Les procédés d'anodisation et de placage sont deux méthodes de traitement de surface largement utilisées dans la production industrielle, visant à améliorer les performances, la durabilité et l'attrait esthétique des composants métalliques et plastiques. L'anodisation est un processus électrochimique qui crée une couche d'oxyde épaisse et protectrice à la surface d'un substrat métallique, grâce à l'oxydation contrôlée du matériau. Cette couche d'oxyde améliore non seulement la résistance du métal à la corrosion, à l'usure et à la température, mais peut également servir de base pour la coloration ou l'impression.
D'autre part, le placage est un processus qui consiste à déposer une fine couche de métal sur la surface d'un substrat en utilisant des méthodes de placage électrolytique ou autocatalytique. Le placage est généralement utilisé pour améliorer la dureté de surface, la résistance à l'abrasion et la conductivité électrique d'un substrat, mais peut également être utilisé à des fins décoratives. Les processus d'anodisation et de placage nécessitent un contrôle strict de divers paramètres pour garantir des résultats cohérents de haute qualité, ce qui en fait une partie importante de diverses industries, notamment l'automobile, l'aérospatiale, l'électronique et la construction.
Alors que les deux procédés visent à améliorer les propriétés de surface d'un substrat, ils diffèrent dans leurs mécanismes et leurs applications. Dans les sections suivantes, nous décrirons les principes, les processus et les applications du processus de placage et du processus d'anodisation, y compris les différents types de placage et d'anodisation, leurs avantages et inconvénients respectifs, ainsi que les défis et les innovations de chaque processus. Nous discuterons également de l'importance de l'eau de refroidissement et du rôle des refroidisseurs pour assurer la qualité et l'efficacité des processus de placage et d'anodisation.
Processus d'anodisation
Le processus d'anodisation crée une couche d'oxyde épaisse et protectrice à la surface d'un substrat métallique. Le processus consiste à immerger le substrat métallique dans une solution d'électrolyte, qui est généralement un acide, et à y faire passer un courant électrique. En conséquence, les ions oxygène dans la solution d'électrolyte sont attirés vers la surface du substrat métallique et se combinent avec les atomes métalliques pour former une couche stable et dense d'oxyde d'aluminium. Cette couche d'oxyde constitue une excellente barrière contre la corrosion, l'usure et les facteurs environnementaux. Le processus d'anodisation peut être effectué selon différents types, y compris l'anodisation à l'acide sulfurique, l'anodisation à l'acide chromique et l'anodisation dure, en fonction des propriétés souhaitées de la couche d'oxyde. Le processus d'anodisation est un processus sûr et respectueux de l'environnement qui ne modifie pas la composition du métal, ce qui le rend adapté à un large éventail d'applications, y compris les industries de l'aérospatiale, de l'automobile et de la construction.
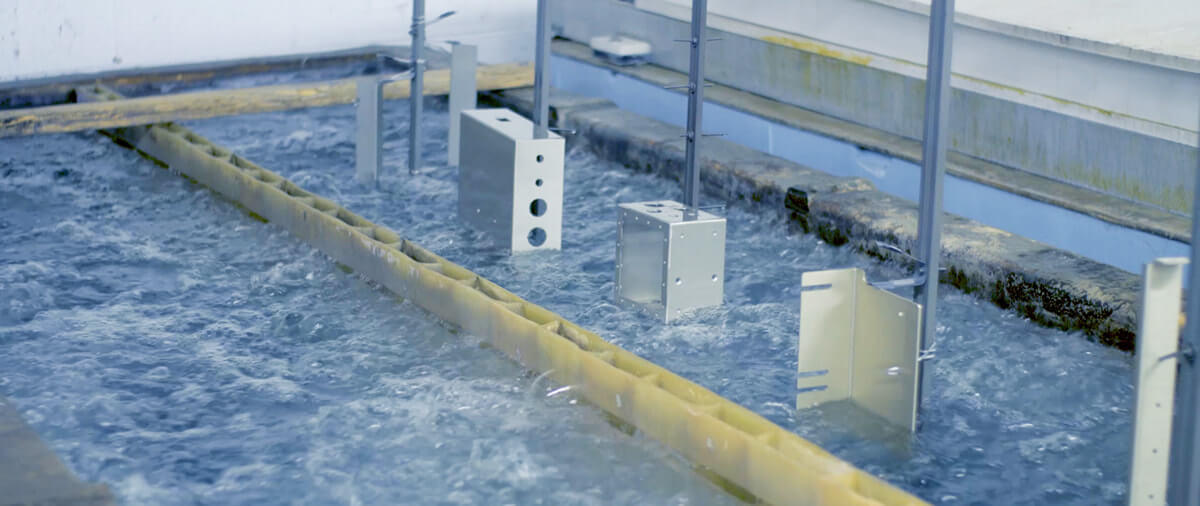
Types de processus d'anodisation
Le processus d'anodisation est une méthode de traitement de surface polyvalente qui peut être classée en différents types en fonction de la solution d'électrolyte utilisée et des propriétés souhaitées de la couche d'oxyde.
