๆ
วิธี | วัตถุประสงค์ |
เทคนิคการทดสอบแบบไม่ทำลาย | วัดความหนาและแรงยึดเกาะของชั้นชุบโดยใช้ XRF หรือการเหนี่ยวนำแม่เหล็ก |
การตรวจสอบด้วยสายตา | ตรวจสอบพื้นผิวเพื่อหาจุดบกพร่องด้วยสายตา |
การทดสอบความทนทานต่อการกัดกร่อน | ทดสอบความทนทานต่อการกัดกร่อนของชั้นชุบโดยใช้การทดสอบการพ่นเกลือ |
การทดสอบความต้านทานการสึกหรอ | ทดสอบความทนทานต่อการสึกหรอของชั้นชุบโดยใช้การทดสอบการขีดข่วน |
การทดสอบการนำไฟฟ้า | ทดสอบการนำไฟฟ้าของชั้นชุบโดยใช้การทดสอบความต้านทาน |
พารามิเตอร์การควบคุมกระบวนการ | ควบคุมพารามิเตอร์ของกระบวนการ เช่น ส่วนประกอบของน้ำยาชุบ อุณหภูมิ ฯลฯ |
ระบบตรวจสอบตามเวลาจริง | ระบุและแก้ไขความเบี่ยงเบนของกระบวนการแบบเรียลไทม์เพื่อให้ได้ผลลัพธ์ที่สอดคล้องกัน |
ความต้องการน้ำระบายความร้อนในกระบวนการอะโนไดซ์และชุบ
การควบคุมอุณหภูมิเป็นปัจจัยสำคัญในกระบวนการอโนไดซ์และการชุบ สารละลายชุบหรือสารละลายอิเล็กโทรไลต์ที่ใช้ในกระบวนการทั้งสองมีช่วงอุณหภูมิที่ต้องรักษาให้อยู่ในเกณฑ์ที่ยอมรับได้เฉพาะ อุณหภูมิของน้ำยาชุบหรือน้ำยาอิเล็กโทรไลต์มีผลต่ออัตราการชุบ ความหนา คุณภาพ และคุณสมบัติของชั้นชุบ ตัวอย่างเช่น หากอุณหภูมิสูงเกินไป ชั้นที่ชุบอาจมีรูพรุน เปราะ หรือมีแรงยึดเกาะต่ำ ในทางกลับกัน หากอุณหภูมิต่ำเกินไป อัตราการชุบอาจช้าเกินไป ซึ่งอาจนำไปสู่การสะสมที่ไม่สม่ำเสมอหรือคุณสมบัติที่ไม่สอดคล้องกัน เพื่อรักษาช่วงอุณหภูมิที่เหมาะสม โดยทั่วไปจะใช้ระบบควบคุมอุณหภูมิ เช่น เครื่องทำความเย็นหรือเครื่องทำความร้อน เพื่อควบคุมอุณหภูมิของสารละลายชุบหรืออิเล็กโทรไลต์ อุณหภูมิของน้ำหล่อเย็นที่ใช้ในระบบควบคุมอุณหภูมิก็มีความสำคัญเช่นกัน และต้องควบคุมอย่างระมัดระวังเพื่อให้แน่ใจว่าอุณหภูมิของน้ำยาชุบหรืออิเล็กโทรไลต์จะอยู่ในช่วงที่ต้องการ ในหัวข้อถัดไป เราจะหารือเกี่ยวกับข้อกำหนดของน้ำหล่อเย็นและบทบาทของเครื่องทำความเย็นในกระบวนการอโนไดซ์และการชุบ
