Muy bien, hablemos de los condensadores de enfriadores, la parte de un sistema de enfriamiento que no recibe suficiente amor pero hace un trabajo muy pesado. Imagine esto: estás en una oficina sofocante o una fábrica zumbando con máquinas, y algo está evitando que todo se convierta en una sauna. Ese es el condensador trabajando su magia, pateando el calor para que el enfriador pueda mantener las cosas frescas. Ya sea que sea un gurú de HVAC, un gerente de edificios que suda las facturas de energía, o simplemente alguien a quien le gusta saber cómo funcionan las cosas, lo tengo cubierto. Analicemos lo que hacen estas cosas, cómo lo hacen y por qué son un gran problema.
¿Qué es un condensador de enfriadores de todos modos?
Imagine un enfriador como una aspiradora de calor: chupa el calor de un espacio o proceso y necesita un lugar para tirarlo. Ahí es donde interviene el condensador. Toma gas refrigerante caliente y presurizado directamente del compresor y lo convierte en un líquido arrojando todo ese calor en el aire o el agua afuera. Es como el tubo de escape de su sistema de enfriamiento, sin que el calor no haya llegado a dónde ir y la tostada de su enfriador.
Tienes dos tipos principales: refrigerado por aire, que usa ventiladores para volar el calor y el agua, que se inclina en el agua de una torre de enfriamiento o alguna otra fuente. Estos chicos malos están en todas partes, pequeñas unidades de 5 toneladas en los tejados, configuraciones monstruosas de 1,000 toneladas en fábricas, que manejan refrigerantes como R-410a o amoníaco y patean calor a velocidades locas, como un millón de BTU por hora en las grandes ligas.
¿Cómo funciona realmente?
Vamos a atravesarlo como si estuviéramos siguiendo el refrigerante en su viaje. Es parte del ciclo de enfriadores, donde el condensador es la parada en boxes de tambor:
- Rollos de gas caliente en: El compresor acaba de apretar el refrigerante en un gas de alta presión y caliente, piense en 150 ° F (66 ° C) y 300 psi. Lleva todo el calor que agarró desde el interior, y está listo para descargar.
- El calor tiene que irse: En un condensador refrigerado por aire, grandes ventiladores, a veces, a media docena de girando a 900 rpm, aire exterior (digamos, 95 ° F o 35 ° C) sobre una bobina gigante con aletas. En uno refrigerado por agua, el agua (tal vez 85 ° F o 29 ° C de una torre) fluye a través de tubos o una carcasa. De cualquier manera, el gas se enfría a aproximadamente 110 ° F (43 ° C) a medida que el calor salta.
- Tiempo de líquido: Una vez que se arroja suficiente calor, el refrigerante se convierte en un líquido de alta presión, todavía cálido, pero ya no hirviendo. Ese es el truco de calor latente, arrojando 80-100 BTU por libra en el aire o el agua.
- Adelante: El líquido se dirige a la válvula de expansión para relajarse aún más, mientras que los ventiladores o el agua siguen arrastrando el calor.
Es un concierto sin parar. El condensador de un enfriador de 100 toneladas podría empujar 1,2 millones de BTU por hora, como derretir una tonelada de hielo literal cada 15 minutos. Salvaje, ¿verdad?
Refrigerado por aire versus refrigerado por agua
Los condensadores vienen en dos sabores, y cada uno tiene su ambiente:
- Refrigerado por aire: Imagine un gran radiador con los fanáticos. La bobina tiene tubos de cobre y aletas de aluminio, a veces de 20 pies de largo, y mueve 20,000 cfm de aire en una unidad de 50 toneladas. Es un chapoteo bajo: no hay líneas de agua, solo conéctelo y vaya. Pero cuando se abre afuera (100 ° F+ o 38 ° C+), suda un poco más duro, y esos ventiladores pueden volverse fuertes (70-80 dba, como una aspiradora.
Condensador refrigerado por agua - Refrigerado por agua: Piense en tubos elegantes o una cáscara donde el agua se levanta pesada. Una unidad de 200 toneladas podría enganchar 600 gpm de una torre de enfriamiento. Es más tranquilo (60 dBA) y más eficiente, recortes de hasta 5.0 frente a 3.5 para refrigerado por aire, pero estás atrapado con bombas de agua y mantenimiento de la torre.
Condensador enfriado por aire
También hay condensadores evaporativos: aire y agua que se unen en una bobina húmeda. Son nicho pero asesinos en calor seco, golpeando a los policías alrededor de 4.5.