- Anodisation à l'acide sulfurique est le type le plus courant de processus d'anodisation et donne une couche d'oxyde dense et dure qui est très résistante à la corrosion, à l'usure et aux facteurs environnementaux. Ce type d'anodisation peut être encore teint ou peint pour obtenir différentes couleurs et effets esthétiques.
- Anodisation à l'acide chromique, d'autre part, donne une couche d'oxyde plus fine et plus flexible qui a une bonne adhérence au substrat et est idéale pour les applications aérospatiales et électriques.
- Anodisation dure est un type d'anodisation à l'acide sulfurique qui implique des tensions et des températures plus élevées, ce qui donne une couche d'oxyde épaisse et résistante à l'usure qui convient aux applications à fortes contraintes telles que les tiges de piston et les vérins hydrauliques.
Le processus d'anodisation a un large éventail d'applications dans diverses industries, notamment l'aérospatiale, l'automobile, l'électronique et la construction. Les pièces anodisées sont couramment utilisées dans les structures d'avions, les carrosseries automobiles, les boîtiers électroniques et les finitions architecturales. Les avantages du processus d'anodisation comprennent une résistance à la corrosion, une résistance à l'usure et un attrait esthétique améliorés, ce qui en fait une méthode de traitement de surface populaire et rentable pour divers substrats.
Avantages et inconvénients du processus d'anodisation
Le processus d'anodisation est une méthode de traitement de surface largement utilisée qui offre plusieurs avantages mais présente également certaines limites.
Les avantages du processus d'anodisation incluent la création d'une couche de surface dure, durable et résistante à la corrosion qui améliore les propriétés fonctionnelles et esthétiques d'un substrat. L'anodisation est également un procédé sûr et écologique qui ne modifie pas la composition du métal. De plus, le processus d'anodisation peut être effectué dans différents types, offrant une flexibilité dans l'obtention de différentes couleurs, finitions et propriétés.
Cependant, il existe également certaines limitations au processus d'anodisation. Par exemple, l'épaisseur de la couche d'oxyde est limitée et peut affecter les propriétés mécaniques du substrat. Le processus d'anodisation nécessite également un contrôle strict de divers paramètres de processus, ce qui peut augmenter le coût et le temps requis pour la production. De plus, certains types d'anodisation, comme l'anodisation à l'acide chromique, peuvent être dangereux pour la santé et l'environnement. Malgré ces limitations, le processus d'anodisation reste une méthode de traitement de surface populaire et rentable pour diverses applications.
