Anodisierungs- und Beschichtungsverfahren sind zwei weit verbreitete Oberflächenbehandlungsmethoden in der industriellen Produktion, die darauf abzielen, die Leistung, Haltbarkeit und Ästhetik von Metall- und Kunststoffkomponenten zu verbessern. Eloxieren ist ein elektrochemischer Prozess, der durch die kontrollierte Oxidation des Materials eine dicke, schützende Oxidschicht auf der Oberfläche eines Metallsubstrats erzeugt. Diese Oxidschicht erhöht nicht nur die Korrosions-, Verschleiß- und Temperaturbeständigkeit des Metalls, sondern kann auch als Grundlage für Farbgebung oder Bedruckung dienen.
Auf der anderen Seite ist das Plattieren ein Prozess, bei dem eine dünne Metallschicht auf der Oberfläche eines Substrats abgeschieden wird, wobei entweder Galvanisierungs- oder stromlose Plattierungsverfahren verwendet werden. Das Plattieren wird normalerweise verwendet, um die Oberflächenhärte, die Abriebfestigkeit und die elektrische Leitfähigkeit eines Substrats zu verbessern, kann aber auch für dekorative Zwecke verwendet werden. Sowohl Anodisierungs- als auch Beschichtungsprozesse erfordern eine strenge Kontrolle verschiedener Parameter, um qualitativ hochwertige, konsistente Ergebnisse zu gewährleisten, was sie zu einem wichtigen Bestandteil verschiedener Branchen macht, darunter Automobil, Luft- und Raumfahrt, Elektronik und Bauwesen.
Während beide Verfahren darauf abzielen, die Oberflächeneigenschaften eines Substrats zu verbessern, unterscheiden sie sich in ihren Mechanismen und Anwendungen. In den folgenden Abschnitten beschreiben wir die Prinzipien, Prozesse und Anwendungen des Beschichtungsverfahrens und des Anodisierungsverfahrens, einschließlich der verschiedenen Arten des Beschichtens und Anodisierens, ihrer jeweiligen Vor- und Nachteile sowie der Herausforderungen und Innovationen in jedem Verfahren. Wir werden auch die Bedeutung von Kühlwasser und die Rolle von Kühlern bei der Gewährleistung der Qualität und Effizienz von Beschichtungs- und Anodisierungsprozessen erörtern.
Anodisierungsprozess
Der Anodisierungsprozess erzeugt eine dicke, schützende Oxidschicht auf der Oberfläche eines Metallsubstrats. Das Verfahren umfasst das Eintauchen des Metallsubstrats in eine Elektrolytlösung, die typischerweise eine Säure ist, und das Hindurchleiten eines elektrischen Stroms. Dadurch werden Sauerstoffionen in der Elektrolytlösung von der Oberfläche des Metallsubstrats angezogen und verbinden sich mit den Metallatomen zu einer stabilen, dichten Schicht aus Aluminiumoxid. Diese Oxidschicht bietet eine hervorragende Barriere gegen Korrosion, Verschleiß und Umwelteinflüsse. Der Anodisierungsprozess kann auf verschiedene Arten durchgeführt werden, einschließlich Schwefelsäureanodisierung, Chromsäureanodisierung und Hartanodisierung, abhängig von den gewünschten Eigenschaften der Oxidschicht. Das Anodisierungsverfahren ist ein sicheres und umweltfreundliches Verfahren, das die Zusammensetzung des Metalls nicht verändert, wodurch es für eine Vielzahl von Anwendungen geeignet ist, einschließlich der Luft- und Raumfahrt-, Automobil- und Bauindustrie.
