Máy làm lạnh làm mát không khí được triển khai rộng rãi trong các tòa nhà thương mại, cơ sở công nghiệp và thậm chí các dự án dân cư do lắp đặt và độc lập đơn giản khỏi tài nguyên nước. Không giống như máy làm lạnh nước làm mát, chúng tan nhiệt vào khí quyển thông qua quạt thổi qua các cuộn dây ngưng tụ, tránh sự phức tạp của xử lý nước và tháp giải nhiệt. Tuy nhiên, việc họ tiếp xúc với các điều kiện ngoài trời, chẳng hạn như nhiệt độ khắc nghiệt và tích lũy mảnh vụn, thực hiện các thách thức thiết kế khác biệt.
Thiết kế một máy làm lạnh được làm mát không khí đòi hỏi các yếu tố cân bằng như chọn máy nén phù hợp với thang đo ứng dụng và độ biến thiên tải, chọn chất làm lạnh cân bằng hiệu quả với tác động môi trường, tối ưu hóa thiết bị ngưng tụ và truyền nhiệt bay hơi, thực hiện các biện pháp kiểm soát nâng cao để tiết kiệm năng lượng và giải quyết các mối quan tâm thực tế như không gian. Những cân nhắc này đảm bảo máy làm lạnh đáp ứng nhu cầu dự án trong khi giảm thiểu chi phí hoạt động và dấu chân môi trường.
So sánh máy làm lạnh làm mát không khí và làm mát nước
Khi chọn loại máy làm lạnh, các thiết kế làm mát bằng không khí và làm mát nước khác nhau đáng kể:
- Từ chối nhiệt: Máy làm lạnh làm mát không khí sử dụng quạt và cuộn dây ngưng tụ với không khí xung quanh; Nước làm lạnh làm mát dựa vào tháp làm mát hoặc nguồn nước.
- Cài đặt: Các đơn vị làm mát không khí không yêu cầu đường ống nước, đơn giản hóa thiết lập nhưng cần thêm không gian cho luồng không khí; Các đơn vị làm mát nước cần hệ thống ống nước rộng nhưng có thể nhỏ gọn hơn trong nhà.
- Hiệu quả: Máy làm lạnh nước làm mát xuất sắc ở vùng khí hậu nóng do nước truyền nhiệt vượt trội; Hiệu quả làm mát không khí giảm ở nhiệt độ cao.
- Bảo trì: Máy làm lạnh làm mát không khí có thể cần làm sạch cuộn dây thường xuyên để ngăn ngừa tắc nghẽn; Các đơn vị làm mát nước yêu cầu xử lý nước để tránh mở rộng và ăn mòn, tăng chi phí.
Do đó, các thiết bị làm lạnh không khí phù hợp với các thiết lập không khí hoặc không gian hạn như mái nhà đô thị hoặc vùng khô cằn, trong khi các thiết kế làm mát nước tốt hơn cho các ứng dụng công nghiệp quy mô lớn, hiệu quả.
Thông số thiết kế
Khả năng lam mat
Khả năng làm mát thường được đánh giá trong tấn điện lạnh (TR) hoặc kilowatt (kW), với 1 TR tương đương với 3,517 kW hoặc 12.000 btu/h. Xếp hạng dựa trên các điều kiện tiêu chuẩn:
- Kiến ngưng vào nhiệt độ không khí: 86 ° F (30 ° C)
- Nước ướp lạnh vào nhiệt độ: 54 ° F (12 ° C)
- Nước lạnh để lại nhiệt độ: 44 ° F (7 ° C)
Ví dụ:
- Một máy làm lạnh 397 kW (~ 113 tr) phù hợp với nhu cầu thương mại hoặc công nghiệp cỡ trung bình.
- Công suất phải phù hợp với tải làm mát. Rủi ro không đủ làm mát không đủ và đi xe đạp thường xuyên; Quá khổ giảm hiệu quả và tăng chi phí. Một cách tiếp cận phổ biến là chọn một đơn vị 10-20% trên tải được tính toán để xử lý các biến thể hoặc mở rộng trong tương lai mà không ảnh hưởng đến hiệu quả.
Loại máy nén
Máy nén, lõi làm lạnh, nén khí làm lạnh để truyền nhiệt. Máy làm lạnh làm mát không khí thường sử dụng:
- Máy nén cuộn: Lý tưởng cho các đơn vị nhỏ đến trung bình (lên đến ~ 150 tr). Nhỏ gọn và yên tĩnh (~ 60-65 dB (a)), chúng có hiệu quả dưới tải trọng ổn định với các thiết kế ẩn dật giảm thiểu rò rỉ.
- Máy nén vít: Phù hợp với các hệ thống trung bình đến lớn (150+ TR). Chúng vượt trội với hiệu quả tải một phần và có thể sử dụng VSD để kiểm soát công suất.
- Máy nén ly tâm: Hiếm khi trong các hệ thống làm mát không khí nhưng được sử dụng trong các ứng dụng rất lớn (500+ TR). Hiệu quả khi tải đầy đủ, chúng yêu cầu các điều khiển phức tạp cho hoạt động tải một phần.