การประยุกต์ใช้เครื่องทำความเย็นในกระบวนการอะโนไดซ์และชุบ
ชิลเลอร์มีบทบาทสำคัญในการรักษาช่วงอุณหภูมิที่เหมาะสมในกระบวนการอะโนไดซ์และชุบ ชิลเลอร์มักใช้ในการทำให้เย็นลงในสารละลายชุบหรืออิเล็กโทรไลต์เพื่อรักษาช่วงอุณหภูมิที่เหมาะสมสำหรับผลลัพธ์การชุบที่สอดคล้องกัน Chillers ลบความร้อนส่วนเกินที่เกิดจากกระบวนการ anodizing & plating และรักษาอุณหภูมิภายในช่วงที่ต้องการ ความสามารถในการระบายความร้อนของเครื่องทำความเย็นจะต้องจับคู่กับข้อกำหนดเฉพาะของกระบวนการอะโนไดซ์และชุบเพื่อให้แน่ใจว่าการควบคุมอุณหภูมิที่เหมาะสม อาจใช้เครื่องทำความเย็นประเภทต่าง ๆ เช่นเครื่องทำความเย็นที่ระบายความร้อนด้วยอากาศหรือระบายความร้อนด้วยน้ำขึ้นอยู่กับข้อกำหนดการใช้งานและกระบวนการ เครื่องทำความเย็นยังสามารถให้ประโยชน์เพิ่มเติมเช่นประสิทธิภาพการใช้พลังงานที่เพิ่มขึ้นการใช้น้ำลดลงและอายุการใช้งานที่ดีขึ้น นอกเหนือจากการให้การควบคุมอุณหภูมิแล้ว Chillers ยังสามารถเสนอคุณสมบัติอื่น ๆ เช่นการตรวจสอบอัตราการไหลและการควบคุมอุณหภูมิอัตโนมัติเพื่อช่วยรักษาสภาพกระบวนการที่ดีที่สุด การประยุกต์ใช้ที่เหมาะสมของเครื่องทำความเย็นสามารถช่วยให้แน่ใจว่าผลลัพธ์ที่มีคุณภาพและคุณภาพสูงในกระบวนการอะโนไดซ์และชุบ
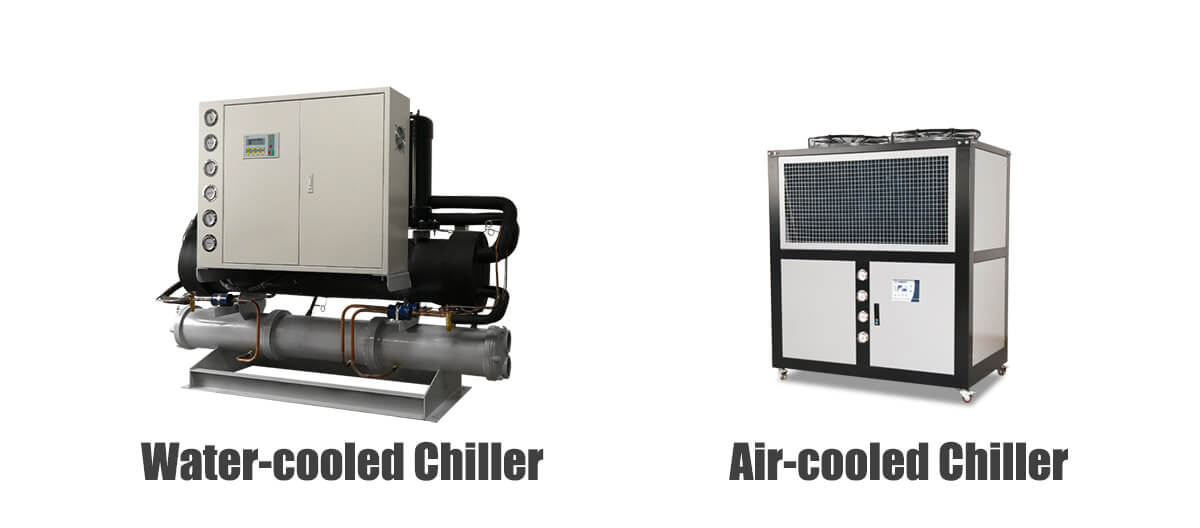
ประเด็นสำคัญสำหรับการเลือกและการกำหนดค่า Chiller
- ความสามารถในการทำความเย็น: ความสามารถในการระบายความร้อนของเครื่องทำความเย็นควรตรงกับข้อกำหนดเฉพาะของกระบวนการอะโนไดซ์และชุบเพื่อให้แน่ใจว่าการควบคุมอุณหภูมิที่เหมาะสม ความสามารถในการระบายความร้อนของเครื่องทำความเย็นมักจะวัดเป็นตันหรือกิโลวัตต์และควรเลือกตามภาระความร้อนของกระบวนการ หากคุณมีข้อมูลเช่นความแตกต่างของอุณหภูมิของน้ำในและออกและอัตราการไหลของการแก้ปัญหาโปรดดูที่ของเรา เครื่องคำนวณขนาดเครื่องทำความเย็น.
