Anodizing&Plating Processes are two widely used surface treatment methods in industrial production, aimed at improving the performance, durability, and aesthetic appeal of metal and plastic components. Anodizing is an electrochemical process that creates a thick, protective oxide layer on the surface of a metal substrate, through the controlled oxidation of the material. This oxide layer not only enhances the metal’s resistance to corrosion, wear and tear, and temperature but can also serve as a base for coloring or printing.
Por otro lado, el enchapado es un proceso que consiste en depositar una capa delgada de metal en la superficie de un sustrato utilizando métodos de enchapado galvánico o no electrolítico. El enchapado generalmente se usa para mejorar la dureza de la superficie, la resistencia a la abrasión y la conductividad eléctrica de un sustrato, pero también se puede usar con fines decorativos. Tanto el proceso de anodizado como el de recubrimiento requieren un control estricto de varios parámetros para garantizar resultados consistentes y de alta calidad, lo que los convierte en una parte importante de varias industrias, incluidas la automotriz, aeroespacial, electrónica y de construcción.
Si bien ambos procesos tienen como objetivo mejorar las propiedades de la superficie de un sustrato, difieren en sus mecanismos y aplicaciones. En las siguientes secciones, describiremos los principios, procesos y aplicaciones del proceso de enchapado y el proceso de anodizado, incluidos los diferentes tipos de enchapado y anodizado, sus respectivas ventajas y desventajas, y los desafíos e innovaciones en cada proceso. También discutiremos la importancia del agua de enfriamiento y el papel de los enfriadores para garantizar la calidad y la eficiencia de los procesos de enchapado y anodizado.
Proceso de anodizado
El proceso de anodizado crea una capa protectora de óxido gruesa en la superficie de un sustrato de metal. El proceso consiste en sumergir el sustrato de metal en una solución electrolítica, que suele ser un ácido, y pasar una corriente eléctrica a través de ella. Como resultado, los iones de oxígeno en la solución electrolítica son atraídos a la superficie del sustrato de metal y se combinan con los átomos de metal para formar una capa densa y estable de óxido de aluminio. Esta capa de óxido proporciona una excelente barrera contra la corrosión, el desgaste y los factores ambientales. El proceso de anodizado se puede realizar en diferentes tipos, incluido el anodizado con ácido sulfúrico, el anodizado con ácido crómico y el anodizado duro, según las propiedades deseadas de la capa de óxido. El proceso de anodizado es un proceso seguro y ecológico que no altera la composición del metal, lo que lo hace adecuado para una amplia gama de aplicaciones, incluidas las industrias aeroespacial, automotriz y de la construcción.
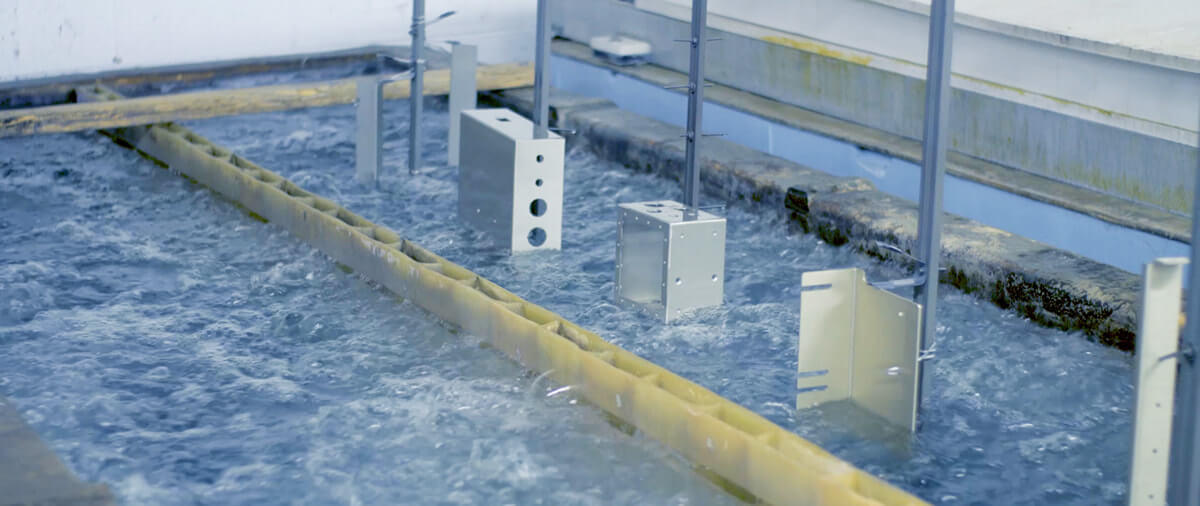
Tipos de procesos de anodizado
El proceso de anodizado es un método de tratamiento de superficie versátil que se puede clasificar en diferentes tipos según la solución de electrolito utilizada y las propiedades deseadas de la capa de óxido.
