Anodizing&Plating Processes are two widely used surface treatment methods in industrial production, aimed at improving the performance, durability, and aesthetic appeal of metal and plastic components. Anodizing is an electrochemical process that creates a thick, protective oxide layer on the surface of a metal substrate, through the controlled oxidation of the material. This oxide layer not only enhances the metal’s resistance to corrosion, wear and tear, and temperature but can also serve as a base for coloring or printing.
Por outro lado, o revestimento é um processo que envolve a deposição de uma fina camada de metal na superfície de um substrato usando métodos de galvanoplastia ou galvanoplastia. O revestimento é geralmente usado para melhorar a dureza da superfície, resistência à abrasão e condutividade elétrica de um substrato, mas também pode ser usado para fins decorativos. Os processos de anodização e galvanização exigem controle rigoroso de vários parâmetros para garantir resultados consistentes e de alta qualidade, tornando-os uma parte importante de várias indústrias, incluindo automotiva, aeroespacial, eletrônica e construção.
Embora ambos os processos visem melhorar as propriedades da superfície de um substrato, eles diferem em seus mecanismos e aplicações. Nas seções a seguir, descreveremos os princípios, processos e aplicações do processo de galvanização e processo de anodização, incluindo os diferentes tipos de galvanização e anodização, suas respectivas vantagens e desvantagens e os desafios e inovações em cada processo. Também discutiremos a importância da água de resfriamento e o papel dos chillers na garantia da qualidade e eficiência dos processos de galvanização e anodização.
Processo de anodização
O processo de anodização cria uma camada espessa e protetora de óxido na superfície de um substrato de metal. O processo envolve a imersão do substrato metálico em uma solução eletrolítica, que normalmente é um ácido, e a passagem de uma corrente elétrica por ele. Como resultado, os íons de oxigênio na solução eletrolítica são atraídos para a superfície do substrato de metal e se combinam com os átomos de metal para formar uma camada densa e estável de óxido de alumínio. Essa camada de óxido fornece uma excelente barreira contra corrosão, desgaste e fatores ambientais. O processo de anodização pode ser realizado em diferentes tipos, incluindo anodização com ácido sulfúrico, anodização com ácido crômico e anodização dura, dependendo das propriedades desejadas da camada de óxido. O processo de anodização é um processo seguro e ecológico que não altera a composição do metal, tornando-o adequado para uma ampla gama de aplicações, incluindo as indústrias aeroespacial, automotiva e de construção.
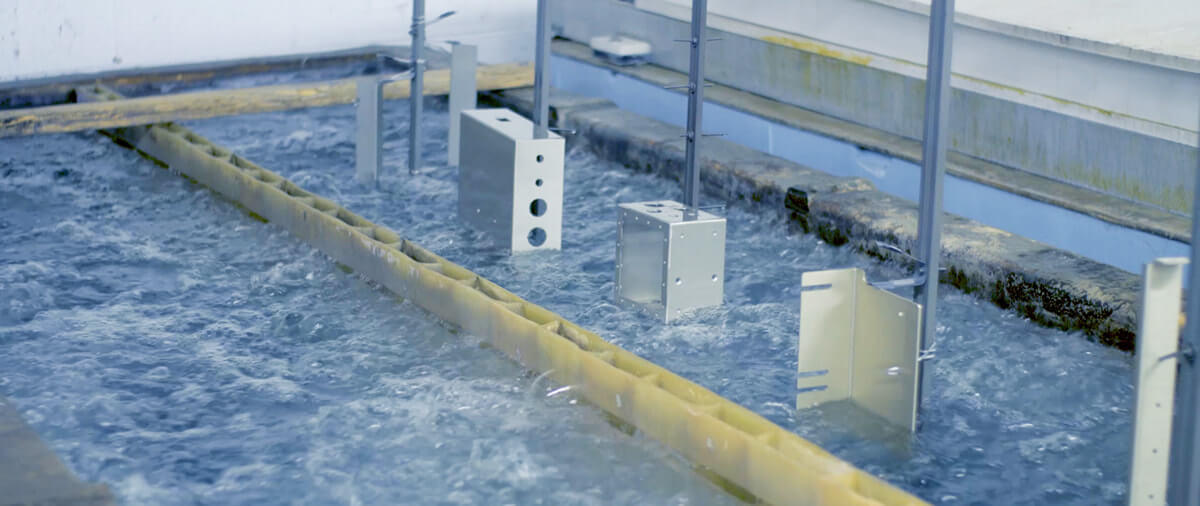
Tipos de processo de anodização
O processo de anodização é um método de tratamento de superfície versátil que pode ser classificado em diferentes tipos com base na solução eletrolítica utilizada e nas propriedades desejadas da camada de óxido.