Avantages | Les inconvénients |
Couche de surface dure, durable et résistante à la corrosion | L'épaisseur limitée de la couche d'oxyde peut affecter les propriétés mécaniques |
Processus sûr et écologique | Nécessite un contrôle strict de divers paramètres de processus, ce qui augmente le coût et le temps |
Fournit une flexibilité dans la réalisation de différentes couleurs, finitions et propriétés | Certains types d'anodisation peuvent être dangereux pour la santé et l'environnement |
Méthodes d'inspection de la qualité de l'anodisation
Pour garantir des résultats de haute qualité et cohérents dans le processus d'anodisation, diverses méthodes d'inspection et de contrôle de la qualité sont utilisées. L'une des méthodes les plus courantes consiste à mesurer l'épaisseur et la porosité de la couche d'oxyde à l'aide de techniques de test non destructif telles que le test par courants de Foucault, la fluorescence X ou l'induction magnétique. L'aspect de surface, la couleur et la brillance des pièces anodisées peuvent être inspectés visuellement ou à l'aide de colorimètres et de brillancemètres. D'autres méthodes de contrôle de la qualité comprennent le test de la résistance à la corrosion, de la résistance à l'usure et de la force d'adhérence de la couche anodisée à l'aide de tests au brouillard salin, de tests de rayures et de tests de pelage. Pour maintenir la qualité et la cohérence du processus d'anodisation, il est crucial de contrôler divers paramètres de processus, y compris la concentration et le pH de la solution d'électrolyte, la température et la densité de courant, ainsi que le taux d'agitation. Les systèmes de surveillance et de rétroaction en temps réel peuvent aider à identifier et à corriger les écarts de processus, garantissant que les produits finaux répondent aux spécifications et aux exigences de performance souhaitées.
Pour les petits systèmes de réfrigération utilisant des tubes capillaires, trop de liquide ajouté peut provoquer un reflux de liquide. Lorsque le givre de l'évaporateur est grave ou que le ventilateur tombe en panne, le transfert de chaleur devient médiocre et le liquide non évaporé provoquera un retour de liquide. De fréquentes fluctuations de température peuvent également empêcher le détendeur de répondre et provoquer le phénomène | But |
Techniques de contrôle non destructif | Mesurer l'épaisseur et la porosité de la couche d'oxyde à l'aide de courants de Foucault, XRF ou MI |
Inspection visuelle et instruments | Inspectez l'apparence, la couleur et la brillance de la surface à l'aide d'une inspection visuelle ou d'instruments |
Essais de résistance à la corrosion | Testez la résistance à la corrosion de la couche anodisée à l'aide d'essais au brouillard salin |
Test de résistance à l'usure | Testez la résistance à l'usure de la couche anodisée à l'aide d'un test de rayure |
Test de force d'adhérence | Testez la force d'adhérence de la couche anodisée à l'aide d'un test de pelage |
Paramètres de contrôle de processus | Contrôlez les paramètres de processus tels que la concentration de la solution d'électrolyte, la température, etc. |
Systèmes de surveillance en temps réel | Identifiez et corrigez les écarts de processus en temps réel pour garantir des résultats cohérents |
Processus de placage
Le processus de placage est une méthode de traitement de surface qui consiste à déposer une fine couche de métal sur la surface d'un substrat à l'aide d'un processus de placage électrolytique ou autocatalytique. La galvanoplastie est un processus qui consiste à faire passer un courant électrique à travers une solution d'électrolyte contenant des ions métalliques, qui sont ensuite attirés vers le substrat et déposés sur sa surface. Le placage autocatalytique, quant à lui, implique une réaction de réduction chimique qui dépose des ions métalliques sur la surface du substrat sans avoir besoin d'un courant électrique externe. Le processus de placage peut être effectué sur une variété de substrats, y compris les métaux, les plastiques et les céramiques, pour améliorer leurs propriétés de surface, telles que la résistance à l'usure, la résistance à la corrosion et la conductivité électrique. L'épaisseur, l'adhérence et les propriétés de la couche plaquée peuvent être contrôlées en ajustant divers paramètres de processus, tels que la composition et le pH de la solution de placage, la température et la vitesse d'agitation, et la densité de courant. Dans les sections suivantes, nous discuterons des différents types de procédés de placage, de leurs avantages et inconvénients, et de leurs applications dans diverses industries. Nous discuterons également de l'importance de l'eau de refroidissement et du rôle des refroidisseurs dans le processus de placage.