- Anodizado con ácido sulfúrico es el tipo más común de proceso de anodizado y da como resultado una capa de óxido densa y dura que es altamente resistente a la corrosión, el desgaste y los factores ambientales. Este tipo de anodizado se puede teñir o pintar para lograr diferentes colores y efectos estéticos.
- Anodizado con ácido crómico, por otro lado, da como resultado una capa de óxido más delgada y flexible que tiene una buena adherencia al sustrato y es ideal para aplicaciones aeroespaciales y eléctricas.
- anodizado duro es un tipo de anodizado con ácido sulfúrico que involucra voltajes y temperaturas más altos, lo que da como resultado una capa de óxido gruesa y resistente al desgaste que es adecuada para aplicaciones de alta tensión, como vástagos de pistón y cilindros hidráulicos.
El proceso de anodizado tiene una amplia gama de aplicaciones en diversas industrias, incluidas la aeroespacial, automotriz, electrónica y de construcción. Las piezas anodizadas se utilizan comúnmente en estructuras de aeronaves, carrocerías de automóviles, carcasas electrónicas y acabados arquitectónicos. Los beneficios del proceso de anodizado incluyen mayor resistencia a la corrosión, resistencia al desgaste y atractivo estético, lo que lo convierte en un método de tratamiento de superficie popular y rentable para diversos sustratos.
Pros y contras del proceso de anodizado
El proceso de anodizado es un método de tratamiento de superficies ampliamente utilizado que brinda varios beneficios pero también tiene algunas limitaciones.
Las ventajas del proceso de anodizado incluyen la creación de una capa superficial dura, duradera y resistente a la corrosión que mejora las propiedades funcionales y estéticas de un sustrato. El anodizado es también un proceso seguro y ecológico que no altera la composición del metal. Además, el proceso de anodizado se puede realizar en diferentes tipos, brindando flexibilidad para lograr varios colores, acabados y propiedades.
Sin embargo, también existen algunas limitaciones en el proceso de anodizado. Por ejemplo, el espesor de la capa de óxido es limitado y puede afectar las propiedades mecánicas del sustrato. El proceso de anodizado también requiere un control estricto de varios parámetros del proceso, lo que puede aumentar el costo y el tiempo requerido para la producción. Además, algunos tipos de anodizado, como el anodizado con ácido crómico, pueden ser peligrosos para la salud y el medio ambiente. A pesar de estas limitaciones, el proceso de anodizado sigue siendo un método de tratamiento de superficies popular y rentable para diversas aplicaciones.
ventajas | Contras |
Capa superficial dura, duradera y resistente a la corrosión | El espesor limitado de la capa de óxido puede afectar las propiedades mecánicas |
Proceso seguro y ecológico. | Requiere un control estricto de varios parámetros del proceso, lo que aumenta el costo y el tiempo |
Brinda flexibilidad para lograr varios colores, acabados y propiedades. | Algunos tipos de anodizado pueden ser peligrosos para la salud y el medio ambiente |
Métodos de inspección de calidad de anodizado
Para garantizar resultados consistentes y de alta calidad en el proceso de anodizado, se utilizan varios métodos de inspección y control de calidad. Uno de los métodos más comunes es medir el grosor y la porosidad de la capa de óxido utilizando técnicas de prueba no destructivas, como la prueba de corrientes parásitas, la fluorescencia de rayos X o la inducción magnética. La apariencia de la superficie, el color y el brillo de las piezas anodizadas se pueden inspeccionar visualmente o usando colorímetros y medidores de brillo. Otros métodos de control de calidad incluyen probar la resistencia a la corrosión, la resistencia al desgaste y la fuerza de adhesión de la capa anodizada mediante pruebas de niebla salina, pruebas de rayado y pruebas de pelado. Para mantener la calidad y la consistencia del proceso de anodizado, es crucial controlar varios parámetros del proceso, incluida la concentración y el valor de pH de la solución electrolítica, la temperatura y la densidad de corriente, y la tasa de agitación. Los sistemas de monitoreo y retroalimentación en tiempo real pueden ayudar a identificar y corregir las desviaciones del proceso, asegurando que los productos finales cumplan con las especificaciones deseadas y los requisitos de rendimiento.