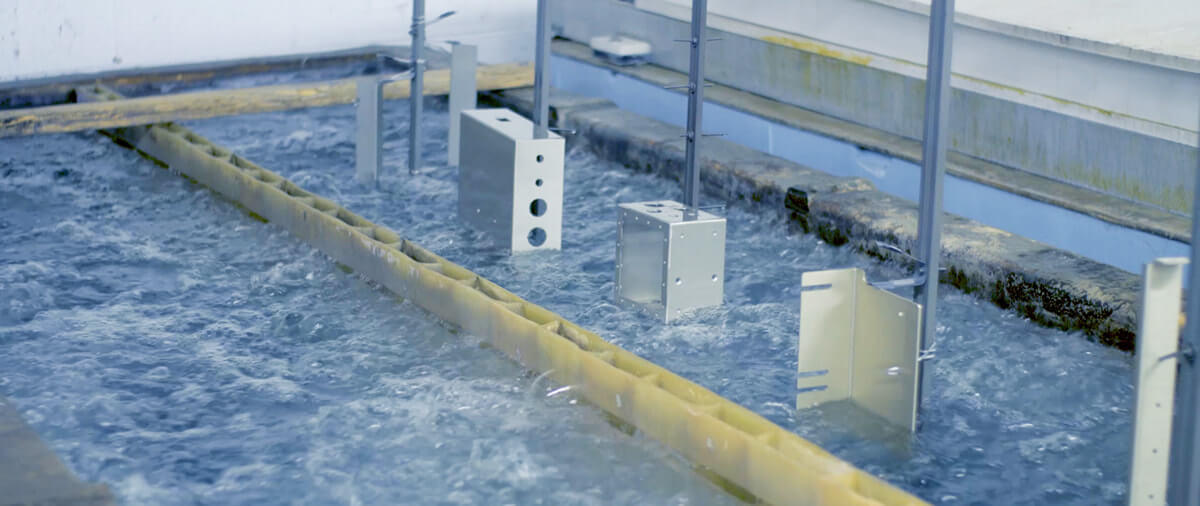
Anodisierungsprozesstypen
Der Anodisierungsprozess ist ein vielseitiges Oberflächenbehandlungsverfahren, das je nach verwendeter Elektrolytlösung und den gewünschten Eigenschaften der Oxidschicht in verschiedene Typen eingeteilt werden kann.
- Eloxieren mit Schwefelsäure ist die häufigste Art des Anodisierungsprozesses und führt zu einer dichten und harten Oxidschicht, die sehr widerstandsfähig gegen Korrosion, Verschleiß und Umwelteinflüsse ist. Diese Art der Eloxierung kann weiter gefärbt oder lackiert werden, um unterschiedliche Farben und ästhetische Effekte zu erzielen.
- Eloxieren mit Chromsäurehingegen führt zu einer dünneren und flexibleren Oxidschicht, die eine gute Haftung auf dem Substrat hat und ideal für Anwendungen in der Luft- und Raumfahrt und in der Elektrotechnik ist.
- Hartanodisierung ist eine Art der Schwefelsäure-Anodisierung, die höhere Spannungen und Temperaturen beinhaltet, was zu einer dicken und verschleißfesten Oxidschicht führt, die für hochbeanspruchte Anwendungen wie Kolbenstangen und Hydraulikzylinder geeignet ist.
Der Anodisierungsprozess hat ein breites Anwendungsspektrum in verschiedenen Branchen, darunter Luft- und Raumfahrt, Automobil, Elektronik und Bauwesen. Eloxierte Teile werden üblicherweise in Flugzeugstrukturen, Automobilkarosserien, Elektronikgehäusen und architektonischen Oberflächen verwendet. Zu den Vorteilen des Anodisierungsverfahrens gehören eine verbesserte Korrosionsbeständigkeit, Verschleißfestigkeit und Ästhetik, was es zu einer beliebten und kostengünstigen Oberflächenbehandlungsmethode für verschiedene Substrate macht.
Vor- und Nachteile des Anodisierungsprozesses
Der Anodisierungsprozess ist eine weit verbreitete Oberflächenbehandlungsmethode, die mehrere Vorteile bietet, aber auch einige Einschränkungen hat.
Zu den Vorteilen des Anodisierungsprozesses gehört die Schaffung einer harten, haltbaren und korrosionsbeständigen Oberflächenschicht, die die funktionellen und ästhetischen Eigenschaften eines Substrats verbessert. Eloxieren ist auch ein sicheres und umweltfreundliches Verfahren, das die Zusammensetzung des Metalls nicht verändert. Darüber hinaus kann der Anodisierungsprozess auf verschiedene Arten durchgeführt werden, was Flexibilität beim Erreichen verschiedener Farben, Oberflächen und Eigenschaften bietet.
Es gibt jedoch auch einige Einschränkungen für den Anodisierungsprozess. Beispielsweise ist die Dicke der Oxidschicht begrenzt und kann die mechanischen Eigenschaften des Substrats beeinflussen. Der Anodisierungsprozess erfordert auch eine strenge Kontrolle verschiedener Prozessparameter, was die für die Produktion erforderlichen Kosten und den Zeitaufwand erhöhen kann. Darüber hinaus können einige Arten des Eloxierens, wie das Chromsäureanodisieren, gesundheits- und umweltschädlich sein. Trotz dieser Einschränkungen bleibt der Anodisierungsprozess eine beliebte und kostengünstige Oberflächenbehandlungsmethode für verschiedene Anwendungen.