¿Qué hay dentro de un condensador?
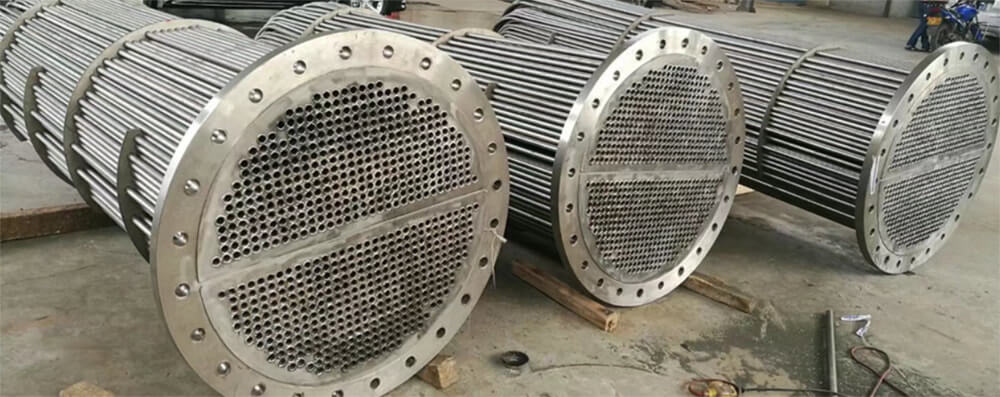
Aquí está el equipo que lo hace tick:
- Bobinas/tubos: Cobre para flujo de calor, aletas o conchas para una superficie adicional, hasta 1,000 pies cuadrados en grandes unidades.
- Fans (refrigerado por aire): Axial, a menudo variable, de velocidad, arrancando 10,000-50,000 CFM. Son la parte ruidosa.
- Bombas (refrigeradas por agua): Empuje 2-3 gpm por tonelada-10-20 hp para los perros grandes.
- Aletas: Aluminio, empaquetado de 8-12 por pulgada, grande para el contacto de aire, pero los imanes de polvo.
- Control: Los sensores observan la presión (250 psi-ish) y ajustan ventiladores o bombas para mantenerla suave.
Los modelos elegantes agilizan el subenfriamiento, el líquido de 10 ° F (6 ° C) por debajo de la temperatura de condensación, para exprimir un 5-10% más de eficiencia. Menos gas en la válvula de expansión, más frío para su dinero.
Por qué los condensadores son los MVP reales
Sin un condensador sólido, su enfriador es solo una trampa de calor. He aquí por qué rockan:
- Volteo: Una unidad de 300 toneladas podría abandonar 3,6 millones de BTU/hora, manteniendo un almacén a 70 ° F (21 ° C) mientras el sol está ardiendo.
- Impulso de eficiencia: Los refrigerados por agua ahorran jugo serio en puntos calientes: 20-30% menos de energía que el aire refrigerado cuando está vaporizado.
- Línea de vida del sistema: Si el condensador se aflige, los picos de presión del compresor, cada 2 ° F (1 ° C), la temperatura de los saltos corta la capacidad del 1%. Ay.
Donde los detectarás
- Oficios: Un condensador refrigerado por aire de 150 toneladas en un techo mantiene los cubículos a 72 ° F (22 ° C), sin problemas de agua.
- Plantas alimenticias: Una unidad refrigerada por agua de 500 toneladas se enfría un congelador a 0 ° F (-18 ° C), bebiendo agua de la torre a 90 ° F (32 ° C).
- Centros tecnológicos: Los centros de datos se apoyan en condensadores refrigerados por aire de 100 toneladas: 30,000 CFM que mantienen servidores a 68 ° F (20 ° C).
- Fábricas: Los moldes de plásticos alcanzaron 50 ° F (10 ° C) gracias a la bobina compacta de una unidad de 50 toneladas.
Tome una cervecería: 75 toneladas de bondad refrigerada por agua mantienen los tanques de fermentación a 55 ° F (13 ° C). Tranquilo, barato de correr y la cerveza es crujiente.
Conclusión
Los condensadores son los campeones de enfriadores de aliento o agua, hacen que el enfriamiento ocurra. From rooftops to factory floors, they’re the difference between comfy and crispy. ¿Tienes un concierto de Chiller? Conocer a los condensadores es su as, suplique un profesional para clavar el correcto y mantener el calor donde pertenece, ¡fuera!