En los sistemas de refrigeración pequeños que utilizan tubos capilares, la adición de demasiado líquido puede causar reflujo de líquido. Cuando la escarcha del evaporador es grave o el ventilador falla, la transferencia de calor se vuelve deficiente y el líquido no evaporado provocará el retorno del líquido. Las fluctuaciones frecuentes de temperatura también pueden hacer que la válvula de expansión no responda y provoque el fenómeno. | Objetivo |
Técnicas de ensayos no destructivos | Mida el grosor y la porosidad de la capa de óxido utilizando corrientes de Foucault, XRF o MI |
Inspección visual e instrumentos | Inspeccione la apariencia, el color y el brillo de la superficie mediante inspección visual o instrumentos |
Ensayos de resistencia a la corrosión | Pruebe la resistencia a la corrosión de la capa anodizada mediante la prueba de niebla salina |
Prueba de resistencia al desgaste | Pruebe la resistencia al desgaste de la capa anodizada mediante pruebas de rayado |
Prueba de fuerza de adherencia | Pruebe la fuerza de adhesión de la capa anodizada usando la prueba de pelado |
Parámetros de control de procesos | Controle los parámetros del proceso, como la concentración de la solución de electrolitos, la temperatura, etc. |
Sistemas de monitoreo en tiempo real | Identifique y corrija las desviaciones del proceso en tiempo real para garantizar resultados consistentes |
Proceso de chapado
El proceso de recubrimiento es un método de tratamiento de superficies que consiste en depositar una capa delgada de metal sobre la superficie de un sustrato mediante un proceso de recubrimiento electrolítico o electrolítico. La galvanoplastia es un proceso que consiste en hacer pasar una corriente eléctrica a través de una solución electrolítica que contiene iones metálicos, que luego son atraídos por el sustrato y depositados en su superficie. El recubrimiento sin electricidad, por otro lado, implica una reacción de reducción química que deposita iones metálicos en la superficie del sustrato sin necesidad de una corriente eléctrica externa. El proceso de recubrimiento se puede realizar en una variedad de sustratos, incluidos metales, plásticos y cerámicas, para mejorar sus propiedades superficiales, como la resistencia al desgaste, la resistencia a la corrosión y la conductividad eléctrica. El grosor, la adhesión y las propiedades de la capa chapada se pueden controlar ajustando varios parámetros del proceso, como la composición y el valor de pH de la solución de chapado, la temperatura y la tasa de agitación, y la densidad de corriente. En las siguientes secciones, discutiremos los diferentes tipos de Procesos de Enchapado, sus ventajas y desventajas, y sus aplicaciones en varias industrias. También discutiremos la importancia del agua de enfriamiento y el papel de los enfriadores en el proceso de enchapado.