Vorteile | Nachteile |
Harte, haltbare und korrosionsbeständige Oberflächenschicht | Eine begrenzte Dicke der Oxidschicht kann die mechanischen Eigenschaften beeinflussen |
Sicheres und umweltfreundliches Verfahren | Erfordert eine strenge Kontrolle verschiedener Prozessparameter, was Kosten und Zeit erhöht |
Bietet Flexibilität beim Erzielen verschiedener Farben, Oberflächen und Eigenschaften | Einige Arten des Eloxierens können gesundheits- und umweltschädlich sein |
Eloxal-Qualitätsprüfmethoden
Um qualitativ hochwertige und konsistente Ergebnisse im Anodisierungsprozess zu gewährleisten, werden verschiedene Qualitätsprüfungs- und Kontrollmethoden eingesetzt. Eine der gebräuchlichsten Methoden besteht darin, die Dicke und Porosität der Oxidschicht mit zerstörungsfreien Prüftechniken wie Wirbelstromprüfung, Röntgenfluoreszenz oder magnetischer Induktion zu messen. Das Aussehen, die Farbe und der Glanz der Oberfläche der eloxierten Teile können visuell oder mit Kolorimetern und Glanzmessgeräten geprüft werden. Andere Qualitätskontrollmethoden umfassen das Testen der Korrosionsbeständigkeit, Verschleißfestigkeit und Haftfestigkeit der anodisierten Schicht durch Salzsprühtest, Kratztest und Schältest. Um die Qualität und Konsistenz des Anodisierungsprozesses aufrechtzuerhalten, ist es entscheidend, verschiedene Prozessparameter zu kontrollieren, einschließlich der Konzentration und des pH-Werts der Elektrolytlösung, der Temperatur und Stromdichte sowie der Rührgeschwindigkeit. Echtzeitüberwachungs- und Feedbacksysteme können dabei helfen, Prozessabweichungen zu identifizieren und zu korrigieren und sicherzustellen, dass die Endprodukte die gewünschten Spezifikationen und Leistungsanforderungen erfüllen.
Methode | Zweck |
Zerstörungsfreie Prüftechniken | Messen Sie die Dicke und Porosität der Oxidschicht mit Wirbelstrom, XRF oder MI |
Sichtprüfung und Instrumente | Überprüfen Sie das Aussehen, die Farbe und den Glanz der Oberfläche durch Sichtprüfung oder Instrumente |
Prüfung der Korrosionsbeständigkeit | Prüfen Sie die Korrosionsbeständigkeit der Eloxalschicht mittels Salzsprühnebeltest |
Prüfung der Verschleißfestigkeit | Testen Sie die Verschleißfestigkeit der Eloxalschicht mittels Kratzprüfung |
Prüfung der Haftfestigkeit | Testen Sie die Haftfestigkeit der Eloxalschicht mittels Schältest |
Prozesssteuerungsparameter | Steuerung von Prozessparametern wie Elektrolytlösungskonzentration, Temperatur usw. |
Echtzeit-Überwachungssysteme | Identifizieren und korrigieren Sie Prozessabweichungen in Echtzeit, um konsistente Ergebnisse zu gewährleisten |
Beschichtungsprozess
Der Plattierungsprozess ist ein Oberflächenbehandlungsverfahren, bei dem eine dünne Metallschicht auf einer Substratoberfläche unter Verwendung eines Elektroplattierungs- oder stromlosen Plattierungsprozesses abgeschieden wird. Galvanisieren ist ein Prozess, bei dem ein elektrischer Strom durch eine Elektrolytlösung geleitet wird, die Metallionen enthält, die dann vom Substrat angezogen und auf seiner Oberfläche abgeschieden werden. Das stromlose Plattieren hingegen beinhaltet eine chemische Reduktionsreaktion, bei der Metallionen auf der Substratoberfläche abgeschieden werden, ohne dass ein externer elektrischer Strom erforderlich ist. Der Beschichtungsprozess kann auf einer Vielzahl von Substraten durchgeführt werden, einschließlich Metallen, Kunststoffen und Keramiken, um deren Oberflächeneigenschaften wie Verschleißfestigkeit, Korrosionsbeständigkeit und elektrische Leitfähigkeit zu verbessern. Die Dicke, Adhäsion und Eigenschaften der plattierten Schicht können durch Einstellen verschiedener Prozessparameter gesteuert werden, wie z. B. der Zusammensetzung und des pH-Werts der Plattierungslösung, der Temperatur und Rührgeschwindigkeit und der Stromdichte. In den folgenden Abschnitten werden wir die verschiedenen Arten von Beschichtungsprozessen, ihre Vor- und Nachteile und ihre Anwendungen in verschiedenen Branchen diskutieren. Wir werden auch die Bedeutung von Kühlwasser und die Rolle von Kühlern im Beschichtungsprozess erörtern.