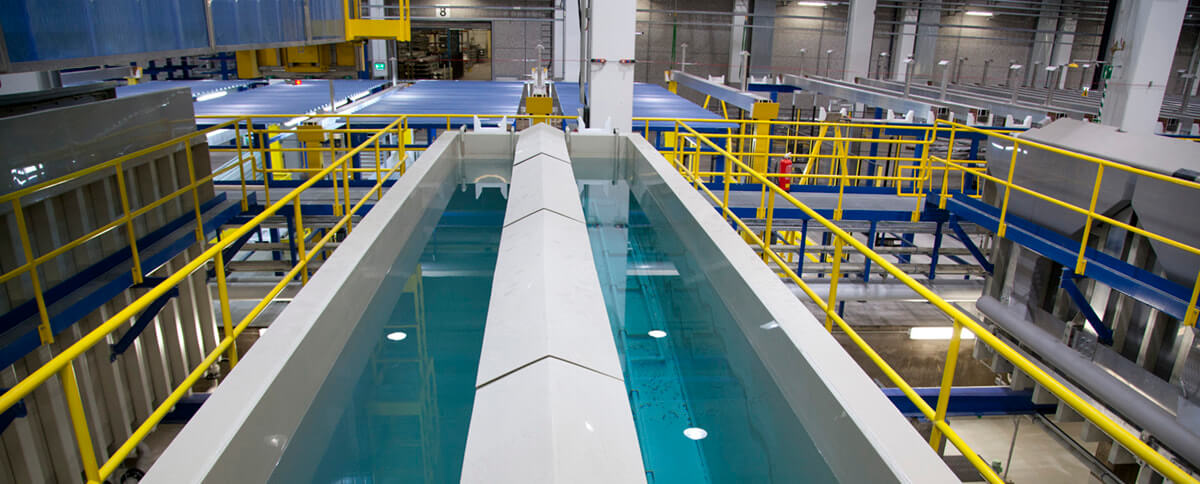
Types de processus de placage
Le processus de placage peut être classé en différents types en fonction du type de métal utilisé dans la solution de placage, du matériau du substrat et des propriétés de la couche plaquée. Certains des types les plus courants de processus de placage comprennent le nickelage autocatalytique, le placage à l'or, le placage à l'argent et le placage au cuivre.
- Le placage autocatalytique au nickel est un type de procédé de placage largement utilisé qui offre d'excellentes propriétés de résistance à l'usure, de résistance à la corrosion et de dureté.
- Le placage à l'or est connu pour son excellente conductivité, sa résistance à la corrosion et son attrait esthétique, ce qui le rend adapté aux applications électroniques et de bijouterie.
- Le placage d'argent est un autre type populaire de processus de placage qui offre une excellente conductivité et est couramment utilisé dans les contacts et connecteurs électriques.
- Le placage de cuivre est souvent utilisé comme sous-couche pour d'autres types de placage afin d'améliorer les propriétés d'adhérence et de résistance à la corrosion de la couche plaquée.
Le procédé de placage a un large éventail d'applications dans diverses industries, notamment l'aérospatiale, l'automobile, l'électronique et le médical. Il peut être utilisé pour améliorer les performances, l'apparence et la durabilité d'un substrat et est souvent utilisé dans la fabrication de pièces, de composants et de produits finis. Les avantages du processus de placage comprennent des propriétés améliorées, un coût réduit et le respect de l'environnement, ce qui en fait une méthode de traitement de surface populaire et rentable pour diverses applications.
Avantages et inconvénients du processus de placage
Les avantages du procédé de placage incluent la possibilité de déposer une fine couche de métal sur une surface de substrat, ce qui améliore les propriétés de surface du substrat, telles que la résistance à l'usure, la résistance à la corrosion et la conductivité électrique. Le processus de placage peut également être effectué sur une variété de substrats, ce qui en fait une méthode de traitement de surface polyvalente. De plus, le processus de placage peut être effectué en différents types, offrant une flexibilité dans l'obtention de diverses propriétés et finitions.