Lựa chọn phụ thuộc vào kích thước tải, độ biến thiên (ví dụ: văn phòng so với nhà máy), các ràng buộc tiếng ồn (ví dụ: mái nhà đô thị) và ngân sách.
Lựa chọn chất làm lạnh
Lựa chọn lạnh ảnh hưởng đến hiệu quả, tuân thủ quy định và hiệu suất:
- Chất làm lạnh thông thườngÁp suất dầu bôi trơn cần phải lớn hơn áp suất hút để dầu bôi trơn đi ra khỏi ổ trục.
- R-134a: HFC, không trả lời, GWP ~ 1430.
- R-410A: HFC Blend, Zero ODP, GWP ~ 2088, phổ biến trong các hệ thống nhỏ hơn.
- R-407C: HFC Blend, GWP ~ 1774, thường là sự thay thế R-22.
- Giải pháp thay thế GWP thấpÁp suất dầu bôi trơn cần phải lớn hơn áp suất hút để dầu bôi trơn đi ra khỏi ổ trục.
- R-32: GWP ~ 675, tăng lên do hiệu quả.
- R-454b: GWP <200, designed as a R-410A substitute.
Các quy định như Sửa đổi Kigali nhằm mục đích giảm HFC, yêu cầu các kỹ sư cân bằng hiệu suất, chi phí và tính khả dụng với sự tuân thủ địa phương.
Thiết kế ngưng tụ
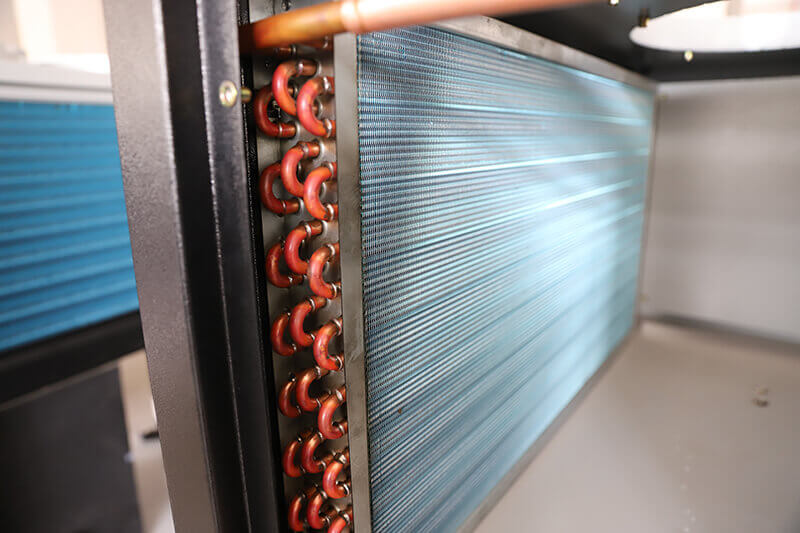
Bộ ngưng tụ, quan trọng cho việc từ chối nhiệt, bao gồm:
- Các tính năng chínhÁp suất dầu bôi trơn cần phải lớn hơn áp suất hút để dầu bôi trơn đi ra khỏi ổ trục.
- Loại vây: Vây bằng đồng bằng đồng là tiêu chuẩn; Mật độ cao hơn cải thiện việc truyền nhiệt nhưng có nguy cơ bị tắc nghẽn.
- Ống: Đồng, cho độ dẫn nhiệt tuyệt vời.
- Sự sắp xếp quạt: Nhiều người hâm mộ đảm bảo dự phòng; Hoạt động giai đoạn phù hợp với tải.
- Động cơ quạt: Xác định tốc độ luồng không khí, giải quyết các thái cực khí hậu địa phương.
Ví dụ:
- Một thiết bị ngưng tụ điển hình có thể có quạt cung cấp luồng không khí ~ 30 m³/s, với không khí ở 30 ° C (86 ° F) và rời khỏi 44 ° C (111 ° F).
Các thiết bị ngưng tụ phải xử lý nhiệt độ môi trường từ mức thấp mùa đông (ví dụ: -10 ° C) đến mức cao mùa hè (ví dụ: +40 ° C), đảm bảo độ tin cậy trong khi giảm thiểu sử dụng năng lượng.
Thiết kế thiết bị bay hơi
Máy bay hơi hấp thụ nhiệt từ nước ướp lạnh hoặc chất lỏng quá trình:
- LoạiÁp suất dầu bôi trơn cần phải lớn hơn áp suất hút để dầu bôi trơn đi ra khỏi ổ trục.
- Vỏ và ống: Mạnh mẽ, phù hợp với hầu hết các ứng dụng.
- Đĩa ăn: Compact, lý tưởng cho các thiết lập giới hạn không gian.
Các tham số chính:
- Tốc độ dòng nước: Khớp với thiết kế hệ thống, ví dụ: ~ 15 kg/s (~ 251 gpm) cho một đơn vị cỡ trung bình.