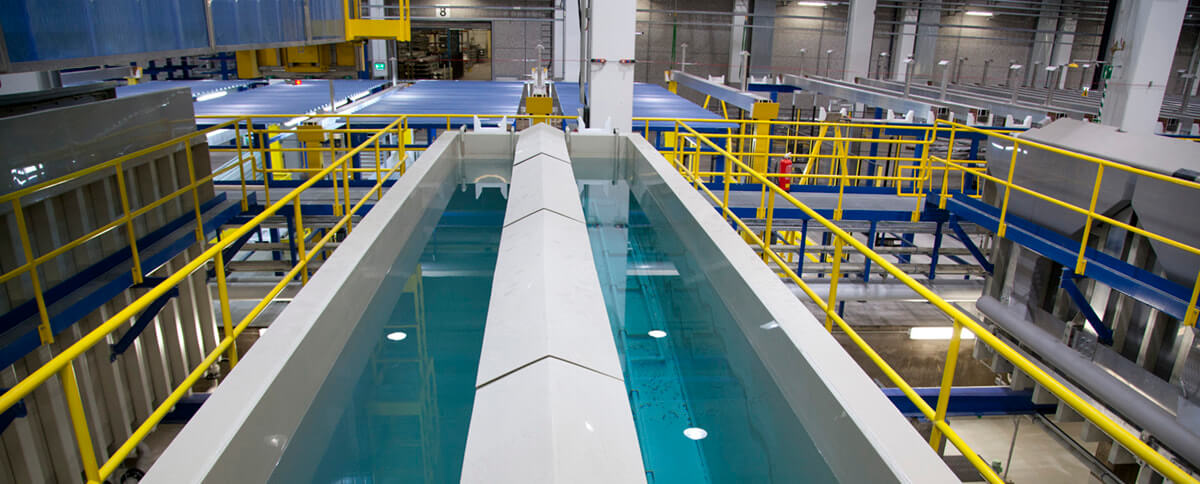
Arten von Beschichtungsverfahren
Der Plattierungsprozess kann basierend auf der Art des in der Plattierungslösung verwendeten Metalls, dem Substratmaterial und den Eigenschaften der plattierten Schicht in verschiedene Typen eingeteilt werden. Einige der gebräuchlichsten Arten von Plattierungsprozessen umfassen stromlose Vernickelung, Vergoldung, Versilberung und Verkupferung.
- Die stromlose Vernickelung ist eine weit verbreitete Art von Beschichtungsverfahren, das eine hervorragende Verschleißfestigkeit, Korrosionsbeständigkeit und Härteeigenschaften bietet.
- Die Vergoldung ist bekannt für ihre hervorragende Leitfähigkeit, Korrosionsbeständigkeit und Ästhetik, wodurch sie sich für Elektronik- und Schmuckanwendungen eignet.
- Die Versilberung ist eine weitere beliebte Art des Beschichtungsverfahrens, das eine hervorragende Leitfähigkeit bietet und häufig in elektrischen Kontakten und Steckverbindern verwendet wird.
- Eine Kupferplattierung wird häufig als Unterschicht für andere Plattierungsarten verwendet, um die Haftungs- und Korrosionsbeständigkeitseigenschaften der plattierten Schicht zu verbessern.
Der Beschichtungsprozess hat ein breites Anwendungsspektrum in verschiedenen Branchen, darunter Luft- und Raumfahrt, Automobil, Elektronik und Medizin. Es kann verwendet werden, um die Leistung, das Erscheinungsbild und die Haltbarkeit eines Substrats zu verbessern, und wird häufig bei der Herstellung von Teilen, Komponenten und Endprodukten verwendet. Zu den Vorteilen des Beschichtungsverfahrens gehören verbesserte Eigenschaften, niedrigere Kosten und Umweltfreundlichkeit, was es zu einer beliebten und kostengünstigen Oberflächenbehandlungsmethode für verschiedene Anwendungen macht.
Vor- und Nachteile des Beschichtungsprozesses
Zu den Vorteilen des Beschichtungsverfahrens gehört die Fähigkeit, eine dünne Metallschicht auf einer Substratoberfläche abzuscheiden, wodurch die Oberflächeneigenschaften des Substrats wie Verschleißfestigkeit, Korrosionsbeständigkeit und elektrische Leitfähigkeit verbessert werden. Der Beschichtungsprozess kann auch auf einer Vielzahl von Substraten durchgeführt werden, was ihn zu einer vielseitigen Oberflächenbehandlungsmethode macht. Darüber hinaus kann der Beschichtungsprozess auf verschiedene Arten durchgeführt werden, was Flexibilität bei der Erzielung verschiedener Eigenschaften und Oberflächen bietet.
Die Einschränkungen des Beschichtungsprozesses. Beispielsweise erfordert das Verfahren eine strenge Kontrolle verschiedener Verfahrensparameter, was die für die Produktion erforderlichen Kosten und Zeit erhöhen kann. Darüber hinaus erfordern einige Arten von Plattierungsprozessen, wie z. B. Elektroplattieren, eine beträchtliche Menge an Elektrizität und erzeugen Abwasser, das für die Umwelt schädlich sein kann. Trotz dieser Einschränkungen bleibt der Beschichtungsprozess eine beliebte und kostengünstige Oberflächenbehandlungsmethode für verschiedene Anwendungen.