- ประเภทของเครื่องทำความเย็น: ควรเลือกประเภทของเครื่องทำความเย็น เช่น ระบายความร้อนด้วยอากาศหรือระบายความร้อนด้วยน้ำ ตามข้อกำหนดการใช้งานและกระบวนการเฉพาะ ชิลเลอร์ระบายความร้อนด้วยน้ำ โดยทั่วไปจะมีประสิทธิภาพมากกว่าและสามารถให้ความเย็นได้สูงกว่า แต่ต้องมีการเข้าถึงหอทำความเย็นและใช้น้ำมากขึ้น ชิลเลอร์ระบายความร้อนด้วยอากาศในทางกลับกัน ติดตั้งและบำรุงรักษาง่ายกว่า แต่มีความสามารถในการระบายความร้อนต่ำกว่าและต้องการพื้นที่มากขึ้นในการระบายความร้อนทิ้ง
- ช่วงการควบคุมอุณหภูมิ: เครื่องทำความเย็นควรสามารถรักษาอุณหภูมิของสารละลายการชุบหรืออิเล็กโทรไลต์ภายในช่วงเฉพาะ โดยทั่วไปช่วงจะถูกกำหนดโดยข้อกำหนดเฉพาะของกระบวนการ anodizing & plating และควรเลือกเครื่องทำความเย็นตามความสามารถในการรักษาช่วงอุณหภูมิที่ต้องการ
- อัตราการไหลและความดัน: อัตราการไหลและแรงดันของน้ำหล่อเย็นควรสอดคล้องกับข้อกำหนดของเครื่องทำความเย็น อัตราการไหลและแรงดันอาจส่งผลต่อประสิทธิภาพและประสิทธิภาพของเครื่องทำความเย็น ดังนั้นจึงเป็นเรื่องสำคัญที่จะต้องแน่ใจว่าระบบน้ำหล่อเย็นได้รับการออกแบบและกำหนดค่าอย่างเหมาะสม
- ประสิทธิภาพการใช้พลังงาน: ประสิทธิภาพการใช้พลังงานของเครื่องทำความเย็นควรได้รับการพิจารณาเพื่อลดต้นทุนการดำเนินงานและลดผลกระทบต่อสิ่งแวดล้อม เครื่องทำความเย็นแบบประหยัดพลังงานสามารถช่วยลดต้นทุนด้านพลังงานและลดการปล่อยก๊าซเรือนกระจก
- การบำรุงรักษาและบริการ: เครื่องทำความเย็นควรบำรุงรักษาและซ่อมบำรุงง่ายเพื่อลดเวลาหยุดทำงานและรับประกันการทำงานที่เชื่อถือได้ การบำรุงรักษาเป็นประจำ เช่น การทำความสะอาดตัวแลกเปลี่ยนความร้อนและการเปลี่ยนตัวกรอง สามารถช่วยรักษาประสิทธิภาพของเครื่องทำความเย็นและยืดอายุการใช้งานได้
เมื่อพิจารณาถึงประเด็นสำคัญเหล่านี้จึงเป็นไปได้ที่จะเลือกและกำหนดค่าเครื่องทำความเย็นที่ตรงตามข้อกำหนดเฉพาะของกระบวนการอะโนไดซ์และชุบและให้การควบคุมอุณหภูมิที่เชื่อถือได้มีประสิทธิภาพและประหยัดต้นทุน
การแก้ไขปัญหา Chiller
การบำรุงรักษาและการทำงานที่เหมาะสมของเครื่องทำความเย็นเป็นสิ่งสำคัญสำหรับการควบคุมอุณหภูมิที่เชื่อถือได้และสม่ำเสมอในกระบวนการอะโนไดซ์และชุบ อย่างไรก็ตามหากมีปัญหาเกิดขึ้นสิ่งสำคัญคือต้องสามารถแก้ไขปัญหาและระบุสาเหตุของปัญหาได้ ปัญหาทั่วไปเกี่ยวกับเครื่องทำความเย็นอาจรวมถึงระดับสารทำความเย็นต่ำตัวกรองอุดตันหรือส่วนประกอบที่ล้มเหลวเช่นคอมเพรสเซอร์หรือเครื่องแลกเปลี่ยนความร้อน