- Anodização com ácido sulfúrico é o tipo mais comum de processo de anodização e resulta em uma camada de óxido densa e dura, altamente resistente à corrosão, desgaste e fatores ambientais. Este tipo de anodização pode ser posteriormente tingido ou pintado para obter diferentes cores e efeitos estéticos.
- Anodização com ácido crômico, por outro lado, resulta em uma camada de óxido mais fina e flexível que possui boa adesão ao substrato e é ideal para aplicações aeroespaciais e elétricas.
- anodização dura é um tipo de anodização com ácido sulfúrico que envolve tensões e temperaturas mais altas, resultando em uma camada de óxido espessa e resistente ao desgaste, adequada para aplicações de alta tensão, como hastes de pistão e cilindros hidráulicos.
O processo de anodização tem uma ampla gama de aplicações em vários setores, incluindo aeroespacial, automotivo, eletrônico e de construção. Peças anodizadas são comumente usadas em estruturas de aeronaves, carrocerias de automóveis, caixas eletrônicas e acabamentos arquitetônicos. Os benefícios do processo de anodização incluem maior resistência à corrosão, resistência ao desgaste e apelo estético, tornando-o um método de tratamento de superfície popular e econômico para vários substratos.
Prós e contras do processo de anodização
O processo de anodização é um método de tratamento de superfície amplamente utilizado que oferece vários benefícios, mas também apresenta algumas limitações.
As vantagens do processo de anodização incluem a criação de uma camada superficial dura, durável e resistente à corrosão que melhora as propriedades funcionais e estéticas de um substrato. A anodização também é um processo seguro e ecológico que não altera a composição do metal. Além disso, o processo de anodização pode ser realizado em diferentes tipos, proporcionando flexibilidade na obtenção de várias cores, acabamentos e propriedades.
No entanto, também existem algumas limitações no processo de anodização. Por exemplo, a espessura da camada de óxido é limitada e pode afetar as propriedades mecânicas do substrato. O processo de anodização também requer um controle rigoroso de vários parâmetros do processo, o que pode aumentar o custo e o tempo necessários para a produção. Além disso, alguns tipos de anodização, como a anodização com ácido crômico, podem ser prejudiciais à saúde e ao meio ambiente. Apesar dessas limitações, o processo de anodização continua sendo um método de tratamento de superfície popular e econômico para várias aplicações.
Profissionais | Contras |
Camada superficial dura, durável e resistente à corrosão | A espessura limitada da camada de óxido pode afetar as propriedades mecânicas |
Processo seguro e ecológico | Requer controle rigoroso de vários parâmetros do processo, aumentando custo e tempo |
Oferece flexibilidade na obtenção de várias cores, acabamentos e propriedades | Alguns tipos de anodização podem ser prejudiciais à saúde e ao meio ambiente |
Métodos de Inspeção de Qualidade de Anodização
Para garantir resultados consistentes e de alta qualidade no processo de anodização, vários métodos de inspeção e controle de qualidade são usados. Um dos métodos mais comuns é medir a espessura e a porosidade da camada de óxido usando técnicas de teste não destrutivas, como teste de corrente parasita, fluorescência de raios X ou indução magnética. A aparência da superfície, cor e brilho das peças anodizadas podem ser inspecionados visualmente ou usando colorímetros e medidores de brilho. Outros métodos de controle de qualidade incluem testes de resistência à corrosão, resistência ao desgaste e resistência à adesão da camada anodizada usando testes de névoa salina, testes de arranhões e testes de descamação. Para manter a qualidade e a consistência do processo de anodização, é crucial controlar vários parâmetros do processo, incluindo a concentração e o valor do pH da solução eletrolítica, a temperatura e a densidade da corrente e a taxa de agitação. Os sistemas de monitoramento e feedback em tempo real podem ajudar a identificar e corrigir desvios do processo, garantindo que os produtos finais atendam às especificações desejadas e aos requisitos de desempenho.