Vorteile | Nachteile |
Abscheidung einer dünnen Metallschicht auf einer Substratoberfläche | Erfordert eine strenge Kontrolle verschiedener Parameter, was die Produktionskosten und -zeit erhöht |
Verbessert die Oberflächeneigenschaften des Substrats | Bestimmte Arten von Beschichtungsprozessen erzeugen Abwasser und verbrauchen eine erhebliche Menge an Strom, was umweltschädlich sein kann |
Vielseitig und kann auf einer Vielzahl von Substraten durchgeführt werden | |
Verschiedene Typen erhältlich, die verschiedene Eigenschaften und Oberflächen ermöglichen |
Methoden zur Prüfung der Beschichtungsqualität
Qualitätsprüfung und -kontrolle sind im Galvanisierungsprozess von entscheidender Bedeutung, um qualitativ hochwertige und konsistente Ergebnisse zu gewährleisten. Einige der gebräuchlichsten Qualitätskontrollmethoden umfassen das Messen der Dicke und Haftfestigkeit der plattierten Schicht, das visuelle Untersuchen der Oberfläche auf Defekte und das Testen der Korrosionsbeständigkeit, Verschleißfestigkeit und elektrischen Leitfähigkeit der plattierten Schicht. Diese Tests werden typischerweise mit zerstörungsfreien Techniken wie Röntgenfluoreszenz und magnetischer Induktion durchgeführt. Neben dem Testen ist die Kontrolle verschiedener Prozessparameter wie die Zusammensetzung und der pH-Wert der Galvanisierungslösung, die Temperatur und Rührgeschwindigkeit sowie die Stromdichte wichtig, um die Qualität und Konsistenz der galvanisierten Schicht aufrechtzuerhalten. Echtzeitüberwachungs- und Feedbacksysteme können dabei helfen, Prozessabweichungen zu identifizieren und zu korrigieren und sicherzustellen, dass die Endprodukte die gewünschten Spezifikationen und Leistungsanforderungen erfüllen. Durch die Implementierung eines strengen Qualitätskontrollsystems kann Plating Process qualitativ hochwertige, zuverlässige und kostengünstige Produkte für verschiedene Anwendungen herstellen.
Methode | Zweck |
Zerstörungsfreie Prüftechniken | Messen Sie die Dicke und Haftfestigkeit der plattierten Schicht mit XRF oder magnetischer Induktion |
Visuelle Inspektion | Prüfen Sie die Oberfläche visuell auf Fehler |
Prüfung der Korrosionsbeständigkeit | Testen Sie die Korrosionsbeständigkeit der plattierten Schicht mit einem Salzsprühtest |
Prüfung der Verschleißfestigkeit | Testen Sie die Verschleißfestigkeit der plattierten Schicht mit einem Kratztest |
Prüfung der elektrischen Leitfähigkeit | Testen Sie die elektrische Leitfähigkeit der plattierten Schicht mit einer Widerstandsprüfung |
Prozesssteuerungsparameter | Steuerung von Prozessparametern wie Zusammensetzung der Beschichtungslösung, Temperatur usw. |
Echtzeit-Überwachungssysteme | Identifizieren und korrigieren Sie Prozessabweichungen in Echtzeit, um konsistente Ergebnisse zu gewährleisten |
Kühlwasseranforderungen im Anodisierungs- und Beschichtungsprozess
Die Temperaturregelung ist ein kritischer Faktor sowohl beim Anodisieren als auch beim Galvanisieren. Die in beiden Prozessen verwendete Galvanisierungslösung oder Elektrolytlösung hat einen Temperaturbereich, der innerhalb einer bestimmten Toleranz gehalten werden muss. Die Temperatur der Plattierungslösung oder Elektrolytlösung beeinflusst die Plattierungsrate, Dicke, Qualität und Eigenschaften der plattierten Schicht. Wenn beispielsweise die Temperatur zu hoch ist, kann die plattierte Schicht porös oder spröde werden oder eine schlechte Haftfestigkeit aufweisen. Wenn andererseits die Temperatur zu niedrig ist, kann die Plattierungsgeschwindigkeit zu langsam sein, was zu einer ungleichmäßigen Abscheidung oder inkonsistenten Eigenschaften führen kann. Um den richtigen Temperaturbereich aufrechtzuerhalten, werden üblicherweise Temperaturregelsysteme wie Kühler oder Heizer verwendet, um die Temperatur der Plattierungs- oder Elektrolytlösung zu regulieren. Die im Temperaturregelsystem verwendete Kühlwassertemperatur ist ebenfalls wichtig und muss sorgfältig kontrolliert werden, um sicherzustellen, dass die Temperatur der Plattierungs- oder Elektrolytlösung innerhalb des gewünschten Bereichs bleibt. In den nächsten Abschnitten werden wir die Kühlwasseranforderungen und die Rolle von Kühlern in Anodisierungs- und Beschichtungsprozessen erörtern.