Les limites du processus de placage. Par exemple, le processus nécessite un contrôle strict de divers paramètres de processus, ce qui peut augmenter le coût et le temps requis pour la production. De plus, certains types de processus de placage, tels que la galvanoplastie, nécessitent une quantité importante d'électricité et génèrent des eaux usées, qui peuvent être dangereuses pour l'environnement. Malgré ces limitations, le procédé de placage reste une méthode de traitement de surface populaire et rentable pour diverses applications.
Avantages | Les inconvénients |
Dépôt d'une fine couche de métal sur une surface de substrat | Nécessite un contrôle strict de divers paramètres, augmentant le coût et le temps de production |
Améliore les propriétés de surface du substrat | Certains types de processus de placage génèrent des eaux usées et consomment une quantité importante d'électricité, ce qui peut être nocif pour l'environnement |
Polyvalent et peut être réalisé sur une variété de substrats | |
Différents types disponibles, permettant diverses propriétés et finitions |
Méthodes d'inspection de la qualité du placage
L'inspection et le contrôle de la qualité sont cruciaux dans le processus de placage pour garantir des résultats de haute qualité et cohérents. Certaines des méthodes de contrôle de la qualité les plus courantes comprennent la mesure de l'épaisseur et de la force d'adhérence de la couche plaquée, l'inspection visuelle de la surface à la recherche de défauts et le test de la résistance à la corrosion, de la résistance à l'usure et de la conductivité électrique de la couche plaquée. Ces tests sont généralement effectués à l'aide de techniques non destructives telles que la fluorescence X et l'induction magnétique. En plus des tests, le contrôle de divers paramètres de processus tels que la composition et la valeur du pH de la solution de placage, la température et le taux d'agitation, et la densité de courant est important pour maintenir la qualité et la cohérence de la couche plaquée. Les systèmes de surveillance et de rétroaction en temps réel peuvent aider à identifier et à corriger les écarts de processus, garantissant que les produits finaux répondent aux spécifications et aux exigences de performance souhaitées. En mettant en œuvre un système de contrôle qualité rigoureux, Plating Process peut produire des produits de haute qualité, fiables et rentables pour diverses applications.
Pour les petits systèmes de réfrigération utilisant des tubes capillaires, trop de liquide ajouté peut provoquer un reflux de liquide. Lorsque le givre de l'évaporateur est grave ou que le ventilateur tombe en panne, le transfert de chaleur devient médiocre et le liquide non évaporé provoquera un retour de liquide. De fréquentes fluctuations de température peuvent également empêcher le détendeur de répondre et provoquer le phénomène | But |
Techniques de contrôle non destructif | Mesurer l'épaisseur et la force d'adhérence de la couche plaquée à l'aide de XRF ou d'induction magnétique |
Inspection visuelle | Inspectez visuellement la surface pour détecter les défauts |
Essais de résistance à la corrosion | Testez la résistance à la corrosion de la couche plaquée à l'aide d'essais au brouillard salin |
Test de résistance à l'usure | Testez la résistance à l'usure de la couche plaquée à l'aide d'un test de rayure |
Test de conductivité électrique | Testez la conductivité électrique de la couche plaquée à l'aide de tests de résistance |
Paramètres de contrôle de processus | Contrôlez les paramètres du processus tels que la composition de la solution de placage, la température, etc. |
Systèmes de surveillance en temps réel | Identifiez et corrigez les écarts de processus en temps réel pour garantir des résultats cohérents |
Besoins en eau de refroidissement dans le processus d'anodisation et de placage
Le contrôle de la température est un facteur critique dans les processus d'anodisation et de placage. La solution de placage ou la solution d'électrolyte utilisée dans les deux processus a une plage de température qui doit être maintenue dans une tolérance spécifique. La température de la solution de placage ou de la solution d'électrolyte affecte la vitesse de placage, l'épaisseur, la qualité et les propriétés de la couche plaquée. Par exemple, si la température est trop élevée, la couche plaquée peut devenir poreuse, cassante ou avoir une faible force d'adhérence. D'autre part, si la température est trop basse, la vitesse de placage peut être trop lente, ce qui peut entraîner un dépôt irrégulier ou des propriétés incohérentes. Pour maintenir la plage de température appropriée, des systèmes de contrôle de la température, tels que des refroidisseurs ou des réchauffeurs, sont couramment utilisés pour réguler la température de la solution de placage ou d'électrolyte. La température de l'eau de refroidissement utilisée dans le système de contrôle de la température est également importante et doit être soigneusement contrôlée pour s'assurer que la température de la solution de placage ou d'électrolyte reste dans la plage souhaitée. Dans les sections suivantes, nous discuterons des besoins en eau de refroidissement et du rôle des refroidisseurs dans les processus d'anodisation et de placage.