Método | Propósito |
Técnicas de testes não destrutivos | Meça a espessura e a porosidade da camada de óxido usando correntes parasitas, XRF ou MI |
Inspeção visual e instrumentos | Inspecione a aparência, cor e brilho da superfície usando inspeção visual ou instrumentos |
Teste de resistência à corrosão | Teste a resistência à corrosão da camada anodizada usando testes de névoa salina |
Teste de resistência ao desgaste | Teste a resistência ao desgaste da camada anodizada usando o teste de arranhões |
Teste de força de adesão | Teste a força de adesão da camada anodizada usando o teste de descascamento |
Parâmetros de controle de processo | Controle os parâmetros do processo, como concentração da solução eletrolítica, temperatura, etc. |
Sistemas de monitoramento em tempo real | Identifique e corrija desvios de processo em tempo real para garantir resultados consistentes |
Processo de chapeamento
O processo de galvanização é um método de tratamento de superfície que envolve a deposição de uma fina camada de metal em uma superfície de substrato usando um processo de galvanoplastia ou galvanoplastia. A galvanoplastia é um processo que envolve a passagem de uma corrente elétrica através de uma solução eletrolítica contendo íons metálicos, que são então atraídos para o substrato e depositados em sua superfície. O revestimento sem eletrodos, por outro lado, envolve uma reação química de redução que deposita íons metálicos na superfície do substrato sem a necessidade de uma corrente elétrica externa. O processo de revestimento pode ser realizado em uma variedade de substratos, incluindo metais, plásticos e cerâmicas, para melhorar suas propriedades de superfície, como resistência ao desgaste, resistência à corrosão e condutividade elétrica. A espessura, a adesão e as propriedades da camada revestida podem ser controladas ajustando vários parâmetros do processo, como a composição e o valor de pH da solução de revestimento, a temperatura e a taxa de agitação e a densidade da corrente. Nas seções a seguir, discutiremos os diferentes tipos de processos de revestimento, suas vantagens e desvantagens e suas aplicações em vários setores. Também discutiremos a importância da água de resfriamento e o papel dos chillers no processo de galvanização.
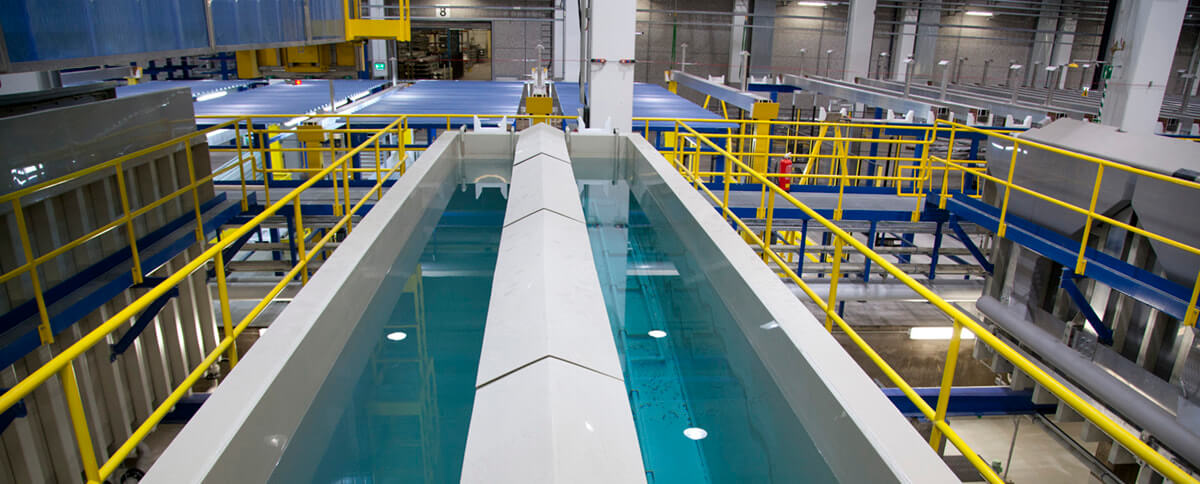
Tipos de processo de chapeamento
O processo de revestimento pode ser classificado em vários tipos com base no tipo de metal usado na solução de revestimento, no material do substrato e nas propriedades da camada revestida. Alguns dos tipos mais comuns de processo de revestimento incluem revestimento de níquel químico, revestimento de ouro, revestimento de prata e revestimento de cobre.