Anwendung des Kühlers im Anodisierungs- und Beschichtungsprozess
Kühler spielen eine entscheidende Rolle bei der Aufrechterhaltung des richtigen Temperaturbereichs im Anodisierungs- und Beschichtungsprozess. Kühler werden üblicherweise zum Kühlen der Plattierungs- oder Elektrolytlösung verwendet, um den richtigen Temperaturbereich für konsistente Plattierungsergebnisse aufrechtzuerhalten. Kühler führen die durch den Anodisierungs- und Beschichtungsprozess erzeugte überschüssige Wärme ab und halten die Temperatur im gewünschten Bereich. Die Kühlleistung des Kühlers muss an die spezifischen Anforderungen des Anodisierungs- und Beschichtungsprozesses angepasst werden, um eine ordnungsgemäße Temperaturregelung zu gewährleisten. Abhängig von der Anwendung und den Prozessanforderungen können unterschiedliche Arten von Kältemaschinen, wie luftgekühlte oder wassergekühlte Kältemaschinen, verwendet werden. Der Kühler kann auch zusätzliche Vorteile bieten, wie z. B. eine erhöhte Energieeffizienz, einen geringeren Wasserverbrauch und eine längere Lebensdauer der Ausrüstung. Zusätzlich zur Temperaturregelung können Kühler auch andere Funktionen bieten, wie z. B. die Überwachung der Durchflussrate und die automatische Temperaturregelung, um zur Aufrechterhaltung optimaler Prozessbedingungen beizutragen. Die richtige Anwendung von Kühlern kann dazu beitragen, konsistente und qualitativ hochwertige Ergebnisse im Anodisierungs- und Beschichtungsprozess zu gewährleisten.
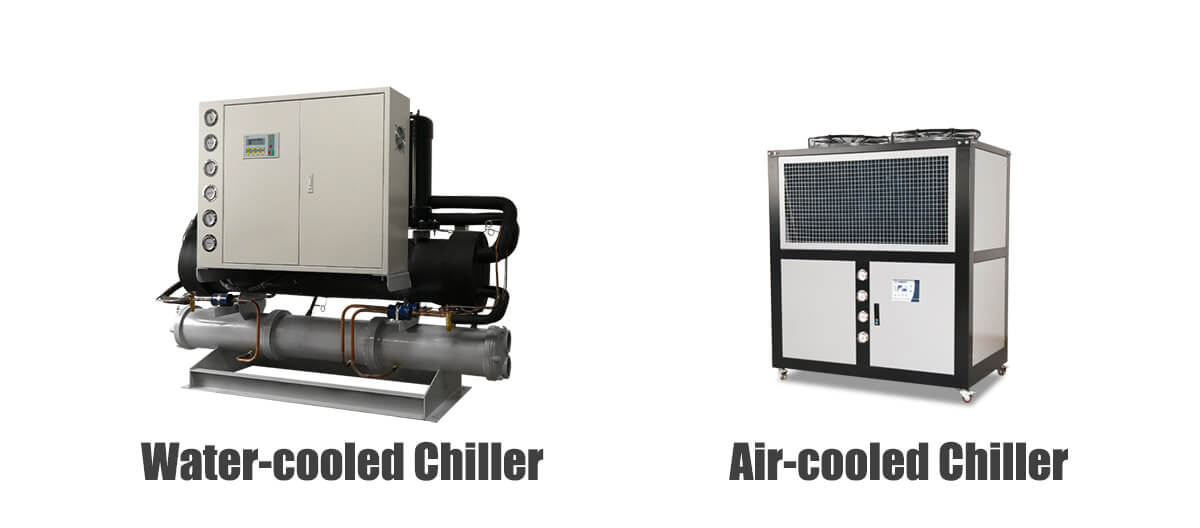
Wichtige Punkte für die Auswahl und Konfiguration des Chillers
- Kühlkapazität: Die Kühlleistung des Kühlers sollte an die spezifischen Anforderungen des Anodisierungs- und Beschichtungsprozesses angepasst werden, um eine ordnungsgemäße Temperaturregelung zu gewährleisten. Die Kühlkapazität des Chillers wird typischerweise in Tonnen oder Kilowatt gemessen und sollte basierend auf der Wärmelast des Prozesses ausgewählt werden. Wenn Sie Daten wie den Temperaturunterschied von ein- und ausgehendem Wasser und die Durchflussrate der Lösung haben, beziehen Sie sich bitte auf unsere Kühlergrößenrechner.