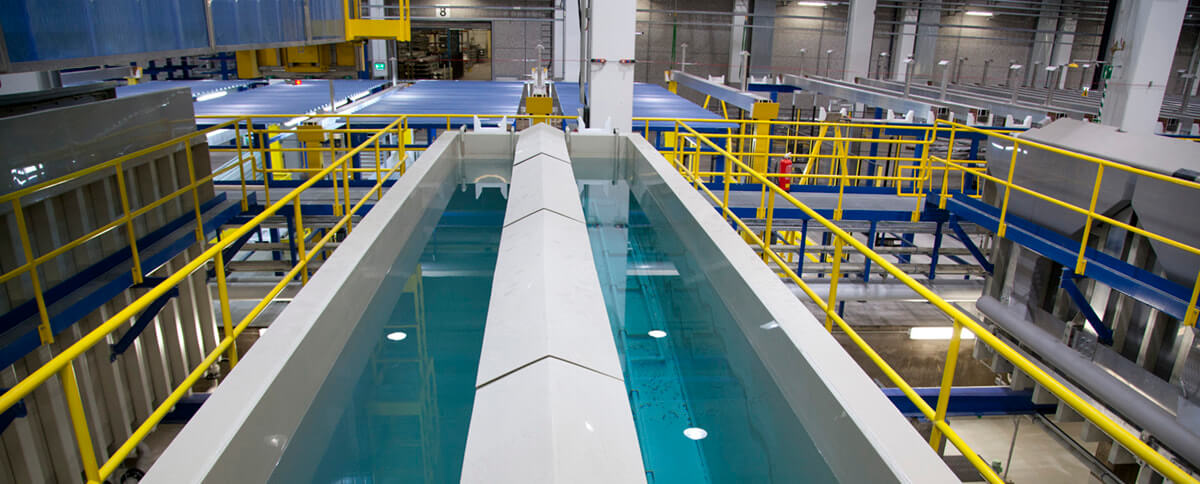
Tipos de procesos de enchapado
El proceso de enchapado se puede clasificar en varios tipos según el tipo de metal utilizado en la solución de enchapado, el material del sustrato y las propiedades de la capa enchapada. Algunos de los tipos más comunes de procesos de enchapado incluyen el enchapado de níquel sin corriente, el enchapado en oro, el enchapado en plata y el enchapado en cobre.
- El niquelado electrolítico es un tipo de proceso de recubrimiento ampliamente utilizado que proporciona una excelente resistencia al desgaste, resistencia a la corrosión y propiedades de dureza.
- El chapado en oro es conocido por su excelente conductividad, resistencia a la corrosión y atractivo estético, lo que lo hace adecuado para aplicaciones electrónicas y de joyería.
- El enchapado en plata es otro tipo popular de proceso de enchapado que proporciona una excelente conductividad y se usa comúnmente en contactos y conectores eléctricos.
- El enchapado de cobre se usa a menudo como capa base para otros tipos de enchapado para mejorar las propiedades de adhesión y resistencia a la corrosión de la capa enchapada.
El proceso de recubrimiento tiene una amplia gama de aplicaciones en diversas industrias, incluidas la aeroespacial, automotriz, electrónica y médica. Se puede usar para mejorar el rendimiento, la apariencia y la durabilidad de un sustrato y, a menudo, se usa en la fabricación de piezas, componentes y productos terminados. Los beneficios del proceso de recubrimiento incluyen propiedades mejoradas, menor costo y respeto al medio ambiente, lo que lo convierte en un método de tratamiento de superficies popular y rentable para diversas aplicaciones.
Pros y contras del proceso de enchapado
Las ventajas del proceso de recubrimiento incluyen la capacidad de depositar una capa delgada de metal sobre la superficie de un sustrato, lo que mejora las propiedades de la superficie del sustrato, como la resistencia al desgaste, la resistencia a la corrosión y la conductividad eléctrica. El proceso de recubrimiento también se puede realizar en una variedad de sustratos, lo que lo convierte en un método de tratamiento de superficie versátil. Además, el proceso de enchapado se puede realizar en diferentes tipos, brindando flexibilidad para lograr varias propiedades y acabados.
Las limitaciones del proceso de enchapado. Por ejemplo, el proceso requiere un control estricto de varios parámetros del proceso, lo que puede aumentar el costo y el tiempo requerido para la producción. Además, algunos tipos de procesos de enchapado, como la galvanoplastia, requieren una cantidad sustancial de electricidad y generan aguas residuales, que pueden ser peligrosas para el medio ambiente. A pesar de estas limitaciones, el proceso de recubrimiento sigue siendo un método de tratamiento de superficies popular y rentable para diversas aplicaciones.