- O revestimento de níquel químico é um tipo de processo de revestimento amplamente utilizado que oferece excelente resistência ao desgaste, resistência à corrosão e propriedades de dureza.
- O revestimento de ouro é conhecido por sua excelente condutividade, resistência à corrosão e apelo estético, tornando-o adequado para aplicações eletrônicas e de joias.
- O revestimento de prata é outro tipo popular de processo de galvanização que fornece excelente condutividade e é comumente usado em contatos e conectores elétricos.
- O revestimento de cobre é frequentemente usado como uma subcamada para outros tipos de revestimento para aumentar as propriedades de adesão e resistência à corrosão da camada revestida.
O processo de revestimento tem uma ampla gama de aplicações em vários setores, incluindo aeroespacial, automotivo, eletrônico e médico. Ele pode ser usado para melhorar o desempenho, aparência e durabilidade de um substrato e é frequentemente usado na fabricação de peças, componentes e produtos acabados. Os benefícios do processo de galvanização incluem propriedades aprimoradas, menor custo e respeito ao meio ambiente, tornando-o um método de tratamento de superfície popular e econômico para várias aplicações.
Prós e Contras do Processo de Revestimento
As vantagens do processo de galvanização incluem a capacidade de depositar uma fina camada de metal na superfície do substrato, o que melhora as propriedades da superfície do substrato, como resistência ao desgaste, resistência à corrosão e condutividade elétrica. O processo de revestimento também pode ser realizado em uma variedade de substratos, tornando-o um método de tratamento de superfície versátil. Além disso, o processo de galvanização pode ser realizado em diferentes tipos, proporcionando flexibilidade na obtenção de várias propriedades e acabamentos.
As limitações do processo de galvanização. Por exemplo, o processo requer um controle rigoroso de vários parâmetros do processo, o que pode aumentar o custo e o tempo necessário para a produção. Além disso, alguns tipos de processos de revestimento, como galvanoplastia, requerem uma quantidade substancial de eletricidade e geram águas residuais, que podem ser perigosas para o meio ambiente. Apesar dessas limitações, o processo de galvanização continua sendo um método de tratamento de superfície popular e econômico para várias aplicações.