ในบางกรณีปัญหาอาจเกี่ยวข้องกับระบบน้ำเย็นแทนที่จะเป็นตัวทำความเย็นเช่นปัญหาเกี่ยวกับการไหลของน้ำหรือความดัน การแก้ไขปัญหาสามารถเกี่ยวข้องกับวิธีการต่าง ๆ เช่นการตรวจสอบด้วยสายตาการวัดอุณหภูมิและแรงกดดันหรือการใช้เครื่องมือวินิจฉัยเช่นการวิเคราะห์การสั่นสะเทือน ด้วยการระบุและจัดการกับสาเหตุของปัญหาเป็นไปได้ที่จะลดเวลาหยุดทำงานและตรวจสอบให้แน่ใจว่ากระบวนการอะโนไดซ์และการชุบสามารถดำเนินการต่อไปในระดับประสิทธิภาพที่ดีที่สุด การบำรุงรักษาและการตรวจสอบอย่างสม่ำเสมอยังสามารถช่วยป้องกันปัญหาที่เกิดขึ้นและตรวจสอบให้แน่ใจว่าเครื่องทำความเย็นและระบบน้ำเย็นนั้นทำงานได้อย่างน่าเชื่อถือและมีประสิทธิภาพ สำหรับข้อมูลการแก้ไขปัญหารายละเอียดเพิ่มเติมโปรดดูที่ รายการตรวจสอบความล้มเหลวของระบบทำความเย็น 10 อันดับแรก.
เทคโนโลยีที่เป็นนวัตกรรมในกระบวนการอะโนไดซ์และชุบ
ความก้าวหน้าทางเทคโนโลยีได้นำไปสู่การพัฒนาวิธีการใหม่และนวัตกรรมสำหรับกระบวนการอะโนไดซ์และชุบ เทคโนโลยีเหล่านี้สามารถให้ประโยชน์เช่นประสิทธิภาพที่ดีขึ้นลดผลกระทบต่อสิ่งแวดล้อมและประสิทธิภาพที่เพิ่มขึ้น
ตัวอย่างเช่น การชุบแบบพัลส์เป็นเทคนิคที่ใช้กระแสไม่ต่อเนื่องเพื่อสะสมไอออนของโลหะลงบนพื้นผิว ส่งผลให้การยึดเกาะและความสม่ำเสมอดีขึ้น
อีกตัวอย่างหนึ่งคือการใช้การชุบแบบไม่ใช้ไฟฟ้า ซึ่งเกี่ยวข้องกับการทับถมของชั้นโลหะลงบนพื้นผิวโดยไม่ต้องใช้แหล่งพลังงานภายนอก เทคนิคนี้สามารถปรับปรุงคุณสมบัติต่างๆ เช่น ความต้านทานการกัดกร่อนและความแข็ง
นอกจากนี้ยังมีการสำรวจวิธีการที่ใช้นาโนเทคโนโลยีหลายวิธีเช่นการใช้การเคลือบนาโนโครงสร้างหรือการปรับเปลี่ยนพื้นผิวกำลังถูกสำรวจสำหรับกระบวนการอะโนไดซ์และชุบเพื่อเพิ่มประสิทธิภาพและความทนทานของพื้นผิวที่ชุบ เทคโนโลยีที่เป็นนวัตกรรมเหล่านี้มีศักยภาพในการปฏิวัติอุตสาหกรรมกระบวนการอะโนไดซ์และชุบและเสนอความเป็นไปได้ใหม่ ๆ สำหรับการรักษาพื้นผิวขั้นสูง
บทสรุป
กระบวนการอะโนไดซ์และการชุบมีบทบาทสำคัญในการใช้งานอุตสาหกรรมจำนวนมากโดยการให้คุณสมบัติพื้นผิวที่เพิ่มขึ้นเช่นความต้านทานการกัดกร่อนความต้านทานการสึกหรอและความสวยงามที่ดีขึ้น กระบวนการนี้ใช้กันอย่างแพร่หลายในอุตสาหกรรมต่าง ๆ เช่นยานยนต์การบินและอวกาศอิเล็กทรอนิกส์และอุปกรณ์การแพทย์ ความต้องการสูงสำหรับกระบวนการเหล่านี้นำไปสู่การพัฒนาเทคโนโลยีใหม่และแนวทางในการปรับปรุงประสิทธิภาพประสิทธิภาพและความยั่งยืน การใช้เครื่องทำความเย็นและระบบควบคุมอุณหภูมิเป็นสิ่งสำคัญสำหรับการรักษาช่วงอุณหภูมิที่เหมาะสมและทำให้มั่นใจได้ว่าผลลัพธ์การชุบที่สอดคล้องและเชื่อถือได้ เทคโนโลยีขั้นสูงเช่นการชุบพัลส์การชุบด้วยไฟฟ้าและวิธีการที่ใช้นาโนเทคโนโลยีนำเสนอความเป็นไปได้ที่น่าตื่นเต้นสำหรับอนาคตของกระบวนการอะโนไดซ์และชุบ ในขณะที่การใช้งานอุตสาหกรรมยังคงเติบโตและมีวิวัฒนาการความต้องการกระบวนการอะโนไดซ์และชุบคาดว่าจะเพิ่มขึ้นเพิ่มความก้าวหน้าทางเทคโนโลยีและแนวทางใหม่ในการรักษาพื้นผิว
สถานะและบทบาทของเครื่องทำความเย็นในกระบวนการอะโนไดซ์และชุบ
ชิลเลอร์มีบทบาทสำคัญในอุตสาหกรรมกระบวนการอะโนไดซ์และชุบโดยให้การควบคุมอุณหภูมิที่เชื่อถือได้และมีประสิทธิภาพสำหรับการแก้ปัญหาการชุบและสารละลายอิเล็กโทรไลต์ การใช้เครื่องทำความเย็นนั้นแพร่หลายและจำเป็นสำหรับการสร้างผลลัพธ์การชุบที่สอดคล้องกันและรักษาคุณภาพของผลิตภัณฑ์ที่สูง นอกจากนี้ชิลเลอร์ยังให้ประโยชน์เช่นการปรับปรุงประสิทธิภาพการใช้พลังงานการใช้น้ำลดลงและอายุการใช้งานที่ยาวนานขึ้น เนื่องจากเทคโนโลยีการชุบและการบำบัดพื้นผิวใหม่ยังคงปรากฏขึ้นบทบาทของเครื่องทำความเย็นจึงคาดว่าจะมีความสำคัญยิ่งขึ้นในการรับรองสภาพกระบวนการและประสิทธิภาพที่ดีที่สุด เป็นผลให้อุตสาหกรรมกระบวนการอะโนไดซ์และชุบมีแนวโน้มที่จะพึ่งพาเครื่องทำความเย็นและระบบควบคุมอุณหภูมิอื่น ๆ สำหรับอนาคตที่คาดการณ์ได้
ผู้จัดหาเครื่องทำความเย็นแบบอะโนไดซ์และชุบมืออาชีพ
หากคุณต้องการเครื่องทำความเย็นที่เชื่อถือได้และมีประสิทธิภาพสำหรับกระบวนการอะโนไดซ์และชุบของคุณอย่ามองหาอะไรอีกต่อไป เครื่องทำความเย็นของเราได้รับการออกแบบมาเพื่อให้การควบคุมอุณหภูมิที่แม่นยำสำหรับการใช้งานอุตสาหกรรมที่หลากหลายรวมถึงกระบวนการชุบและการบำบัดพื้นผิว เรานำเสนอหลากหลายประเภทของเครื่องทำความเย็นเช่นเครื่องทำความเย็นที่ระบายความร้อนด้วยอากาศและน้ำเย็นเพื่อตอบสนองความต้องการและข้อกำหนดเฉพาะของคุณ ชิลเลอร์ของเราประหยัดพลังงานใช้งานง่ายและต้องการการบำรุงรักษาน้อยที่สุดเพื่อให้มั่นใจว่ากระบวนการอะโนไดซ์และการชุบของคุณทำงานได้อย่างราบรื่นและมีประสิทธิภาพ ติดต่อเรา วันนี้เพื่อเรียนรู้เพิ่มเติมเกี่ยวกับโซลูชันชิลเลอร์ของเราและวิธีที่เราสามารถช่วยเพิ่มประสิทธิภาพกระบวนการอะโนไดซ์และชุบของคุณ