ventajas | Contras |
Deposición de una fina capa de metal sobre la superficie de un sustrato | Requiere un control estricto de varios parámetros, lo que aumenta el costo y el tiempo de producción |
Mejora las propiedades de la superficie del sustrato. | Ciertos tipos de procesos de enchapado generan aguas residuales y consumen una cantidad significativa de electricidad, lo que puede ser dañino para el medio ambiente. |
Versátil y se puede realizar en una variedad de sustratos | |
Diferentes tipos disponibles, lo que permite varias propiedades y acabados. |
Métodos de inspección de calidad de chapado
La inspección y el control de calidad son cruciales en el proceso de enchapado para garantizar resultados consistentes y de alta calidad. Algunos de los métodos de control de calidad más comunes incluyen medir el grosor y la fuerza de adhesión de la capa revestida, inspeccionar visualmente la superficie en busca de defectos y probar la resistencia a la corrosión, la resistencia al desgaste y la conductividad eléctrica de la capa revestida. Estas pruebas generalmente se realizan utilizando técnicas no destructivas como la fluorescencia de rayos X y la inducción magnética. Además de las pruebas, es importante controlar varios parámetros del proceso, como la composición y el valor de pH de la solución de recubrimiento, la temperatura y la tasa de agitación, y la densidad de corriente, para mantener la calidad y la consistencia de la capa recubierta. Los sistemas de monitoreo y retroalimentación en tiempo real pueden ayudar a identificar y corregir las desviaciones del proceso, asegurando que los productos finales cumplan con las especificaciones deseadas y los requisitos de rendimiento. Mediante la implementación de un riguroso sistema de control de calidad, Plating Process puede producir productos de alta calidad, confiables y rentables para diversas aplicaciones.
En los sistemas de refrigeración pequeños que utilizan tubos capilares, la adición de demasiado líquido puede causar reflujo de líquido. Cuando la escarcha del evaporador es grave o el ventilador falla, la transferencia de calor se vuelve deficiente y el líquido no evaporado provocará el retorno del líquido. Las fluctuaciones frecuentes de temperatura también pueden hacer que la válvula de expansión no responda y provoque el fenómeno. | Objetivo |
Técnicas de ensayos no destructivos | Mida el espesor y la fuerza de adhesión de la capa plateada usando XRF o inducción magnética |
Inspección visual | Inspeccione la superficie en busca de defectos visualmente |
Ensayos de resistencia a la corrosión | Pruebe la resistencia a la corrosión de la capa chapada mediante la prueba de niebla salina |
Prueba de resistencia al desgaste | Pruebe la resistencia al desgaste de la capa chapada mediante pruebas de rayado |
Pruebas de conductividad eléctrica | Pruebe la conductividad eléctrica de la capa plateada usando pruebas de resistencia |
Parámetros de control de procesos | Controle los parámetros del proceso, como la composición de la solución de recubrimiento, la temperatura, etc. |
Sistemas de monitoreo en tiempo real | Identifique y corrija las desviaciones del proceso en tiempo real para garantizar resultados consistentes |
Cooling Water Requirements in Anodizing&Plating Process
El control de la temperatura es un factor crítico tanto en los procesos de anodizado como de revestimiento. La solución de recubrimiento o solución electrolítica utilizada en ambos procesos tiene un rango de temperatura que debe mantenerse dentro de una tolerancia específica. La temperatura de la solución de revestimiento o de la solución de electrolitos afecta la tasa de revestimiento, el espesor, la calidad y las propiedades de la capa de revestimiento. Por ejemplo, si la temperatura es demasiado alta, la capa chapada puede volverse porosa, quebradiza o tener poca fuerza de adhesión. Por otro lado, si la temperatura es demasiado baja, la velocidad de recubrimiento puede ser demasiado lenta, lo que puede provocar una deposición desigual o propiedades inconsistentes. Para mantener el rango de temperatura adecuado, los sistemas de control de temperatura, como enfriadores o calentadores, se utilizan comúnmente para regular la temperatura de la solución electrolítica o de revestimiento. La temperatura del agua de enfriamiento utilizada en el sistema de control de temperatura también es importante y debe controlarse cuidadosamente para garantizar que la temperatura de la solución electrolítica o de revestimiento se mantenga dentro del rango deseado. En las siguientes secciones, analizaremos los requisitos de agua de refrigeración y el papel de los enfriadores en los procesos de anodizado y chapado.
Application of Chiller in Anodizing&Plating Process
Chillers play a critical role in maintaining the proper temperature range in Anodizing&Plating Process. Chillers are commonly used to cool the plating or electrolyte solution to maintain the proper temperature range for consistent plating results. Chillers remove the excess heat generated by the Anodizing&Plating Process and maintain the temperature within the desired range. The cooling capacity of the chiller must be matched to the specific requirements of the Anodizing&Plating Process to ensure proper temperature control. Different types of chillers, such as air-cooled or water-cooled chillers, may be used depending on the application and process requirements. The chiller can also provide additional benefits, such as increased energy efficiency, reduced water usage, and improved equipment lifespan. In addition to providing temperature control, chillers can also offer other features such as flow rate monitoring and automatic temperature control to help maintain optimal process conditions. The proper application of chillers can help to ensure consistent and high-quality results in Anodizing&Plating Process.