Profissionais | Contras |
Deposição de uma fina camada de metal sobre uma superfície de substrato | Requer controle rigoroso de vários parâmetros, aumentando o custo e o tempo de produção |
Melhora as propriedades da superfície do substrato | Certos tipos de processo de revestimento geram águas residuais e consomem uma quantidade significativa de eletricidade, o que pode ser prejudicial ao meio ambiente |
Versátil e pode ser executado em uma variedade de substratos | |
Diferentes tipos disponíveis, permitindo várias propriedades e acabamentos |
Métodos de Inspeção de Qualidade de Revestimento
A inspeção e o controle de qualidade são cruciais no processo de galvanização para garantir resultados consistentes e de alta qualidade. Alguns dos métodos de controle de qualidade mais comuns incluem medir a espessura e a força de adesão da camada revestida, inspecionar visualmente a superfície em busca de defeitos e testar a resistência à corrosão, resistência ao desgaste e condutividade elétrica da camada revestida. Esses testes são normalmente realizados usando técnicas não destrutivas, como fluorescência de raios-X e indução magnética. Além de testar, controlar vários parâmetros do processo, como a composição e o valor de pH da solução de revestimento, a temperatura e a taxa de agitação e a densidade de corrente, é importante para manter a qualidade e a consistência da camada revestida. Os sistemas de monitoramento e feedback em tempo real podem ajudar a identificar e corrigir desvios do processo, garantindo que os produtos finais atendam às especificações desejadas e aos requisitos de desempenho. Ao implementar um rigoroso sistema de controle de qualidade, a Plating Process pode produzir produtos de alta qualidade, confiáveis e econômicos para várias aplicações.
Método | Propósito |
Técnicas de testes não destrutivos | Meça a espessura e a força de adesão da camada revestida usando XRF ou indução magnética |
Inspeção visual | Inspecione visualmente a superfície quanto a defeitos |
Teste de resistência à corrosão | Teste a resistência à corrosão da camada revestida usando testes de névoa salina |
Teste de resistência ao desgaste | Teste a resistência ao desgaste da camada revestida usando o teste de arranhões |
Teste de condutividade elétrica | Teste a condutividade elétrica da camada revestida usando testes de resistência |
Parâmetros de controle de processo | Controle os parâmetros do processo, como composição da solução de revestimento, temperatura, etc. |
Sistemas de monitoramento em tempo real | Identifique e corrija desvios de processo em tempo real para garantir resultados consistentes |
Cooling Water Requirements in Anodizing&Plating Process
O controle de temperatura é um fator crítico nos processos de anodização e galvanização. A solução de revestimento ou solução eletrolítica usada em ambos os processos tem uma faixa de temperatura que deve ser mantida dentro de uma tolerância específica. A temperatura da solução de revestimento ou solução de eletrólito afeta a taxa de revestimento, espessura, qualidade e propriedades da camada revestida. Por exemplo, se a temperatura for muito alta, a camada revestida pode se tornar porosa, quebradiça ou ter baixa resistência à adesão. Por outro lado, se a temperatura for muito baixa, a taxa de revestimento pode ser muito lenta, o que pode levar a deposição irregular ou propriedades inconsistentes. Para manter a faixa de temperatura adequada, sistemas de controle de temperatura, como resfriadores ou aquecedores, são comumente usados para regular a temperatura do revestimento ou da solução eletrolítica. A temperatura da água de resfriamento usada no sistema de controle de temperatura também é importante e deve ser cuidadosamente controlada para garantir que a temperatura da solução de revestimento ou eletrólito permaneça dentro da faixa desejada. Nas próximas seções, discutiremos os requisitos de água de resfriamento e o papel dos chillers nos processos de anodização e galvanização.
Application of Chiller in Anodizing&Plating Process
Chillers play a critical role in maintaining the proper temperature range in Anodizing&Plating Process. Chillers are commonly used to cool the plating or electrolyte solution to maintain the proper temperature range for consistent plating results. Chillers remove the excess heat generated by the Anodizing&Plating Process and maintain the temperature within the desired range. The cooling capacity of the chiller must be matched to the specific requirements of the Anodizing&Plating Process to ensure proper temperature control. Different types of chillers, such as air-cooled or water-cooled chillers, may be used depending on the application and process requirements. The chiller can also provide additional benefits, such as increased energy efficiency, reduced water usage, and improved equipment lifespan. In addition to providing temperature control, chillers can also offer other features such as flow rate monitoring and automatic temperature control to help maintain optimal process conditions. The proper application of chillers can help to ensure consistent and high-quality results in Anodizing&Plating Process.