- Art der Kältemaschine: Die Art der Kältemaschine, z. B. luftgekühlt oder wassergekühlt, sollte basierend auf der spezifischen Anwendung und den Prozessanforderungen ausgewählt werden. Wassergekühlte Chiller sind in der Regel effizienter und können höhere Kühlkapazitäten bereitstellen, erfordern jedoch Zugang zu einem Kühlturm und verbrauchen mehr Wasser. Luftgekühlte Kältemaschinen, hingegen sind einfacher zu installieren und zu warten, haben jedoch geringere Kühlleistungen und benötigen mehr Platz, um die Abwärme abzuführen.
- Temperaturregelbereich: Der Kühler sollte in der Lage sein, die Temperatur der Plattierungs- oder Elektrolytlösung innerhalb eines bestimmten Bereichs zu halten. Der Bereich wird in der Regel durch die spezifischen Anforderungen des Anodisierungs- und Beschichtungsprozesses bestimmt, und der Kühler sollte basierend auf seiner Fähigkeit ausgewählt werden, den erforderlichen Temperaturbereich aufrechtzuerhalten.
- Durchfluss und Druck: Die Durchflussrate und der Druck des Kühlwassers sollten mit den Anforderungen der Kältemaschine kompatibel sein. Die Durchflussrate und der Druck können die Leistung und Effizienz des Kühlers beeinflussen, daher ist es wichtig sicherzustellen, dass das Kühlwassersystem richtig ausgelegt und konfiguriert ist.
- Energieeffizienz: Die Energieeffizienz der Kältemaschine sollte berücksichtigt werden, um die Betriebskosten zu minimieren und die Umweltbelastung zu reduzieren. Energieeffiziente Kältemaschinen können helfen, Energiekosten zu senken und Treibhausgasemissionen zu reduzieren.
- Wartung und Service: Die Kältemaschine sollte einfach zu warten und zu warten sein, um Ausfallzeiten zu minimieren und einen zuverlässigen Betrieb zu gewährleisten. Regelmäßige Wartung, wie die Reinigung des Wärmetauschers und der Austausch von Filtern, kann dazu beitragen, die Leistung der Kältemaschine aufrechtzuerhalten und ihre Lebensdauer zu verlängern.
Durch die Berücksichtigung dieser Schlüsselpunkte ist es möglich, einen Kühler auszuwählen und zu konfigurieren, der die spezifischen Anforderungen des Anodisierungs- und Beschichtungsprozesses erfüllt und eine zuverlässige, effiziente und kostengünstige Temperaturregelung bietet.
Fehlerbehebung des Kühlers
Die ordnungsgemäße Wartung und der ordnungsgemäße Betrieb eines Kühlers sind entscheidend für eine zuverlässige und konsistente Temperaturregelung im Anodisierungs- und Beschichtungsprozess. Wenn jedoch ein Problem auftritt, ist es wichtig, das Problem beheben und die Ursache des Problems identifizieren zu können. Häufige Probleme mit Kältemaschinen können niedrige Kältemittelfüllstände, verstopfte Filter oder ausgefallene Komponenten wie Kompressoren oder Wärmetauscher sein. In einigen Fällen kann das Problem eher mit dem Kühlwassersystem als mit dem Kühler selbst zusammenhängen, z. B. Probleme mit dem Wasserfluss oder -druck. Die Fehlersuche kann verschiedene Methoden wie Sichtprüfung, Messen von Temperaturen und Drücken oder die Verwendung von Diagnosewerkzeugen wie Schwingungsanalyse umfassen. Durch das Identifizieren und Beheben der Grundursache des Problems ist es möglich, Ausfallzeiten zu minimieren und sicherzustellen, dass der Anodisierungs- und Beschichtungsprozess weiterhin auf optimalem Leistungsniveau betrieben werden kann. Regelmäßige Wartung und Überwachung können auch dazu beitragen, Probleme zu vermeiden und sicherzustellen, dass die Kältemaschine und das Kühlwassersystem zuverlässig und effizient arbeiten. Ausführlichere Informationen zur Fehlerbehebung finden Sie unter Checkliste der 10 häufigsten Fehler im Kühlsystem.
Innovative Technologien im Anodisierungs- und Beschichtungsprozess
Fortschritte in der Technologie haben zur Entwicklung neuer und innovativer Ansätze für Anodisierungs- und Beschichtungsprozesse geführt. Diese Technologien können Vorteile wie verbesserte Effizienz, geringere Umweltbelastung und verbesserte Leistung bieten.