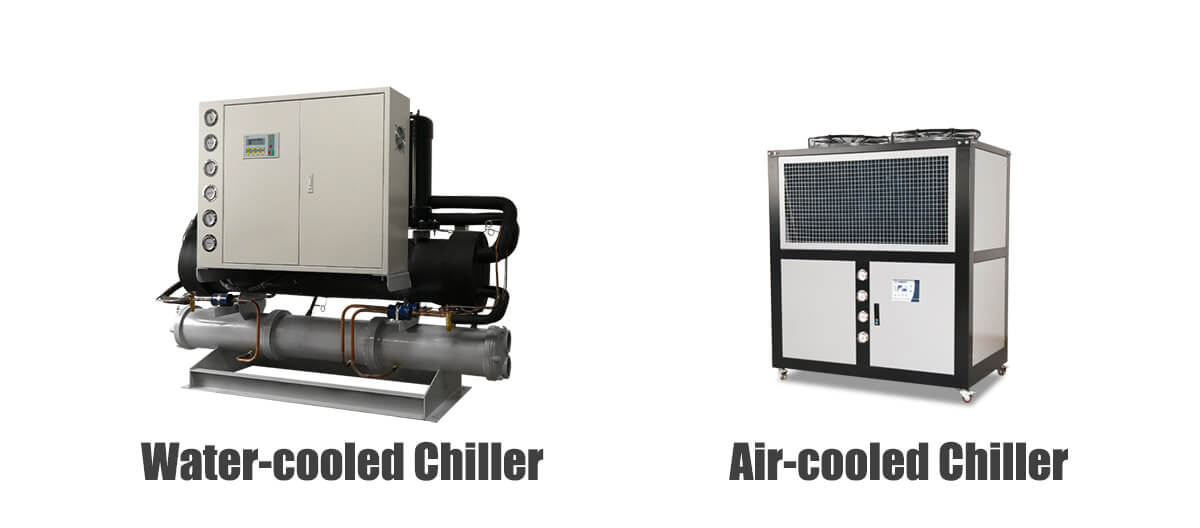
Puntos clave para la selección y configuración de enfriadores
- Capacidad de enfriamiento: The cooling capacity of the chiller should be matched to the specific requirements of the Anodizing&Plating Process to ensure proper temperature control. The cooling capacity of the chiller is typically measured in tons or kilowatts and should be selected based on the heat load of the process. If you have data like the temperature difference of in&out water, and the flow rate of the solution, please refer to our Reste su temperatura inicial de su temperatura actual y registre el resultado, que se conoce como diferencial de temperatura..
- Tipo de enfriador: El tipo de enfriador, como enfriado por aire o enfriado por agua, debe seleccionarse en función de los requisitos específicos de la aplicación y el proceso. Enfriadores refrigerados por agua suelen ser más eficientes y pueden proporcionar mayores capacidades de enfriamiento, pero requieren acceso a una torre de enfriamiento y consumen más agua. Enfriadores refrigerados por aire, por otro lado, son más fáciles de instalar y mantener, pero tienen capacidades de enfriamiento más bajas y requieren más espacio para ventilar el calor residual.
- Rango de control de temperatura: The chiller should be able to maintain the temperature of the plating or electrolyte solution within a specific range. The range is typically determined by the specific requirements of the Anodizing&Plating Process, and the chiller should be selected based on its ability to maintain the required temperature range.
- Caudal y presión: El caudal y la presión del agua de refrigeración deben ser compatibles con los requisitos del enfriador. El caudal y la presión pueden afectar el rendimiento y la eficiencia del enfriador, por lo que es importante asegurarse de que el sistema de agua de refrigeración esté diseñado y configurado correctamente.
- Eficiencia energética: Se debe considerar la eficiencia energética del enfriador para minimizar los costos operativos y reducir el impacto ambiental. Los enfriadores energéticamente eficientes pueden ayudar a reducir los costos de energía y las emisiones de gases de efecto invernadero.
- Mantenimiento y servicio: El enfriador debe ser fácil de mantener y reparar para minimizar el tiempo de inactividad y garantizar un funcionamiento confiable. El mantenimiento regular, como la limpieza del intercambiador de calor y el reemplazo de filtros, puede ayudar a mantener el rendimiento del enfriador y prolongar su vida útil.