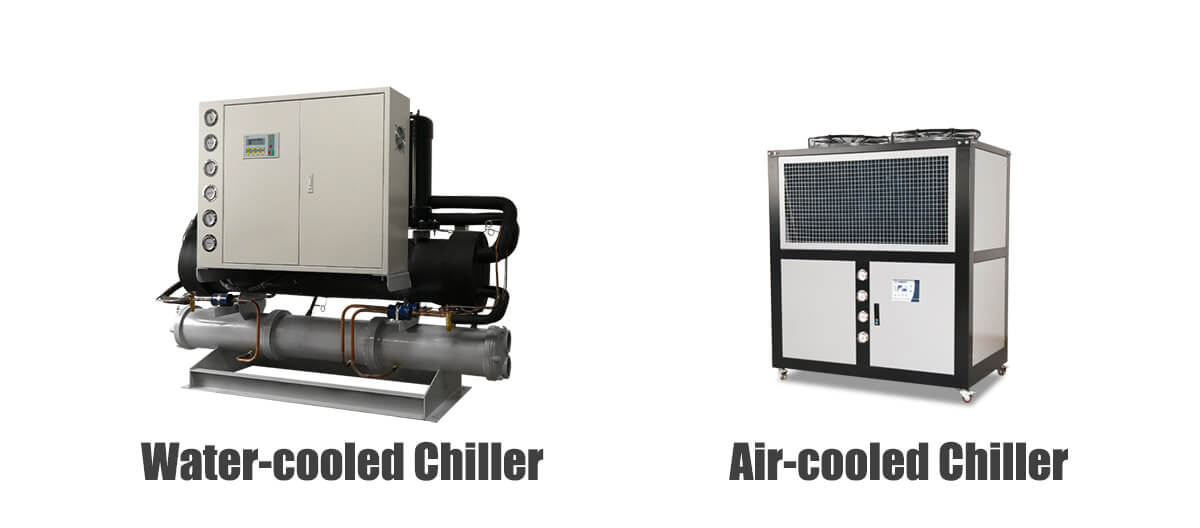
Pontos-chave para seleção e configuração do resfriador
- Capacidade de refrigeração: The cooling capacity of the chiller should be matched to the specific requirements of the Anodizing&Plating Process to ensure proper temperature control. The cooling capacity of the chiller is typically measured in tons or kilowatts and should be selected based on the heat load of the process. If you have data like the temperature difference of in&out water, and the flow rate of the solution, please refer to our calculadora de tamanho do resfriador.
- Tipo de refrigerador: O tipo de resfriador, como resfriado a ar ou resfriado a água, deve ser selecionado com base na aplicação específica e nos requisitos do processo. Chillers refrigerados a água são normalmente mais eficientes e podem fornecer maiores capacidades de resfriamento, mas requerem acesso a uma torre de resfriamento e consomem mais água. Chillers refrigerados a ar, por outro lado, são mais fáceis de instalar e manter, mas têm menor capacidade de resfriamento e requerem mais espaço para liberar o calor residual.
- Faixa de controle de temperatura: The chiller should be able to maintain the temperature of the plating or electrolyte solution within a specific range. The range is typically determined by the specific requirements of the Anodizing&Plating Process, and the chiller should be selected based on its ability to maintain the required temperature range.
- Vazão e pressão: A vazão e a pressão da água de resfriamento devem ser compatíveis com os requisitos do chiller. A vazão e a pressão podem afetar o desempenho e a eficiência do chiller, por isso é importante garantir que o sistema de água de resfriamento seja projetado e configurado adequadamente.
- Eficiência energética: A eficiência energética do chiller deve ser considerada para minimizar os custos operacionais e reduzir o impacto ambiental. Chillers energeticamente eficientes podem ajudar a reduzir os custos de energia e reduzir as emissões de gases de efeito estufa.
- Manutenção e serviço: O chiller deve ser de fácil manutenção e serviço para minimizar o tempo de inatividade e garantir uma operação confiável. A manutenção regular, como a limpeza do trocador de calor e a substituição dos filtros, pode ajudar a manter o desempenho do chiller e prolongar sua vida útil.
By considering these key points, it is possible to select and configure a chiller that meets the specific requirements of Anodizing&Plating Process and provides reliable, efficient, and cost-effective temperature control.