Application du refroidisseur dans le processus d'anodisation et de placage
Les refroidisseurs jouent un rôle essentiel dans le maintien de la plage de température appropriée dans le processus d'anodisation et de placage. Les refroidisseurs sont couramment utilisés pour refroidir la solution de placage ou d'électrolyte afin de maintenir la plage de température appropriée pour des résultats de placage constants. Les refroidisseurs éliminent l'excès de chaleur généré par le processus d'anodisation et de placage et maintiennent la température dans la plage souhaitée. La capacité de refroidissement du refroidisseur doit être adaptée aux exigences spécifiques du processus d'anodisation et de placage pour assurer un contrôle de température approprié. Différents types de refroidisseurs, tels que les refroidisseurs à air ou à eau, peuvent être utilisés en fonction de l'application et des exigences du processus. Le refroidisseur peut également offrir des avantages supplémentaires, tels qu'une efficacité énergétique accrue, une consommation d'eau réduite et une durée de vie améliorée de l'équipement. En plus de fournir un contrôle de la température, les refroidisseurs peuvent également offrir d'autres fonctionnalités telles que la surveillance du débit et le contrôle automatique de la température pour aider à maintenir des conditions de processus optimales. L'application appropriée des refroidisseurs peut aider à garantir des résultats cohérents et de haute qualité dans le processus d'anodisation et de placage.
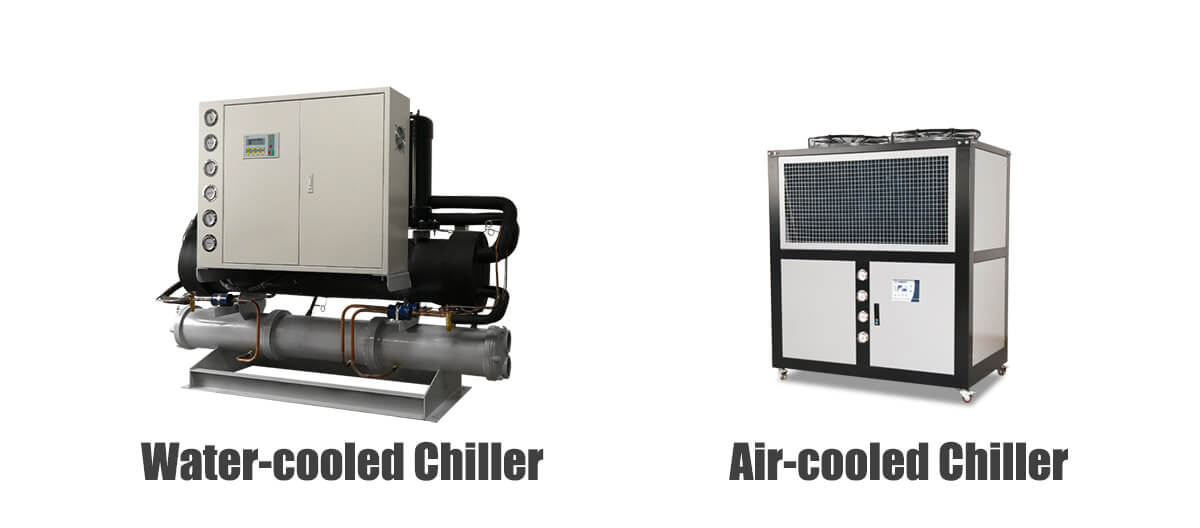
Points clés pour la sélection et la configuration du refroidisseur
- Capacité de refroidissement: La capacité de refroidissement du refroidisseur doit être adaptée aux exigences spécifiques du processus d'anodisation et de placage pour assurer un contrôle de température approprié. La capacité de refroidissement du refroidisseur est généralement mesurée en tonnes ou en kilowatts et doit être sélectionnée en fonction de la charge thermique du processus. Si vous avez des données comme la différence de température de l'eau d'entrée et de sortie et le débit de la solution, veuillez vous référer à notre Soustrayez votre température de départ de votre température actuelle et notez le résultat, connu sous le nom de différentiel de température..