By considering these key points, it is possible to select and configure a chiller that meets the specific requirements of Anodizing&Plating Process and provides reliable, efficient, and cost-effective temperature control.
Solución de problemas del enfriador
Proper maintenance and operation of a chiller are crucial for reliable and consistent temperature control in Anodizing&Plating Process. However, if a problem does occur, it is important to be able to troubleshoot the issue and identify the root cause of the problem. Common issues with chillers can include low refrigerant levels, clogged filters, or failed components such as compressors or heat exchangers. In some cases, the problem may be related to the cooling water system rather than the chiller itself, such as issues with water flow or pressure. Troubleshooting can involve various methods such as visual inspection, measuring temperatures and pressures, or using diagnostic tools such as vibration analysis. By identifying and addressing the root cause of the problem, it is possible to minimize downtime and ensure that the Anodizing&Plating Process can continue to operate at optimal performance levels. Regular maintenance and monitoring can also help to prevent issues from occurring and ensure that the chiller and cooling water system are operating reliably and efficiently. For more detailed troubleshooting information, please refer to Lista de verificación de las 10 fallas principales del sistema de refrigeración.
Innovative Technologies in Anodizing&Plating Process
Advancements in technology have led to the development of new and innovative approaches for Anodizing&Plating Processes. These technologies can offer benefits such as improved efficiency, reduced environmental impact, and enhanced performance.
Por ejemplo, el recubrimiento por pulsos es una técnica que utiliza una corriente intermitente para depositar iones metálicos en un sustrato, lo que resulta en una mejor adherencia y uniformidad.
Otro ejemplo es el uso de metalizado sin electricidad, que implica la deposición de una capa de metal sobre un sustrato sin necesidad de una fuente de alimentación externa. Esta técnica puede dar como resultado propiedades mejoradas como la resistencia a la corrosión y la dureza.
In addition, various nanotechnology-based approaches, such as the use of nanostructured coatings or surface modifications, are being explored for Anodizing&Plating Process to enhance the performance and durability of plated surfaces. These innovative technologies have the potential to revolutionize the Anodizing&Plating Process industry and offer new possibilities for advanced surface treatments.
Conclusión
Anodizing&Plating Process plays a crucial role in many industrial applications by providing enhanced surface properties, such as corrosion resistance, wear resistance, and improved aesthetics. The processes are widely used in various industries such as automotive, aerospace, electronics, and medical devices. The high demand for these processes has led to the development of new technologies and approaches for improving efficiency, performance, and sustainability. The use of chillers and temperature control systems is critical for maintaining the proper temperature range and ensuring consistent and reliable plating results. Advanced technologies such as pulse plating, electroless plating, and nanotechnology-based approaches offer exciting possibilities for the future of Anodizing&Plating Process. As industrial applications continue to grow and evolve, the demand for Anodizing&Plating Process is expected to increase, driving further advancements in technology and new approaches to surface treatments.
Status and Role of Chiller in Anodizing&Plating Process
Chillers play a critical role in the Anodizing&Plating Process industry by providing reliable and efficient temperature control for plating solutions and electrolyte solutions. The use of chillers is widespread and essential for ensuring consistent plating results and maintaining high product quality. In addition, chillers offer benefits such as improved energy efficiency, reduced water usage, and longer equipment lifespan. As new plating and surface treatment technologies continue to emerge, the role of chillers is expected to become even more important in ensuring optimal process conditions and performance. As a result, the Anodizing&Plating Process industry is likely to continue to rely on chillers and other temperature control systems for the foreseeable future.
Professional Anodizing&Plating Process Chiller Supplier
If you’re in need of a reliable and efficient chiller for your Anodizing&Plating Process, look no further than SCY Chiller. Our chillers are designed to provide precise temperature control for a wide range of industrial applications, including plating and surface treatment processes. We offer a variety of chiller types, such as air-cooled and water-cooled chillers, to meet your specific needs and requirements. Our chillers are energy-efficient, easy to operate, and require minimal maintenance, ensuring that your Anodizing&Plating Process runs smoothly and efficiently. Contáctenos today to learn more about our chiller solutions and how we can help optimize your Anodizing&Plating Process.