Solução de problemas do resfriador
Proper maintenance and operation of a chiller are crucial for reliable and consistent temperature control in Anodizing&Plating Process. However, if a problem does occur, it is important to be able to troubleshoot the issue and identify the root cause of the problem. Common issues with chillers can include low refrigerant levels, clogged filters, or failed components such as compressors or heat exchangers. In some cases, the problem may be related to the cooling water system rather than the chiller itself, such as issues with water flow or pressure. Troubleshooting can involve various methods such as visual inspection, measuring temperatures and pressures, or using diagnostic tools such as vibration analysis. By identifying and addressing the root cause of the problem, it is possible to minimize downtime and ensure that the Anodizing&Plating Process can continue to operate at optimal performance levels. Regular maintenance and monitoring can also help to prevent issues from occurring and ensure that the chiller and cooling water system are operating reliably and efficiently. For more detailed troubleshooting information, please refer to Lista de verificação das 10 principais falhas do sistema de refrigeração.
Innovative Technologies in Anodizing&Plating Process
Advancements in technology have led to the development of new and innovative approaches for Anodizing&Plating Processes. These technologies can offer benefits such as improved efficiency, reduced environmental impact, and enhanced performance.
Por exemplo, o revestimento por pulso é uma técnica que usa corrente intermitente para depositar íons metálicos em um substrato, resultando em melhor adesão e uniformidade.
Outro exemplo é o uso de galvanoplastia, que envolve a deposição de uma camada de metal sobre um substrato sem a necessidade de uma fonte de energia externa. Essa técnica pode resultar em propriedades aprimoradas, como resistência à corrosão e dureza.
In addition, various nanotechnology-based approaches, such as the use of nanostructured coatings or surface modifications, are being explored for Anodizing&Plating Process to enhance the performance and durability of plated surfaces. These innovative technologies have the potential to revolutionize the Anodizing&Plating Process industry and offer new possibilities for advanced surface treatments.
Conclusão
Anodizing&Plating Process plays a crucial role in many industrial applications by providing enhanced surface properties, such as corrosion resistance, wear resistance, and improved aesthetics. The processes are widely used in various industries such as automotive, aerospace, electronics, and medical devices. The high demand for these processes has led to the development of new technologies and approaches for improving efficiency, performance, and sustainability. The use of chillers and temperature control systems is critical for maintaining the proper temperature range and ensuring consistent and reliable plating results. Advanced technologies such as pulse plating, electroless plating, and nanotechnology-based approaches offer exciting possibilities for the future of Anodizing&Plating Process. As industrial applications continue to grow and evolve, the demand for Anodizing&Plating Process is expected to increase, driving further advancements in technology and new approaches to surface treatments.
Status and Role of Chiller in Anodizing&Plating Process
Chillers play a critical role in the Anodizing&Plating Process industry by providing reliable and efficient temperature control for plating solutions and electrolyte solutions. The use of chillers is widespread and essential for ensuring consistent plating results and maintaining high product quality. In addition, chillers offer benefits such as improved energy efficiency, reduced water usage, and longer equipment lifespan. As new plating and surface treatment technologies continue to emerge, the role of chillers is expected to become even more important in ensuring optimal process conditions and performance. As a result, the Anodizing&Plating Process industry is likely to continue to rely on chillers and other temperature control systems for the foreseeable future.
Professional Anodizing&Plating Process Chiller Supplier
If you’re in need of a reliable and efficient chiller for your Anodizing&Plating Process, look no further than SCY Chiller. Our chillers are designed to provide precise temperature control for a wide range of industrial applications, including plating and surface treatment processes. We offer a variety of chiller types, such as air-cooled and water-cooled chillers, to meet your specific needs and requirements. Our chillers are energy-efficient, easy to operate, and require minimal maintenance, ensuring that your Anodizing&Plating Process runs smoothly and efficiently. Contate-nos today to learn more about our chiller solutions and how we can help optimize your Anodizing&Plating Process.