- Type de refroidisseur : Le type de refroidisseur, tel que refroidi par air ou refroidi par eau, doit être sélectionné en fonction des exigences spécifiques de l'application et du processus. Les refroidisseurs refroidis par eau sont généralement plus efficaces et peuvent fournir des capacités de refroidissement plus élevées, mais nécessitent l'accès à une tour de refroidissement et consomment plus d'eau. Refroidisseurs refroidis à l’air, d'autre part, sont plus faciles à installer et à entretenir, mais ont des capacités de refroidissement inférieures et nécessitent plus d'espace pour évacuer la chaleur perdue.
- Plage de contrôle de température : Le refroidisseur doit pouvoir maintenir la température de la solution de placage ou d'électrolyte dans une plage spécifique. La plage est généralement déterminée par les exigences spécifiques du processus d'anodisation et de placage, et le refroidisseur doit être sélectionné en fonction de sa capacité à maintenir la plage de température requise.
- Débit et pression : Le débit et la pression de l'eau de refroidissement doivent être compatibles avec les exigences du refroidisseur. Le débit et la pression peuvent affecter les performances et l'efficacité du refroidisseur, il est donc important de s'assurer que le système d'eau de refroidissement est correctement conçu et configuré.
- Efficacité énergétique : L'efficacité énergétique du refroidisseur doit être prise en compte pour minimiser les coûts d'exploitation et réduire l'impact environnemental. Les refroidisseurs écoénergétiques peuvent aider à réduire les coûts énergétiques et à réduire les émissions de gaz à effet de serre.
- Entretien et SAV : Le refroidisseur doit être facile à entretenir et à entretenir pour minimiser les temps d'arrêt et assurer un fonctionnement fiable. Un entretien régulier, tel que le nettoyage de l'échangeur de chaleur et le remplacement des filtres, peut aider à maintenir les performances du refroidisseur et à prolonger sa durée de vie.
En tenant compte de ces points clés, il est possible de sélectionner et de configurer un refroidisseur qui répond aux exigences spécifiques du processus d'anodisation et de placage et fournit un contrôle de température fiable, efficace et rentable.
Dépannage du refroidisseur
L'entretien et le fonctionnement appropriés d'un refroidisseur sont cruciaux pour un contrôle de température fiable et constant dans le processus d'anodisation et de placage. Cependant, si un problème survient, il est important de pouvoir résoudre le problème et d'identifier la cause première du problème. Les problèmes courants avec les refroidisseurs peuvent inclure de faibles niveaux de réfrigérant, des filtres obstrués ou des composants défectueux tels que des compresseurs ou des échangeurs de chaleur. Dans certains cas, le problème peut être lié au système d'eau de refroidissement plutôt qu'au refroidisseur lui-même, comme des problèmes de débit ou de pression d'eau. Le dépannage peut impliquer diverses méthodes telles que l'inspection visuelle, la mesure des températures et des pressions ou l'utilisation d'outils de diagnostic tels que l'analyse des vibrations. En identifiant et en traitant la cause première du problème, il est possible de minimiser les temps d'arrêt et de garantir que le processus d'anodisation et de placage peut continuer à fonctionner à des niveaux de performance optimaux. Une maintenance et une surveillance régulières peuvent également aider à prévenir les problèmes et garantir que le refroidisseur et le système d'eau de refroidissement fonctionnent de manière fiable et efficace. Pour des informations de dépannage plus détaillées, reportez-vous à Liste de contrôle des 10 principales défaillances du système de réfrigération.