Impulsplattieren ist beispielsweise eine Technik, die intermittierenden Strom verwendet, um Metallionen auf einem Substrat abzuscheiden, was zu einer verbesserten Haftung und Gleichmäßigkeit führt.
Ein weiteres Beispiel ist die Verwendung von stromlosem Plattieren, bei dem eine Metallschicht auf einem Substrat abgeschieden wird, ohne dass eine externe Stromquelle erforderlich ist. Diese Technik kann zu verbesserten Eigenschaften wie Korrosionsbeständigkeit und Härte führen.
Darüber hinaus werden verschiedene auf Nanotechnologie basierende Ansätze, wie die Verwendung von nanostrukturierten Beschichtungen oder Oberflächenmodifikationen, für den Anodisierungs- und Beschichtungsprozess untersucht, um die Leistung und Haltbarkeit von beschichteten Oberflächen zu verbessern. Diese innovativen Technologien haben das Potenzial, die Anodisierungs- und Beschichtungsindustrie zu revolutionieren und bieten neue Möglichkeiten für fortschrittliche Oberflächenbehandlungen.
Abschluss
Der Anodisierungs- und Beschichtungsprozess spielt in vielen industriellen Anwendungen eine entscheidende Rolle, indem er verbesserte Oberflächeneigenschaften wie Korrosionsbeständigkeit, Verschleißfestigkeit und verbesserte Ästhetik bietet. Die Prozesse werden in verschiedenen Branchen wie Automobil, Luft- und Raumfahrt, Elektronik und Medizintechnik weit verbreitet eingesetzt. Die hohe Nachfrage nach diesen Verfahren hat zur Entwicklung neuer Technologien und Ansätze zur Verbesserung von Effizienz, Leistung und Nachhaltigkeit geführt. Die Verwendung von Kühlern und Temperaturregelsystemen ist entscheidend für die Aufrechterhaltung des richtigen Temperaturbereichs und die Sicherstellung konsistenter und zuverlässiger Beschichtungsergebnisse. Fortschrittliche Technologien wie Impulsplattieren, stromloses Plattieren und auf Nanotechnologie basierende Ansätze bieten aufregende Möglichkeiten für die Zukunft des Anodisierungs- und Plattierungsprozesses. Da industrielle Anwendungen weiter wachsen und sich weiterentwickeln, wird erwartet, dass die Nachfrage nach Anodisierungs- und Beschichtungsverfahren steigen wird, was weitere Fortschritte in der Technologie und neue Ansätze für Oberflächenbehandlungen vorantreiben wird.
Status und Rolle des Kühlers im Anodisierungs- und Beschichtungsprozess
Kühler spielen eine entscheidende Rolle in der Anodisierungs- und Beschichtungsprozessindustrie, indem sie eine zuverlässige und effiziente Temperaturregelung für Beschichtungslösungen und Elektrolytlösungen bieten. Der Einsatz von Kühlern ist weit verbreitet und unerlässlich, um konsistente Beschichtungsergebnisse sicherzustellen und eine hohe Produktqualität aufrechtzuerhalten. Darüber hinaus bieten Kältemaschinen Vorteile wie verbesserte Energieeffizienz, reduzierten Wasserverbrauch und längere Lebensdauer der Ausrüstung. Mit dem Aufkommen neuer Beschichtungs- und Oberflächenbehandlungstechnologien wird erwartet, dass die Rolle von Kühlern bei der Gewährleistung optimaler Prozessbedingungen und -leistung noch wichtiger wird. Infolgedessen wird sich die Branche der Anodisierungs- und Beschichtungsprozesse in absehbarer Zukunft wahrscheinlich weiterhin auf Kühler und andere Temperaturregelsysteme verlassen.
Professioneller Lieferant von Anodisierungs- und Beschichtungsprozesskühlern
Wenn Sie einen zuverlässigen und effizienten Kühler für Ihren Anodisierungs- und Beschichtungsprozess benötigen, sind Sie bei SCY Chiller genau richtig. Unsere Kühler sind so konzipiert, dass sie eine präzise Temperaturregelung für eine Vielzahl industrieller Anwendungen bieten, einschließlich Beschichtungs- und Oberflächenbehandlungsverfahren. Wir bieten eine Vielzahl von Kältemaschinentypen an, wie z. B. luftgekühlte und wassergekühlte Kältemaschinen, um Ihre spezifischen Bedürfnisse und Anforderungen zu erfüllen. Unsere Kühler sind energieeffizient, einfach zu bedienen und erfordern nur minimale Wartung, wodurch sichergestellt wird, dass Ihr Anodisierungs- und Beschichtungsprozess reibungslos und effizient abläuft. Kontaktiere uns Erfahren Sie noch heute mehr über unsere Kühllösungen und wie wir Ihnen helfen können, Ihren Anodisierungs- und Beschichtungsprozess zu optimieren.