- Nhiệt độ giảm: Thông thường 6-10 ° C (ví dụ: đầu vào 12 ° C/53 ° F, đầu ra 6 ° C/42 ° F).
Kích thước thích hợp đảm bảo truyền nhiệt hiệu quả trong khi giảm thiểu áp suất giảm trên thiết bị bay hơi.
Hệ thống điều khiển
Máy làm lạnh không khí hiện đại có các điều khiển nâng cao:
- Ổ đĩa tốc độ thay đổi (VSDS): Áp dụng cho máy nén và quạt để điều chỉnh công suất chính xác.
- Điều khiển bộ vi xử lý: Giám sát nhiệt độ/áp suất, điều chỉnh động các điểm đặt.
Những điều này tăng cường hiệu quả tải một phần, hầu hết các ứng dụng chạy ở mức 45-60% phần lớn thời gian trong khi giảm hao mòn trên các thành phần như máy nén và quạt.
Hiệu quả năng lượng
Hiệu quả được đo lường thông qua hệ số hiệu suất (COP) hoặc tỷ lệ hiệu quả năng lượng (EER):
- COP = đầu ra / đầu ra công suất làm mát
- Ví dụ: Làm mát 397 kW, đầu vào 98,9 kW, COP ≈ 4.0.
Higher COP indicates better efficiency; modern systems typically achieve COP >4.0 at full load. Look for high ratings at both full and part-load conditions (e.g., IPLV), as chillers rarely operate at full capacity year-round.
Mức độ tiếng ồn
Máy làm lạnh làm mát không khí tạo ra tiếng ồn đáng kể từ quạt và máy nén:
- Sức mạnh âm thanh điển hình: ~ 70-90 dB (a) ở 30 feet.
Chiến lược giảm thiểu:
- Vị trí đơn vị cách xa các khu vực nhạy cảm.
- Sử dụng vỏ âm thanh hoặc rào cản.
Tiếng ồn là mối quan tâm chính trong môi trường đô thị hoặc dân cư, thường được điều chỉnh bởi các quy định nghiêm ngặt của địa phương.
Kích thước và trọng lượng
Kích thước vật lý ảnh hưởng đến tính khả thi cài đặt:
- Ví dụ: Một đơn vị ~ 100 TR có thể đo 10 x 6 x 7 feet, nặng 5-10 tấn.
Đảm bảo hỗ trợ cấu trúc, đặc biệt là cho các cài đặt trên mái nhà với giới hạn tải.
Yêu cầu điện
Người làm lạnh đòi hỏi sức mạnh đáng kể:
- Điện áp: Thông thường 460V/3 pha cho các đơn vị lớn hơn.
- AMP tải đầy đủ: Thay đổi theo kích thước; Một đơn vị 100 tr có thể vẽ 50-150 A.
Xác minh cơ sở hạ tầng điện hỗ trợ nhu cầu cao nhất, bao gồm các bộ ngắt thích hợp và bảo vệ quá dòng trên mỗi mã địa phương.
Yêu cầu cài đặt
Các cân nhắc cài đặt bao gồm:
- Giải phóng mặt bằng: ~ 3-5 feet xung quanh đơn vị cho luồng khí và bảo trì.
- Gắn cấp độ: Đảm bảo lưu lượng thoát nước/chất làm lạnh thích hợp.
Tài khoản cho khí hậu địa phương; Bảo vệ chống lại thời tiết khắc nghiệt (ví dụ: bao phủ mưa) nếu cần.
Cân nhắc bảo trì
Bảo trì thường xuyên đảm bảo tuổi thọ:
- Cuộn dây ngưng tụ sạch hàng năm; Kiểm tra mức độ lạnh.
Thiết kế các tính năng như lõi có thể tháo rời hoặc bảng điều khiển có thể truy cập đơn giản hóa các tác vụ như thay thế bộ lọc hoặc làm sạch cuộn dây, giảm chi phí thời gian chết.
Phần kết luận
Thiết kế một máy làm lạnh được làm mát không khí liên quan đến việc cân bằng nhiều thông số khả năng làm việc, loại máy nén, lựa chọn chất làm lạnh, thiết kế bộ trao đổi nhiệt để đạt được hoạt động hiệu quả trong các điều kiện. Hiểu các khía cạnh này, bao gồm các hệ thống điều khiển, các số liệu hiệu quả như COP/IPLV, mức độ nhiễu, kích thước, nhu cầu cài đặt và các tính năng bảo trì của các kỹ sư để chỉ định các hệ thống đáp ứng yêu cầu của dự án trong khi giảm thiểu chi phí dài hạn và tác động môi trường.
Cho dù trang bị thêm một cơ sở hiện có hoặc thiết kế một dự án mới, hãy xem xét cẩn thận các yếu tố này đảm bảo hiệu suất và độ bền tối ưu, phù hợp với các mục tiêu bền vững và các yêu cầu quy định như Sửa đổi Kigali.