Technologies innovantes dans le processus d'anodisation et de placage
Les progrès technologiques ont conduit au développement d'approches nouvelles et innovantes pour les processus d'anodisation et de placage. Ces technologies peuvent offrir des avantages tels qu'une efficacité améliorée, un impact environnemental réduit et des performances améliorées.
Par exemple, le placage par impulsions est une technique qui utilise un courant intermittent pour déposer des ions métalliques sur un substrat, ce qui améliore l'adhérence et l'uniformité.
Un autre exemple est l'utilisation du placage autocatalytique, qui implique le dépôt d'une couche métallique sur un substrat sans avoir besoin d'une source d'alimentation externe. Cette technique peut entraîner des propriétés améliorées telles que la résistance à la corrosion et la dureté.
En outre, diverses approches basées sur la nanotechnologie, telles que l'utilisation de revêtements nanostructurés ou de modifications de surface, sont explorées pour le processus d'anodisation et de placage afin d'améliorer les performances et la durabilité des surfaces plaquées. Ces technologies innovantes ont le potentiel de révolutionner l'industrie des procédés d'anodisation et de placage et d'offrir de nouvelles possibilités de traitements de surface avancés.
Conclusion
Le processus d'anodisation et de placage joue un rôle crucial dans de nombreuses applications industrielles en fournissant des propriétés de surface améliorées, telles que la résistance à la corrosion, la résistance à l'usure et l'esthétique améliorée. Les processus sont largement utilisés dans diverses industries telles que l'automobile, l'aérospatiale, l'électronique et les dispositifs médicaux. La forte demande pour ces processus a conduit au développement de nouvelles technologies et approches pour améliorer l'efficacité, les performances et la durabilité. L'utilisation de refroidisseurs et de systèmes de contrôle de la température est essentielle pour maintenir la plage de température appropriée et garantir des résultats de placage cohérents et fiables. Les technologies avancées telles que le placage par impulsions, le placage autocatalytique et les approches basées sur la nanotechnologie offrent des possibilités intéressantes pour l'avenir du processus d'anodisation et de placage. À mesure que les applications industrielles continuent de croître et d'évoluer, la demande de processus d'anodisation et de placage devrait augmenter, entraînant de nouvelles avancées technologiques et de nouvelles approches des traitements de surface.
Statut et rôle du refroidisseur dans le processus d'anodisation et de placage
Les refroidisseurs jouent un rôle essentiel dans l'industrie des processus d'anodisation et de placage en fournissant un contrôle de température fiable et efficace pour les solutions de placage et les solutions d'électrolyte. L'utilisation de refroidisseurs est répandue et essentielle pour garantir des résultats de placage constants et maintenir une qualité élevée des produits. De plus, les refroidisseurs offrent des avantages tels qu'une efficacité énergétique améliorée, une consommation d'eau réduite et une durée de vie plus longue de l'équipement. Alors que de nouvelles technologies de placage et de traitement de surface continuent d'émerger, le rôle des refroidisseurs devrait devenir encore plus important pour garantir des conditions et des performances de processus optimales. En conséquence, l'industrie des procédés d'anodisation et de placage continuera probablement de s'appuyer sur des refroidisseurs et d'autres systèmes de contrôle de la température dans un avenir prévisible.
Fournisseur professionnel de refroidisseur de processus d'anodisation et de placage
Si vous avez besoin d'un refroidisseur fiable et efficace pour votre processus d'anodisation et de placage, ne cherchez pas plus loin que le refroidisseur SCY. Nos refroidisseurs sont conçus pour fournir un contrôle précis de la température pour une large gamme d'applications industrielles, y compris les processus de placage et de traitement de surface. Nous proposons une variété de types de refroidisseurs, tels que des refroidisseurs à air et à eau, pour répondre à vos besoins et exigences spécifiques. Nos refroidisseurs sont économes en énergie, faciles à utiliser et nécessitent un entretien minimal, garantissant que votre processus d'anodisation et de placage se déroule de manière fluide et efficace. Contactez-nous aujourd'hui pour en savoir plus sur nos solutions de refroidissement et sur la manière dont nous pouvons vous aider à optimiser votre processus d'anodisation et de placage.